不良の発生原因を調査しても、一向に解決しないのはなぜ?
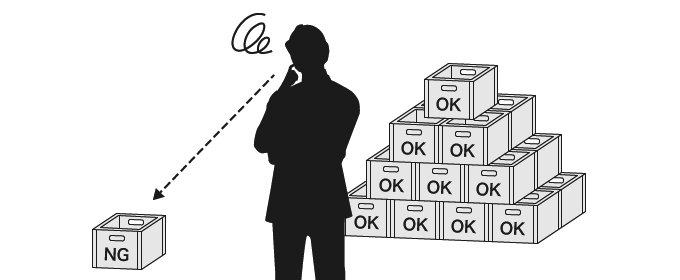
ある工場では、樹脂成形品の4%にバリによる不良品が発生し、問題になっていました。管理者は「4%のエラーの原因」を探るため、すぐさま設備や金型を調べ、作業者や設備設計者にヒアリングを繰り返すなど、不良原因の調査・究明に四苦八苦。しかし、原因は一向に解明できません。
大量生産において、4%の不良は無視できないロスですが、裏を返せば「96%の良品ができている」という状況でもあります。つまり、良品ができる条件のほうが圧倒的に多いといえます。これまでの量産試作や生産から製造条件が変化していることも考えられます。
- この記事でわかること
良品の条件を追及する
下記の例のように、まず良品ができた条件を振り返ることで、不良発生の問題を解決できる場合があります。
- 不具合発生の例
- 樹脂成形(射出成形)で良品(96%)と不良品(4%)が、同じ成形条件(温度とショットタイム)で発生している。
- 良品から原因究明の例
- 1. 良品が大多数だったこの条件から、温度とショットタイムをそれぞれ少しずつ変える実験を行う。
- 2. 1の実験で「良品だけができる領域」の方向性を探る。
- 3. 2の方向性から100%「良品ができる領域(=成形条件) 」をみつける。
→不良原因を研究する必要がなくなる(=不良の問題を解決している)。
変化への気づきと対策
もし上記の方法で「良品ができる領域」がみつからない場合、装置や金型などの不具合が考えられるため、広範囲な調査が必要となります。しかし、テクノロジーを活用することで、これらの作業を大幅に省略することができます。
普段から温度や装置などをセンシングし、複数データによる状態監視で、どこに変化が生じたか素早く察知できるほか、データの記録・分析により予知保全にも役立てることができます。
- 関連ページ
トラブル時こそ、発想を転換
樹脂成形に限らず、前途の例のように発想を転換することで、本来は不必要だった原因究明の作業を大幅に省略できる場合があります。
「木を見て森を見ず」ということわざのように、人はつい近くにある「気になる木」に注目しがちです。しかし、この「気になる木」が生まれた「森」に、ヒントが隠れていることは少なくありません。少し視点を変えてみることで、良い結果を早く導き出せるケースもあります。このような視点や発想の転換は、ものづくりの醍醐味である「ひらめき」や「発明」にも通ずるものかもしれませんね。
- 関連ページ