ベアリングの摩耗・トラブルを測定する方法
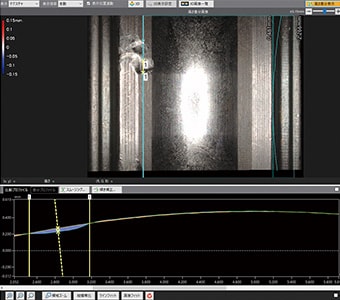
ベアリングの品質は、動作の滑らかさと耐久性で評価されます。その動作の滑らかさは省エネや動作精度に、また耐久性は耐用年数に直結します。ベアリングの素材や構造、給油方式、密閉性については、日々進歩しており、メンテナンス不要の製品も開発されています。しかし、どのような構造であっても、摺動部品である限り摩耗や損傷といったトラブルは避けられません。
ここでは、ベアリングに発生するトラブルやベアリングの精度の測定方法と課題、さらにその課題の解決方法をご紹介します。
ベアリングとは
ベアリングは「軸受」ともいわれ、回転する軸の回転がブレないよう支えます。高温下、低温下での動作に耐える耐候性、高荷重・高速回転に耐える耐久性が求められる部品で、自動車や自転車、家電製品はもちろん、航空機まで幅広い分野の製品に使用されています。
ベアリングの種類と荷重
ベアリングのトラブルの多くは、ボールやころ、軸と、それを受ける部分との摩擦面で発生します。トラブルの種類は、大きく摩耗と傷に分けられ、発生の原因には使用による劣化以外に外部からの衝撃や組み付け不良などがあります。そして、トラブルの対策は、ベアリングの構造やベアリングにかかる荷重によって異なります。
ベアリングの種類
ベアリングは、大きく分けてボールやころといった転動体を持つボールベアリングやローラーベアリングと、転動体の代わりに潤滑剤をつかうスライドベアリングがあります。
- ボールベアリング・ローラーベアリング・ニードルベアリング:
- これらのベアリングは、玉や円筒状のころで軸を支えます。玉を使ったものは「ボールベアリング(玉軸受)」といいます。また、ころを使ったものは「ローラーベアリング(円筒ころ軸受)」「ニードルベアリング(針状ころ軸受)」といわれ、負荷能力が高く、ボールベアリングと比べて薄肉に作ることができます。
- スライドベアリング:
- 滑り軸受ともいわれます。「メタル」や「平軸受」とも呼ばれ、軸とベアリングの面が直接接触します。内部には、潤滑用の油が封入されており、摩擦を低減します。回り始めは潤滑油の膜が回転の抵抗になりますが、回転が安定すると機械的接触がないため抵抗が小さくなります。回転中は接触面がないため、静かで高速回転・衝撃荷重に強いという特徴があります。

- A
- ボールベアリング
- B
- 軸

- B
- 軸
- C
- スライドベアリング
- D
- 潤滑剤
ベアリングにかかる荷重
ベアリングにかかる力は、「ラジアル荷重」「アキシャル荷重」「モーメント荷重」に分類されます。
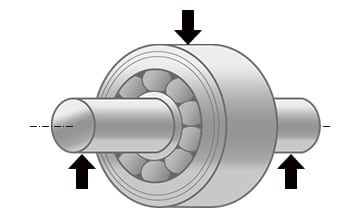
- ラジアル荷重:
- ベアリングの中心線に対し垂直な方向(回転体の円周方向)にかかる荷重です。
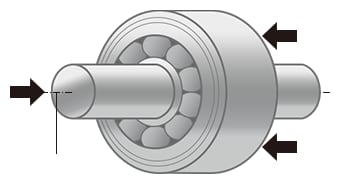
- アキシャル荷重:
- 「スラスト荷重」ともいいます。ベアリングの中心線に対し平行な方向(回転体の軸方向)にかかる荷重です。
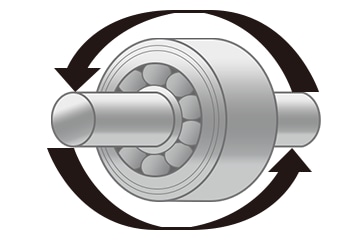
- モーメント荷重:
- ベアリングや軸の偏心によって発生する荷重です。この荷重が発生している場合、軸受の寿命は極端に低下します。
ベアリングのトラブル
ベアリングの代表的なトラブルには、摩耗やフレーキング、かじり、ピーリングなどがあります。その他、取付時や落下時の衝撃・過大荷重が原因である圧痕、すき間の過小や過大荷重が原因であるスミアリング、潤滑不良や取り付け不良が原因である電食などがあります。これらのトラブルは、表面を測定/観察することで、その原因がわかります。
ここでは、代表的なトラブルである摩耗、フレーキング、かじり、ピーリングの損傷状態、原因、対策について紹介します。
摩耗
摩耗には、多くの原因があり、ベアリングに現れる現象もさまざまです。
- 損傷状態:
- 表面が摩耗し、寸法変化を起している。荒れ、傷がある。
- 原因:
- 潤滑剤への固形異物の浸入。潤滑不良。嵌合面のすき間過小。
- 対策:
- フィルタによる潤滑剤のろ過または潤滑剤、潤滑方法の改善。密封性能の強化。しめしろを大きくする。
フレーキング
フレーキングとは剥離のことです。軌道面や転動面に現れるトラブルで、ベアリングの寿命により発生します。ただし、早期に発生した場合はただちに原因を突き止め、何らかの対策が必要です。
- 損傷状態:
- 軌道の全周がうろこ状に剥がれる。剥がれた後に玉ピッチの凹凸ができる。
- 原因:
- 組み付け不良や軸の膨張による過大なアキシャル荷重。異物の浸入、さびの発生。
- 対策:
- 組み付け精度の見直し。荷重の適正化。潤滑剤の粘度を上げ、潤滑方法を改善する。運転休止が長期におよぶ場合の防錆。
かじり
熱の影響で、表面が局部的に溶着する現象です。アキシャル方向に発生します。
- 損傷状態:
- 軌道・転動面の焼き付きを伴う傷。
- 原因:
- 脱着時の取り扱い不良。過大なアキシアル荷重による接触面の潤滑剤不足または潤滑不良。過大予圧。転動体の滑り。
- 対策:
- 脱着方法の改善。荷重の軽減と潤滑剤および潤滑方法の改善。密封性能の強化。
ピーリング
軌道面に発生する摩耗を伴ったくすみです。一般に、ニードルベアリングに多く発生します。また、ピーリングからフレーキングに進行することがあります。
- 損傷状態:
- 表面が数μmから10μmの深さで剥離し、広範囲に発生する。
- 原因:
- 潤滑剤が適切でない。潤滑剤への異物混入。潤滑不良。相手部品の表面が粗い。
- 対策:
- 適切な潤滑剤を選定する。潤滑剤のフィルタリング。部品の粗さの改善。
従来のベアリング測定の課題
多くの場合、ベアリングのトラブルは外輪や内輪、ボールやころなどに発生します。したがって、これらの箇所を測定することで、摩耗やフレーキング・かじり・ピーリングなどの発生を確認することができます。
従来は、ベアリングの測定に形状測定機を使用していました。しかし、ベアリングの形状は複雑であるため、以下のような測定課題がありました。
輪郭形状測定機によるベアリング測定の課題
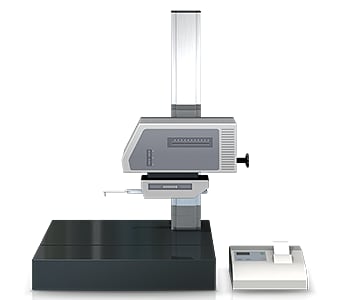
輪郭形状測定機は、スタイラスと呼ばれる触針を用いて対象物の表面をなぞることで、その輪郭形状を測定、記録する装置です。近年は触針の代わりにレーザーを用いて、非接触で輪郭をなぞることで複雑な形状の測定に対応した機種もあります。また、機種によっては上下両面の測定が可能なものもあります。
輪郭形状測定機では、測定したいベアリングのトラブルに対して、正確な測定ラインを取る必要があります。
そこで、下記のような課題がありました。
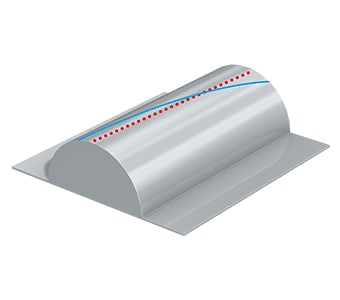
- サンプルを治具に固定したり、水平出ししたりなどの作業に時間がかかってしまいます。また、正確に水平出しするためには、輪郭形状測定機に関する知識やスキルが必須です。
- 輪郭形状測定機の触針は、触針アーム上の支点を中心に上下に円弧運動し、触針先端位置はX方向にも動くため、X軸データにも誤差が発生します。
- 狙った通りに針を通す作業は非常に困難で、微妙な針のズレが測定値のバラつきの原因となります。
- 特定の箇所を狙って測定する必要があるので、N増しが困難です。
- 一部の測定値しか取れないので、面での評価ができません。
三次元測定機の測定課題
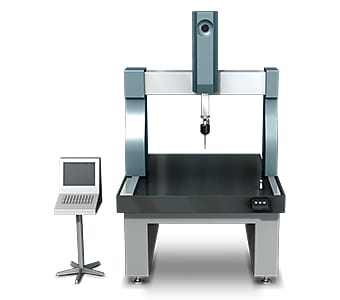
たとえば、測定する部分の面積が1mm2と小さい場合、その箇所をプローブで狙って仮想面を作成し、正確に測定することは困難を極めます。また、小さな部分の三次元形状を測定する場合、測定点が少なくなり正確な形状把握が困難です。さらに、測定データの集計や図面との照合など、多くの手間が必要です。
ベアリング測定における課題解決方法
輪郭形状測定機には、立体的な対象物・測定箇所に対して点や線で接触しながら測定しているため全体の形状が把握できない、測定値の信頼性が低い、という課題があります。こうした測定の課題を解決すべく、キーエンスでは、ワンショット3D形状測定機「VRシリーズ」を開発しました。
対象物の3D形状を非接触で、かつ面で正確に捉えることができます。また、ステージ上の対象物を最速1秒で3Dスキャンして3次元形状を高精度に測定することができます。このため、測定結果がバラつくことなく、瞬時に定量的な測定を実施することが可能です。ここでは、その具体的なメリットについて紹介します。
メリット1:3D形状を面で測定
測定に必要な作業は、対象物をステージに置いて、ボタンを押すだけ。厳密な位置決めなどの事前準備が不要なので、測定機の知識や経験がなくても、すぐに高精度な測定が可能です。

輪郭形状測定機と異なり、ステージに置いた対象物の特徴を抽出し自動的に位置補正することができるので、測定作業が属人化することなく不慣れな方でも簡単・瞬時に測定することができます。また、最大200mm×100mmの広範囲を連結して測定することができ、ステージ上に置いた複数の対象物を同時に測定することもできます。
「VRシリーズ」なら、ベアリングのような複雑な形状の対象物も、ステージに置いてボタンを押すだけの操作で、正確な形状測定が可能です。
メリット2:バラつきのない測定を可能にする豊富な補助ツール
スキャンした3D形状のデータに対して、パソコンの画面上でツールを使って、任意の位置に正しく垂直なプロファイル線を引くことができるため、測定結果にバラつきが生じません。

さらに、豊富な補助ツールを使用することで、目的の測定内容を簡単に設定することができます。たとえば、ツールの垂直線ツールを使うと、ベアリングの外径の測定ラインを簡単かつ正確に決定できます。


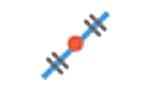

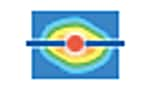



簡単設定に加えて、初心者でも簡単な操作を実現しているため、測定に不慣れな人でも最速1秒で正確な測定が可能です。そのため、試作品やトライだけでなく、製品の測定・検査におけるN数増やしも簡単に実現します。
まとめ:ベアリングの形状測定の課題を根こそぎ改善・効率化
「VRシリーズ」なら、高速3Dスキャンにより非接触で対象物の正確な3D形状を瞬時に測定可能。ボールやころ、軌道溝の摩耗状態など難しい測定も最速1秒で完了できます。従来の測定機における課題をすべてクリアすることができます。
- 非接触かつ面で捉えるので、触針が届かない部分も断面測定が可能。小さなベアリングも簡単かつ正確に測定することができます。
- 豊富な補助ツールで人による測定値のバラつきを解消。定量的な測定が実現します。
- 位置決めなどなしに、ステージに対象物を置いてボタンを押すだけの簡単操作を実現。測定作業の属人化を解消します。
- 簡単・高速・高精度に3D形状を測定できるため、短時間で多くの対象物を測定することができ、品質向上に役立てることができます。
他にも、過去の3D形状データやCADデータとの比較、公差範囲内での分布などを簡単に分析できるため、製品開発や製造の傾向分析、抜き取り検査などさまざまな用途で活用することができます。