鋳造品を誰でも簡単・正確に測定する方法

鋳造で作った製品は、圧延加工や鍛造加工で作った製品に比べると強度は劣るものの、複雑な形状や大型の製品の加工に向いています。また、大量生産が可能で製造コストを抑えることができるというメリットがあります。この利点を活かし、自動車など輸送機器の部品や産業機械、電気・通信機器から日用品まで、幅広い分野の部品の製造に用いられています。
しかし、鋳造時の金属の粘度や温度・異物混入などが原因で、製品の内部や外部に不良が起こりやすいといった特性もあります。
そこで、ここでは主な鋳造の方法とトラブルの種類、開発・設計における試作品測定、および量産における不良流出を防止するための測定方法を解説。さらに、従来の測定方法の課題とソリューションを紹介します。
鋳造とは
鋳造とは、溶融金属、または溶湯といわれる溶かした金属を作りたい形の空洞部に流し込み、冷やして固める金属加工法です。作りたい形の空洞部を持つ型を「鋳型(いがた)」といい、できた製品を「鋳物(いもの)」といいます。鋳型には金属を削って作った金型や砂で作った砂型、樹脂や石膏で作った型などがあり、中でも金型と砂型が一般的です。鋳物の材料には目的に応じて鋳鉄や鋳鋼、アルミニウム合金やマグネシウム合金などが使い分けられます。

- A
- 鋳型(上型)
- B
- 鋳物
- C
- 鋳型(下型)
鋳造の種類
鋳造には、鋳型の材料によるものや造型法によるもの、模型の種類によるものなどさまざまな分類法があります。ここでは、最も一般的である鋳型の材料による分類に注目し、中でも砂型鋳造と金型鋳造・ロストワックス鋳造法の種類について説明します。
砂型鋳造
砂型鋳造とは、作りたい形と同じ形を砂で作り、そこに溶融金属を流し込んで冷やして固める鋳造法です。鋳型を作る砂は「鋳物砂(いものずな)」といわれ、珪砂の粒にベントナイト(粘土鉱物)や水ガラス、または樹脂などの粘結剤や添加剤を混ぜて作ります。そして、この鋳型を「砂型」といいます。
複雑な形状にも対応でき、少数生産なら金型鋳造より安価で早く鋳物を作ることができます。一方、砂型鋳造で作られた鋳物は一般に寸法精度に劣り、鋳造時の冷却速度が遅いため強度に欠けます。また、1度鋳造するたびに砂型を破壊するため、大量生産ではランニングコストが高くなります。
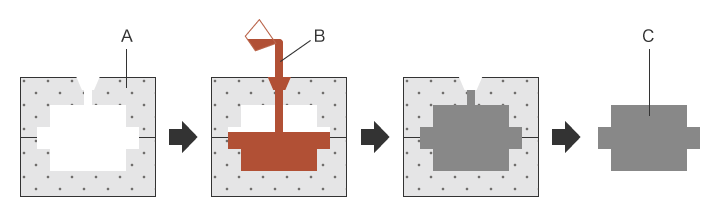
- A
- 砂型
- B
- 溶融金属
- C
- 鋳物
金型鋳造
金型鋳造とは、金属でできた鋳型に溶融金属を流し込んで冷やして固める鋳造法です。

- A
- 溶融金属
- B
- 鋳型(上型)
- C
- 鋳物
- D
- 鋳型(下型)
- E
- 溶湯
- 重力鋳造法(グラビティ鋳造):
-
重力鋳造法では、溶融金属は重力で充填します。砂型鋳造も同じ充填方法ですが、鋳型が何度も使えるため、大量生産に向いています。溶融金属の冷却速度が速いため、機械的特性に優れた鋳物を作ることができます。また、溶融金属の充填速度が低速であるため、ダイカスト鋳造法に比べて空気やガスなどを巻き込むことが少なく、圧力をかけないので「中子」といわれる形を使うことができ、これにより中空部がある複雑な形状の鋳物を作ることができます。
これらのメリットから、最も一般的な鋳造法としてさまざまな鋳物の製造に利用されていますが、溶融金属に圧力をかけないため鋳型全体に溶融金属を充填する必要があり歩留まりが低い、充填に時間がかかるのでサイクルタイムが長いといったデメリットもあります。 - 高圧鋳造法:
-
高圧鋳造では、溶融金属をゆっくりと鋳型に充填し、外部から圧力をかけて固めて鋳造します。溶融金属の充填速度が遅いためダイカスト鋳造法に比べて空気やガスなどを巻き込むことが少なく、重力金型鋳造法に比べて圧力が高いため微細な金属組織構造を持った強い機械的性質の鋳物を作ることができます。
圧力をかける方法には、直接加圧と間接加圧があります。直接加圧では、「パンチ」といわれる加圧プランジャで直接溶融金属に圧力をかけます。間接加圧では、プランジャで溶融金属をキャビティ内に充填させつつ圧力をかけます。一般に直接加圧は単純な形状の鋳物の製造に向いており、間接加圧は複雑で中・大型の鋳物の製造に向いているとされます。 - 低圧鋳造法:
- 低圧鋳造法では、加圧した大気圧、または不活性ガス圧により溶融金属を充填します。溶融金属が鋳型の隅々に行き渡り、冷えて固まるまで加圧を保持し続けるため、ひけ巣やブローホールなどの欠陥が発生しにくいというメリットがあります。また、湯口部まで固まった時点で加圧を中止すると、鋳物に不要な溶融金属はるつぼの中に戻ります。このため、砂型鋳造や重力鋳造法に比べて歩留まりが高いという特徴があります。さらに、重力鋳造法と同じく中子が使えるため、中空部がある複雑な形状の鋳物を作ることができます。一方で、冷却に時間がかかりサイクルタイムが長くなるため、生産性が低いというデメリットがあります。
- 遠心鋳造法:
- 遠心鋳造法では、高速で回転する円筒形の鋳型に溶融金属を充填します。溶融金属は遠心力によって鋳型の内壁に押し付けられ円筒形の鋳物が作られます。円筒は縦型と横型があり、縦型は鋳型が垂直に立っており、短い鋳物の製造に使われます。横型は鋳型が水平に設置されており、長い鋳物の製造に使われます。遠心鋳造法では、中子を使わず中空の鋳物を作ることができます。また、湯口や加圧は不要で回転速度を制御することで鋳物の金属密度を変えることができるというメリットがあります。冷却時間が短いため、凝固の早い材料や肉厚が薄いパイプの製造に適しており複雑形状の鋳物の製造も可能で、水道管やガス管・軸受メタル・銀歯などの製造に用いられます。一方で、遠心力により偏析が発生したり、冷却直後に亀裂が発生することがあるなどのデメリットがあります。
- ダイカスト鋳造法:
-
ダイカスト鋳造法では、溶融金属を高速かつ高圧力で鋳型に充填し、短時間で冷却します。緻密で寸法精度の高い鋳造が可能で、サイクルタイムも短いため大量生産に適しています。主に、融点の低いアルミニウム合金や亜鉛合金、マグネシウム合金の鋳造に利用されます。ダイカスト鋳造を行う鋳造機にはホットチャンバーマシンとコールドチャンバーマシンがあります。
ホットチャンバーマシンは溶融金属が入っている炉と鋳造機が一体になっており、主にマグネシウム合金の鋳造に使われます。コールドチャンバーマシンは溶融金属が入っている炉と鋳造機が別で、溶融金属はラドルによって射出部に注湯します。
コールドチャンバーマシンは、主にマグネシウム合金の鋳造に使われます。高速で緻密で寸法精度が高い鋳造が可能なダイカスト鋳造法ですが、一方で、溶融金属を高速で鋳型に充填するため、空気や離型剤などを鋳物に巻き込む可能性があるというデメリットがあります。このため、ダイカスト鋳造法で作った鋳物は強度が必要な部品に使用することはできません。
ロストワックス鋳造法
ロストワックス鋳造法は精密鋳造法の一種で、「インベストメント鋳造法」ともいわれます。融点の低いパラフィン・レジン・フィラーなどを混ぜたもので模型を作り、その周りをセラミックスなどの耐火性の材料で包んで内部の模型を溶かして流し出し、鋳型を作ります。鋳型を分解しなくても良いため砂型鋳造や他の金型鋳造では不可能な複雑な形状であっても鋳造でき、鋳型がセラミックスなど耐火性なので、炭素鋼やステンレス鋼など融点が高い材料の鋳造が可能であるというメリットがあります。一方で、鋳型が使い捨てであることから、大量生産には向かないというデメリットがあります。

- A
- 模型
- B
- 耐火性材料(鋳型)
- C
- 脱ろう
- D
- 溶融金属
鋳物に発生する不良
鋳造加工では、さまざまな原因で欠陥が発生します。欠陥は、歩留まりの低下や返品・リコールの原因となるため、迅速な原因の究明と対策が必要です。ここでは、鋳造で発生する主な欠陥を紹介します。
ひけ巣
鋳型に充填した溶融金属は、冷えてくると収縮します。冷却が進んで凝固が始まるとさらに収縮が進むため、足りない分は凝固していない部分から補給することになります。しかし、凝固が終わると補給できなくなるため、足りない部分は空洞,または凹みになります。この空洞または凹みを「ひけ巣」といいます。
ひけ巣には、外ひけ巣と内ひけ巣があります。外ひけ巣は鋳物の表面の一部に発生する凹みのことで、「外ひけ」ともいわれます。内ひけ巣は鋳物内部に発生する空洞のことで空洞の表面は荒れており青紫色、または黒褐色を帯びています。いずれのひけ巣も最終凝固部に発生し、厚肉部や交差部のほか角や隅、湯口部などに発生します。

- A
- 外ひけ巣
- B
- 鋳型(上型)
- C
- 鋳物
- D
- 内ひけ巣
- E
- 鋳型(下型)
ブローホール・ピンホール
ブローホール・ピンホールは、鋳物内部に丸みのある空洞ができる欠陥です。鋳型に溶融金属を充填する際にガスや空気を巻き込むことで発生します。空洞の大きさによって呼び方が変わり、直径が約2mm以上の空洞を「ブローホール」、それ以下の空洞を「ピンホール」といいます。
原因となるガスは、溶融金属と介在物との化学反応や水分により発生します。また、ダイカスト鋳造など溶融金属を高速で充填する鋳造では、溶融金属が空気を巻き込むことでブローホールやピンホールが発生する場合があります。

- A
- 鋳型(上型)
- B
- ブローホール/ピンホール
- C
- 鋳物
- D
- 鋳型(下型)
割れ
割れとは、鋳物に亀裂が表れる欠陥です。高温時に発生するものと低温時に発生するものがあります。高温時に発生する割れを「高温割れ」といい、最終凝固部に亀裂が生じます。また、低温時に発生する割れを「低温割れ」といい、冷却中や冷却後に亀裂が生じます。また、凝固中に凝固していない部分を凝固した部分が引っ張ってできる亀裂を「ひけ割れ」または「凝固割れ」、肉厚の不均衡により発生する機械的応力や収縮時の応力で生じる亀裂を「ひずみ割れ」といいます。

- A
- 割れ
- B
- 鋳型(上型)
- C
- 鋳物
- D
- 鋳型(下型)
湯回り不良
湯回り不良は、溶融金属が鋳型に行き渡らずに鋳物の形状が不完全になる現象です。薄肉部分や細い部分に発生し、先端部は丸まった形状になります。十分に溶融金属を充填できない場合に起こる欠陥で、原因としては肉厚が薄すぎる・充填速度が遅い・鋳型の温度が低い・鋳型のガス抜きが不十分などが挙げられます。また、溶融金属の充填不良で起こる欠陥には、鋳物の表面に境目が形成される湯境、鋳物の表面に不規則なしわが発生する湯じわなどがあります。

- A
- 鋳物
- B
- 湯じわ
- C
- 湯回り不良
- D
- 湯境
ひずみ(反り・うねり)
鋳物に発生する反りやうねりといったひずみは、鋳造加工の不具合によって発生します。金属を高温で溶かして成形する鋳造では、厚みや部位によって冷却速度に差が発生します。薄い部分は速く冷え、厚い部分や最終充填箇所は冷えるのに時間がかかります。冷えるのに時間がかかる内部が冷えた部分を引っ張るため、残留応力が発生し、ひずみが起こります。


従来の鋳造品の測定課題
鋳物が狙い通りの寸法(公差内)・形状が得られていることの確認は非常に重要です。特に、精密部品や複雑形状の鋳物は強度や動作精度に影響するため、高精度かつ定量的な3D形状の測定が求められます。
従来の三次元測定機や簡易な3Dスキャナなどでは、測定できない箇所があったり測定精度が低かったりで、これらの機器による測定データを基に解析しても不具合の原因を特定できないケースが多くありました。また、測定には多くの時間が必要でした。
三次元測定機での測定課題

一般に、三次元測定機でひけ巣や割れ・湯回り不良などの鋳造欠陥を測定するには、たとえば測定する部分の面積が小さい場合、その箇所をプローブで狙って仮想面を作成し測定します。しかし、この方法では正確に測定することは困難を極めます。また、小さな部分の3D形状を測定する場合、測定点が少なくなり正確な形状把握が困難です。さらに、測定データの集計や図面との照合など、多くの手間が必要です。
3Dスキャナでの測定課題
3Dスキャナはワークを光で照射し反射光で形状を測定できるので、比較的容易に形状測定が可能です。しかし、従来の3Dスキャナは、撮像や処理速度が遅かったり斜面の測定精度が低いなどの問題がありました。さらに、ワークの位置や姿勢によっては正常に測定できなかったり、測定機能が少なかったりと、十分な検査ができませんでした。
鋳造品の測定課題解決方法
鋳造品の品質を担保するには形状の解析が欠かせません。しかし、三次元測定機で測定するには測定機の知識と正確な操作が必要で、高いスキルと長い時間を要します。また、簡易な3Dスキャナでは、多くの場合、システムや精度において研究開発段階や溶接条件出しのためのテスト、不具合発生原因の解析や問題点の早期解決といった目的には向いていませんでした。
このような課題を解決すべく、キーエンスでは、3Dスキャナ型三次元測定機「VLシリーズ」を開発しました。
対象物の3D形状を非接触で、かつ面で正確に捉えることができます。また、ステージ上の対象物を瞬時に3Dスキャンして3D形状を高精度に測定することができます。このため、測定に不慣れな人でも測定結果がバラつくことなく、瞬時に定量的な測定を実施することが可能です。ここでは、その具体的なメリットについて紹介します。
メリット1:「面」で対象物全体の3D形状を一括取得
「VLシリーズ」は、面データ(ワンクリックで1600万点のデータ)を取得することができます。それにより、複雑な鋳造品の3D形状を瞬時かつ高精度に測定し、定量的な評価が可能です。
最大・最小の凹凸をカラーマップでわかりやすく表現でき、不良箇所を判別することができます。また、3D比較した状態のまま、断面計測することが可能です。
測定後であっても対象物を再びセットすることなく、過去に3Dスキャンしたデータから別の箇所のプロファイルデータを取得することもできます。また、複数の対象物の測定データを並べて比較したり、目的の条件を複数のデータに一括適用することができます。
これらの機能により、形状解析にかかる工数を大幅に削減することが可能です。


メリット2:簡単操作で、誰が測っても測定値がバラつかない
対象物をステージの上に置き、ワンクリックするだけの簡単操作で、3D形状の測定を実現しました。対象物の特徴データから自動的に位置補正が可能なため、シビアな水平出しや位置決めは不要です。また、対象物の大きさを判断して測定範囲を自動設定する、「Smart
Stage機能」を搭載し、測定長やZ範囲などを設定する手間を一切排除しました。
取得した3Dデータから形状公差・姿勢公差・位置公差の合計11種類の幾何公差測定ができます。従来では一点一点時間がかかっていた平面度測定も一瞬で視覚的に捉えることが可能。全体形状と部分形状を高精度に解析することができるため、迅速で正確な問題解決が可能です。
簡単設定に加えて、簡単な操作を実現しているため、測定に不慣れな人でも正確な測定が可能です。そのため、研究開発や条件出しのテスト時だけでなく、製品の測定・解析におけるN増しも簡単に実現します。


![[形状公差]: 平面度、円筒度、真直度、真円度 [姿勢公差]: 平行度、直角度、傾斜度 [位置公差]: 位置度、同心度、同軸度、対称度](/Images/ss_measurement-solutions_casting_017_1991810.png)
メリット3:3D-CADデータとの差分をカラーで見える化
設計した3D-CADデータと取得したデータを照合することができ、ワークの設計に対する現物の仕上がりを見える化できます。従来では測定が困難だったワークも、3D-CADデータと取得したデータを比較することで、今までわからなかった不具合が明確になるため、開発・設計担当がその場でフィードバックをかけることが可能。鋳造不良箇所の調査や原因追及などの解析に要する時間を飛躍的に短縮できます。
また、さまざまな寸法計測に対応でき、気になった箇所の寸法を精密に計測することで、問題点を詳細に分析することができます。
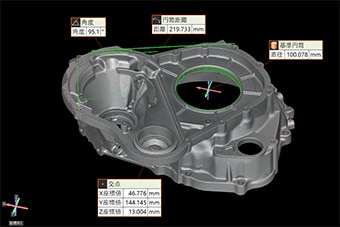
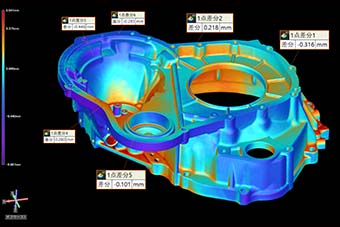
まとめ:鋳造品の測定を飛躍的に改善・効率化
「VLシリーズ」なら、高速3Dスキャンにより非接触で鋳造品の正確な3D形状を瞬時に測定可能です。
- 面で捉えるため、対象物全体において欠陥のある箇所の把握、そして任意の箇所のプロファイル測定が可能です。
- 複雑形状の対象物であっても、非接触で高精度な形状測定が可能です。
- 位置決め不要。対象物をステージに置いてワンクリックするだけの簡単操作で測定が完了します。
- 3D形状をカラーマップで表現可能。視覚的にわかりやすいデータを共有できるため、鋳造欠陥への対策がスムーズ。
- 複数の測定データの定量的な比較・分析が簡単に実現します。
- 複数の測定データに平面度の公差などの一括設定が可能。
- OK/NG品の判別が可能。データを共有し、NG品の解析を素早く実施することができます。
このように、「VLシリーズ」は、測定作業から不良解析、不良対策まで、業務の飛躍的な効率化を実現します。