C面の形状を正確かつ定量的に測定する方法
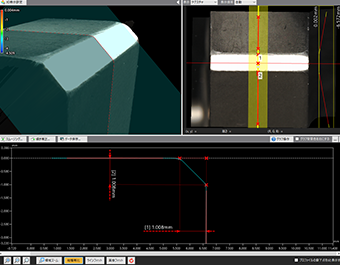
近年では金属のみならず、軽量で強度の高いCFRP(炭素繊維強化樹脂)や強化ガラスなどを材料とした部品・製品の角(エッジ)を面取り加工し、C面に仕上げる場合が多くあります。歯車など接触部分を持つ機械部品のエッジ摩耗防止はもちろん、腕時計や筆記用具、スマートフォンやタブレット、ウェアラブル端末など人が触れる製品にも施される場合があります。
高精度な面取り加工が求められる部品においては、正しく加工できているかを確認するために高い精度での定量的な測定が必要となります。このページでは、C面の図面表記などの基礎知識から、高精度な加工の実現に欠かせない測定の課題と解決方法を紹介します。
C面とは
強度の高い材料をせん断加工や打ち抜き加工した場合、端部がとても鋭利になるため、面取り加工(エッジ処理)を行います。面取り加工にはいくつか種類があり、面取り部分の形状に違いがあります。角を斜めに切削することを「C面取り」と呼びます。他にも、角を丸く加工する「R面取り」、微細に調整した加工を「糸面取り」などがあります。
C面の図面記載
C面は、よく図面上で「C5」や「C10」というように「C」と「数字」で表されます。「C」は、chamfering(面取り)を意味しており、一般に45度のC面を意味します。その横に付く数字は、切り取る辺の寸法(長さ:mm)です。つまり、辺の寸法(長さ)で交わる直角二等辺三角形で切り取った「45度のC面」を意味しています。たとえば、「C3」の場合の図面表記と加工内容を示します。
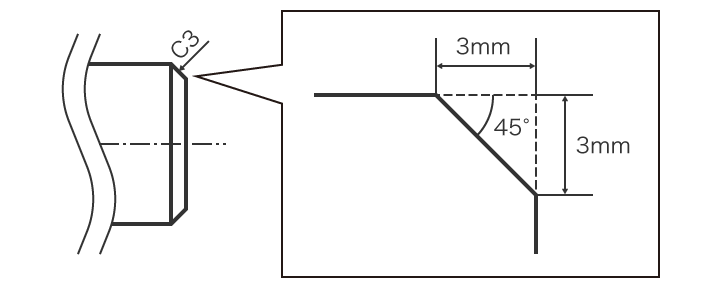
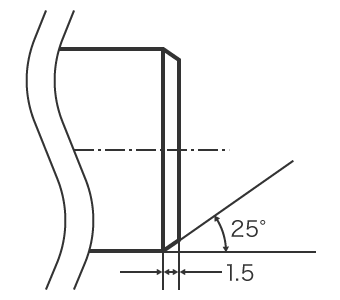
一般に、C面の角度が45度でない場合は、角度と寸法で表記します。たとえば、C面の角度が25度で、面取りする部分の辺の長さが1.5mmの場合は、下記のように示します。
C面加工深さの計算方法
たとえば、端部に対して45度の角度から工具または加工対象物を当て、切削してC面を取る場合、端部からの深さを計算することで、どの程度深く削ればいいかがわかります。
削りたい深さを「D」とします。「C1」の場合、下記の計算式で削る深さを求めることができます。
- D=1.0÷√2≒0.7(mm)
- 求めたい深さDは、1mm×1mmの辺で挟まれた直角二等辺三角形を半分にした長辺1.0の直角二等辺三角形の短辺に相当します。
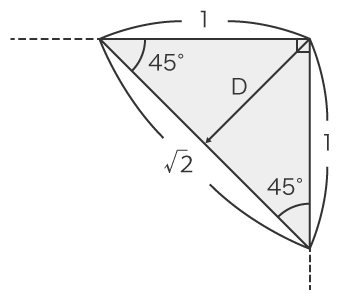
直角二等辺三角形の辺の比率は、1:1:√2です。
簡素化すると下記となります。
- D≒0.7(mm)
- これを覚えておけば、たとえば、「C4」のときは、D×4≒2.8というように、45度方向からエッジを削る深さを簡単に求めることができます。
C面の測定における従来の測定機での課題
C面の加工によって狙い通りの寸法(公差内)・形状が得られているかどうかの確認は非常に重要です。C面は立体的な形状であるため、高精度かつ定量的な3D形状の測定が求められます。
しかし、従来の三次元測定機や輪郭形状測定機、ノギス、測定ゲージなどを用いて測定する場合、正確な測定を実現するには難易度が高いなど、さまざまな課題がありました。
三次元測定機でのC面測定の課題
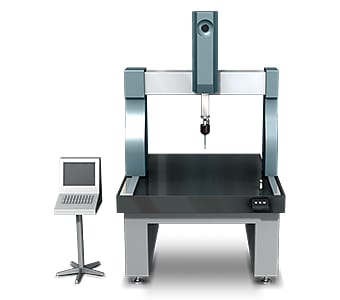
一般的に、三次元測定機では、対象物の3~6点に接触子を当てて、仮想面を作成してC面を測定しますが、下記のような課題があります。
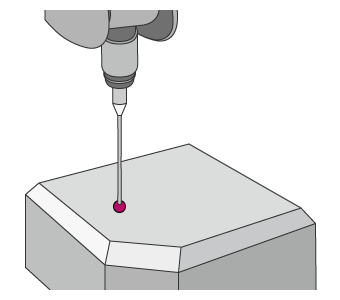
- たとえば、C面部分の面積が1mm2と小さい場合、その箇所をプローブで狙って仮想面を作成し、正確に測定することは困難を極めます。
- 小さな部分の3次元形状を測定する場合、三次元測定機にCAD図面を読み込ませるなどの工夫が必要となります。ある程度の習熟を要する測定機であるため、CAD図面を利用するにはさらに複雑で難易度が高い操作が求められます。
このように、現場の誰もが正確に測定できるわけではないということが大きな課題でした。また、仮想面の交点からC面を測定するため、実形状を反映することはできません。
輪郭形状測定機でのC面測定の課題
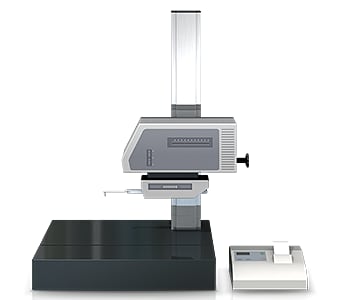
輪郭形状測定機では、測定したいC面の形状に対して、垂直方向に正確な測定ラインを取る必要があります。そこで、下記のような課題がありました。
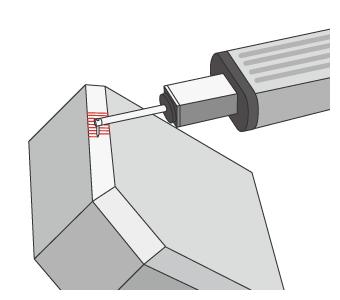
- サンプルを治具に固定したり、水平出ししたりなどの作業に時間がかかってしまいます。
- 正確に水平出しするためには、輪郭形状測定機に関する知識やスキルが必須です。
- 狙った通りに針を通す作業は非常に困難で、微妙な針のズレが測定値のバラつきの原因となります。
C面ノギスやゲージでのC面測定の課題
C面ノギスや、C面測定ゲージなどハンドツールは、非常に手軽な測定が可能です。しかし、測定誤差の発生や測定値がバラつく要因が複数あります。
たとえば、ノギスやゲージは、手で測定箇所に押し当てる力(測定力)や測る箇所のバラつきなど、人によって測定する際のさじ加減が異なります。その結果、測定値にバラつきが発生し、定量的な測定が困難となります。
C面の測定における課題解決方法
従来から使用されている一般的な測定機での課題を見直すと、ある共通点がわかります。それは、立体的な対象物・測定箇所に対して、点や線で接触しながら測定しているということです。
こうした測定の課題を解決すべく、キーエンスでは、ワンショット3D形状測定機「VRシリーズ」を開発しました。対象物の3D形状を非接触で、かつ面で正確に捉えることができます。ステージ上の対象物を最速1秒で3Dスキャンして3次元形状を高精度に測定することができます。そのため、測定結果のバラつくことなく、瞬時に定量的な測定を実施することが可能です。具体的なメリットを下記に挙げます。
メリット1:バラつきが生じない
スキャンした3D形状のデータに対して、パソコンの画面上で多彩な補助ツールを使って、任意の位置に正しく垂直なプロファイル線を引くことができるため、測定結果にバラつきが生じません。
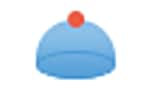
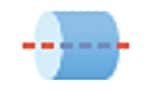
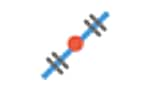
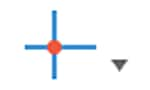
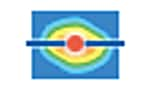
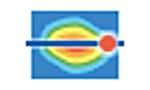
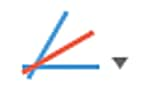
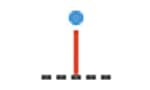
豊富な補助ツールで正確な測定が簡単に
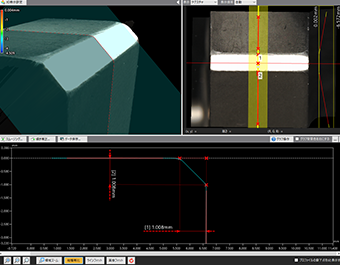
一度対象物をスキャンすれば、過去の測定時とは異なる箇所のプロファイル(断面形状)を測定することも可能です。わざわざ同一の個体を再び用意して再測定する必要はありません。また、過去のデータを活用して、ロットや加工条件、材料などが異なる同一形状のワークとの差分チェックも簡単に実現します。
メリット2:位置を気にせず、ステージに置くだけ
測定に必要な作業は、対象物をステージに置いて、ボタンを押すだけ。厳密な位置決めなどの事前準備が不要なので、測定機の知識や経験がなくても、すぐに高精度な測定が可能です。
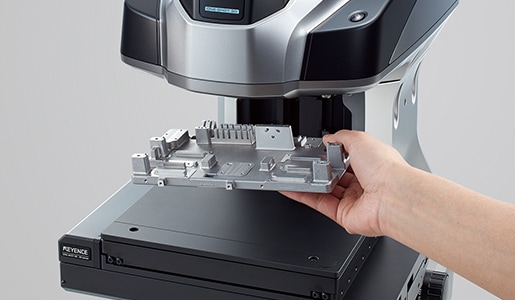
従来の測定機と異なり、ステージに置いた対象物の特徴を抽出し、自動的に位置補正することができます。これまで多くの手間と時間を要した厳密な位置調整は不要です。そのため、測定作業が属人化することなく、不慣れな方でも簡単・瞬時に測定することができます。
メリット3:高速かつ高精度に測定
ワンショット最速1秒で測定が完了します。従来の測定機では測定に時間を要するため困難だった、N数の大幅増加を実現します。
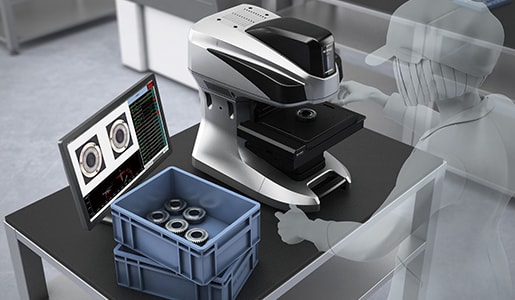
対象物を素早く簡単に測ることができるため、高精度な3D形状測定を開発やトライはもちろん抜き取り検査や、小ロット・高付加価値な製品であれば全数検査に活用するとこも可能です。不良品流出の抑制に加え、簡単な操作でレポート化も可能なため、ムダな工数をかけることなく、信頼獲得に貢献します。
まとめ:3Dスキャンなら、C面測定の飛躍的な改善・効率化が実現
高速3Dスキャンにより、非接触で対象物の正確な3D形状を瞬時に測定できる「VRシリーズ」であれば、従来の測定機における課題をクリアすることできます。
- 人による測定値のバラつきを解消し、定量的な測定が実現します。
- 位置決めなどなしに、ステージに対象物を置いてボタンを押すだけの簡単操作を実現。測定作業の属人化を解消します。
- 簡単・高速・高精度に3D形状を測定できるため、短時間で多くの対象物を測定することができ、品質向上に役立てることができます。
他にも、過去の3D形状データやCADデータとの比較、公差範囲内での分布などを簡単に分析できるため、製品開発や製造の傾向分析、抜き取り検査などさまざまな用途で活用することができます。