パイプ曲げ加工の計算方法
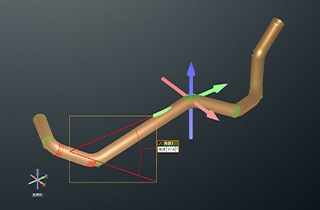
パイプとは、中空で断面が円形や角型になった金属や樹脂などの管全般を指します。また、パイプのほかに鋼管や配管、チューブなど、さまざまな呼び名もあります。
その形状や性質から液体やガスなどの搬送用、そのほか身近なところでは手すりや家具のフレームなど、さまざまな用途で使用されています。さらに用途にあわせて形状を加工することも多く、とくに『曲げ加工』はパイプを扱う上で必須の機械加工です。しかし、曲げ加工を施したパイプは、その形状の測定が難しく、測定に手間や時間がかかるという課題がありました。
今回は、そんな曲げ加工を施したパイプの寸法測定について解説。パイプの曲げ加工の基礎知識から加工方法、その測定方法と課題、課題の解決策をまとめています。さらにキーエンスの3Dスキャナ型 三次元測定機『VL-700シリーズ』は、パイプの曲げ寸法のように従来の方法では測定が難しかった形状にも対応。短時間で測定が可能ですので、その方法についても紹介します。
- パイプ・鋼管・配管とは?
- 金属管の種類
- パイプの曲げ加工とは
- 曲げ加工の種類
- 曲げRと曲げ角とは?
- パイプの曲げ加工における注意点
- パイプの曲げ加工に必要な展開寸法計算
- 従来のパイプ曲げ寸法測定の課題
- パイプ曲げ寸法測定における課題解決方法
- 短時間で正確にパイプ曲げ寸法の測定を実現
パイプ・鋼管・配管とは?
パイプとは、中空の管全般を指します。その中でも鋼材の管を『鋼管(こうかん)』と言います。ちなみに鋼材とは、鋼鉄を工業材料として製造したもので、炭素量0.02~2.1%の金属です。また配管は、液体や気体などの伝達に必要な管(パイプやホース)・継ぎ手・バルブ・計器・保護材などで構成された構造体を指します。
金属管の種類
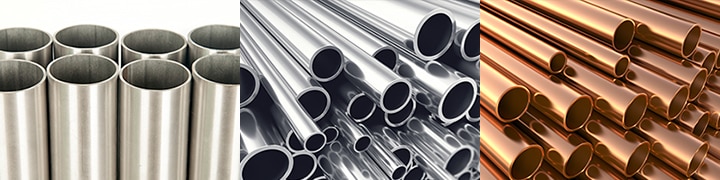
金属製の配管は、一般的に使用する材質によって以下のように分類されます。さらに鋼管は、用途によって配管用や建設用、土木用、機械用など、さまざまな種類にわけられます。
- ステンレス鋼管
- 10.5%以上のクロムが含まれた合金鋼で作られたパイプを『ステンレス鋼管』と呼びます。耐久性が高く、軽量化が可能で、低コストかつサビに強いことから使用頻度の高い鋼管です。
- 炭素鋼鋼管
- 鉄と炭素の合金である炭素鋼を主材料としたパイプを『炭素鋼鋼管』と呼びます。最も一般的な鋼管のため、単純に『鋼管』と呼ばれることもあります。また、炭素の含有量によって低炭素鋼や中炭素鋼、高炭素鋼のように分類されます。
- 合金鋼鋼管
- 炭素鋼にクロムやニッケル、モリブデンなどを添加した合金鋼を使用したパイプを『合金鋼鋼管』と呼びます。熱交換用の配管システム、また加熱炉などに用いられます。
- アルミ管
- 軽く、錆びにくいアルミを使用したパイプを『アルミ管』と呼びます。純度99%以上のアルミは強度が低いため、ジュラルミンなどを添加して強度を高めて使用します。主に熱交換器や船舶などの配管に使用されています。
- 銅管
- 水や土に対する耐腐食性に優れた銅を使用したパイプを『銅管』と呼びます。銅に亜鉛やスズ、金、銀などを添加することで、強度を高めることが可能。また、殺菌作用もあるので、エアコンの空気や冷媒などの配管、飲料水の給水管などに使用されています。
パイプの曲げ加工とは

曲げ加工とは、金属加工のひとつです。こちらでは、主に鋼管の曲げ加工の基礎知識として、『冷間曲げ』と『温間曲げ』について説明します。鋼材は、温度によって強度があがったり、脆くなったりするので、曲げ加工では温度管理が重要です。
- 冷間曲げ
- 常温から720°までの範囲で鋼材を曲げる加工方法を『冷間曲げ』と呼びます。ベンダー曲げやロール曲げなど、加工方法はさまざまですが、専用の機械を使用し、圧力をかけながらな目的の形状に曲げていきます。
- 温間曲げ
- 800°~900°の範囲で鋼材を曲げる加工方法を『温間曲げ』と呼びます。使用する鋼材にあわせて、 800°~900°の範囲で温度を上げて曲げ加工を行います。メリットは、冷間曲げよりも小さな圧力で加工でき、より大きく曲げたり、大きな歪みを与えたりすることが可能です。そのため、半径の小さな曲げを作りたい、鋭角に曲げたいといった場合に適しています。
- 炎加熱による曲げ
- 膨張や収縮による力を利用して鋼材を曲げる加工方法を『炎加熱による曲げ』と呼びます。具体的には、曲げたい箇所を局所的に加熱し、膨張させたあと、水などで冷却して収縮させることで対象箇所を曲げるので、大きな対象物でも高精度に曲げ加工ができます。炎加熱による曲げには、『線上加熱加工』などがあります。
曲げ加工の種類

金属製パイプを曲げる方法には、主にパイプベンダーを使用した『ドロー曲げ』と、3本のローラーを使用して曲げる『ロール曲げ(バリアブル曲げ)』などがあります。こちらでは、パイプの曲げ加工の方法について説明します。
- ドロー・ベンディング(回転引き曲げ方式)
- ドロー・ベンディング(回転引き曲げ方式)は、適応範囲の広いパイプ曲げの加工方法です。肉厚パイプや肉薄パイプ、さらにパイプ直径に対して1.0~1.5倍の曲げ半径になる極小R仕上げといった精密曲げも可能です。具体的な加工方法は、回転するベンディング・フォームにクランプ・ダイを使用してパイプを固定し、引き曲げていきます。
- コンプレッション・ベンディング(圧縮曲げ方式)
- コンプレッション・ベンディング(圧縮曲げ方式)は、マンドレルを使用せず、最小限の設備でパイプを曲げられる加工方法です。最小限の設備で曲げ加工ができるので安価かつ作業性に優れています。両端同時曲げや蛇行曲げに適した加工方法です。
- プレス・ベンディング(プレス曲げ方式)
- プレス・ベンディング(プレス曲げ方式)は、パイプをラムまたはシリンダなどによって押し曲げる加工方法です。比較的肉薄なパイプ、また曲げRの大きなものなど、使用用途は限定されますが大量生産に向いた曲げ加工方法です。曲げ品質よりも生産性を重視した加工方法と言えます。
- ロール・ベンディング(3本ロール曲げ方式)
- ロール・ベンディング(3本ロール曲げ方式)は、回転駆動する3本のローラーを組み合わせ、パイプをアーチ上に曲げる方式です。曲げ加工に必要な金型製作も容易で、円形曲げに適した加工方法です。ただし、ドロー・ベンディングのような精度が見込めず、2箇所以上の連続曲げにも適していません。また、ロール・ベンディングのほか、『バリアブル曲げ』とも呼ばれます。
- ストレッチ・ベンディング(引張曲げ方式)
- ストレッチ・ベンディング(引張曲げ方式)は、複合R形状の曲げに適した加工方式です。比較的大きなR曲げ、また不規則な曲げ加工に適応します。また、パイプのほか、ロール成形品やアルミサッシュ材などの曲げ加工でも多く用いられている方法です。
曲げRと曲げ角とは?

曲げRとは、板材や管材(パイプ)、棒材などをプレスやロールなどで曲げ加工したとき、曲げた位置から曲げの中心部までのR(半径)のことです。曲げRには、板厚や径によって、素材を割らずに曲げ加工が行える限界(最小曲げR)があり、適切な曲げRに設定する必要があります。
また、曲げRに似た言葉として、『曲げ角』があります。曲げ角は、L曲げやU曲げの際にパッドで押さえられているウエブ面からの角度を指します。この曲げRと曲げ角の違いを理解しておきましょう。
パイプの曲げ加工における注意点
パイプの曲げ加工において、パイプの厚みや径、長さ、そして素材にとって曲げ加工のしやすさが変わります。とくにパイプ経が太く、厚みのある場合には、指定の角度に曲げることが困難な場合もあります。
また、曲げRが小さい場合も加工が難しくなります。曲げRが小さいということは、鋭角に曲げる必要があり、亀裂などが生じやすくなります。そのため、パイプや鋼材ごとの最小曲げRを考慮する必要があります。
そのほかにも金属を曲げる場合、金型などから外したとき、もとの形状に戻ってしまう『スプリングバック』という現象についても考慮が必要です。そのため設計時には、事前にスプリングバックによる戻りを計算するなど、2段曲げやストライキングなどのスプリングバック対策が求められます。
パイプの曲げ加工に必要な展開寸法計算
パイプの曲げ加工を行う場合、安定して曲げることができるのか、シミュレーションを行う必要があります。その際に用いるのが展開寸法計算です。パイプの曲げ展開寸法は、曲げRからパイプの中立軸までの距離を求めれば、算出できます。

- a
- 曲げRから中立軸までの距離
- b
- 曲げR
- c
- 曲げ部中立軸
直線部分AおよびBについては、曲げによる変化がないので、そのままの数値を使用します。曲げ部分の中立軸移動率(λ:ラムダ)は、材料の板厚や硬度、曲げ角度、内曲げRによっても異なりますが、一般的にパイプの厚さの20~45%あたりの位置になるとされています。ただし、最小曲げRは鋼材の特性などによっても異なるため、設計する際には素材が破れない曲げRに指定する必要があり、設計の際には図面どおりに曲げ加工ができるのかを見極め、それにあわせて使用する鋼材を検討する必要もあります。
L=A+B+(R+T×λ)×2п×θ/360
- L
- 展開寸法
- A・B
- 曲げ応力のない部分の長さ
- R
- 曲げ内側R(半径)
- T
- 板厚
- θ
- 曲げ角度
- λ
- 中立軸移動率(%)※経験値を採用
従来のパイプ曲げ寸法測定の課題
パイプの曲げ加工では、ドロー曲げやロール曲げにかかわらず、完全に不良を防止することは困難です。割れや欠け(クラック)、スプリングバックによる形状不良などは、歩留まり率の低下や製品の品質不良・破損といったトラブルを招きます。
そのために設計時や試作時、加工の条件変更時、さらに量産時など、正確に形状測定・検査が求められます。一般的にパイプ曲げ寸法は、ノギスや投影機を使って測定しますが、それら従来の測定方式では時間がかかるといった課題がありました。
ノギスによる測定の課題
ノギスなどのハンドツールで測定する場合、はさめる範囲であれば厚みや寸法を測定できますが、パイプの曲がり部分などの物理的にノギスの入らない場所は測定が困難でした。また、曲げ加工を行ったパイプなど、曲線部分などがある場合の寸法測定では、架空点による測定も用いられますが、ノギスなどのハンドツールでは架空点測定に対応できません。

投影機による測定の課題
パイプ曲げ寸法を測定する場合、対象物を台に乗せ、下から光を当てることで輪郭をスクリーン上に投影する『投影機』もよく用いられます。投影機の場合、対象物をセットする際に水平出しをする必要があり、置き方によって寸法も変わるため、サンプルの固定に手間がかかり、形状によっては寸法測定ができないといった問題ありました。また、三次元形状に曲がりのあるパイプの場合、測定箇所ごとに設置方法を変更する必要があり、大型のサンプルでは物理的にステージに置けない場合もあります。さらに寸法や図面との相違箇所の数値が取得できず、輪郭形状をトレース紙に転写する必要があるなど、データの保存や比較が困難です。

パイプ曲げ寸法測定における課題解決方法
パイプ曲げ寸法を測定する従来の方法では、立体的な対象物・測定箇所に対して測定が困難で、測定者によって測定結果がバラつくという課題があります。測定だけではなく、数値の取得や図面との比較に時間がかかるという大きな課題がありました。
それらのパイプ曲げ寸法測定の課題を解決する手段がキーエンスの3Dスキャナ型 三次元測定機『VL-700シリーズ』です。『VL-700シリーズ』は、ステージ上に置いた対象物をワンショット最速8秒で360°スキャンを実現し、高精度に3次元形状を測定可能。パイプの曲げ寸法なども正確に測定可能。さらに測定者によるバラつきもなくし、曲げ加工を施したパイプの寸法を短時間で測定できます。ここでは、その具体的なメリットについて紹介します。
メリット1:置き方を気にせず、簡単に曲げ寸法を測定できる
キーエンスの3Dスキャナ型 三次元測定機『VL-700シリーズ』は、曲げパイプのような三次元形状も手軽に測定できます。取得したデータを見ながら、自由自在にXYZの座標系を作成可能で、座標系に基づいた測定を実現します。従来の投影機による測定では、測定箇所ごとにサンプルの設置位置を変更して測定を行う必要がありましたが、キーエンスの3Dスキャナ型 三次元測定機『VL-700シリーズ』ならそんな手間も不要。ワンショットで全体像をスキャンし、座標軸を変更しながら自由自在に測定できます。

メリット2:複雑な曲げパイプでも一度のスキャンで測定ができる。
キーエンスの3Dスキャナ型 三次元測定機『VL-700シリーズ』ならワンショット最速8秒で全体形状をスキャンするので、複雑な曲げパイプでも各部の寸法測定が簡単かつ素早く行えます。架空点による測定など、二次元に投影した差異のXY寸法の測定にも対応しています。また、CADデータとの比較なども簡単に行えるので、形状不良などの判定も容易で、寸法測定はもちろん、合否判定にも活用できます。

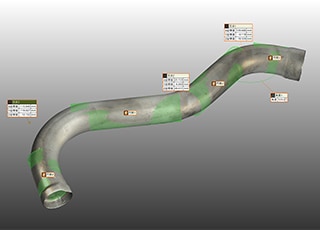
短時間で正確にパイプ曲げ寸法の測定を実現
キーエンスの3Dスキャナ型 三次元測定機『VL-700シリーズ』なら、従来のように何度もサンプルの置き方を変えたり、トレース紙に書き写したり、図面と比較したりといった手間がなく、パイプ曲げ寸法の測定を簡単かつ短時間で、さらに正確に実施できます。
- 立体物を三次元でスキャンするので、何度もサンプルの置き方を変える必要がありません。
- ワンショット最速8秒で360°スキャンが可能なので、測定にかかる時間を大幅に短縮できます。
- 複雑な形状でも自由自在にXYZの座標系を設定できるので、必要な場所の寸法を測定できます。
- 各部寸法の数値も簡単に取得でき、3D CADデータとの比較も簡単に実施できます。
- 寸法だけではなく、形状変化なども同時に検査できます。
従来の測定方法では、時間も手間もかかっていたパイプ曲げ寸法の測定。それがキーエンスの3Dスキャナ型 三次元測定機『VL-700シリーズ』なら、ワンショット最短8秒のスキャンで完了します。さらに必要な寸法を簡単に参照できるので、短時間でも寸法測定が実現し、作業の大幅な効率化につながります。