研磨量を簡単・正確に測定する方法

「研磨」とは「とぎ、みがくこと」また、「深く研究したり、心身を鍛えること」といった意味でも使われる良い言葉です。工業界でもさまざまな分野で使われ、代表的なものとして、半導体工程のラッピングが挙げられます。「研磨」という技術の歴史は古く、その起源は縄文時代まで遡るという説もあります。
ここでは、対象の表面を磨き、なめらかにする「研磨」と研磨によって発生したひずみや損傷を除去する「エッチング技術」の基礎知識と特長、そしてそれらの評価に使用されている「3D形状測定機」の活用事例をご紹介します。
- ラップ研磨
- バフ研磨
- 電解研磨
- 化学研磨
- 樹脂の磨耗量解析事例
- 研磨パッドの形状測定事例
- 砥石の形状測定事例
- さまざまな種類のエッチング
- 金属組織の観察、エッチングによる組成分析事例
- エッチング量の評価事例
- 化学研磨処理後の表面粗さ測定事例
ラップ研磨
ラップと呼ばれる平面定盤に対象物を置き、対象物と定盤の間に砥粒としてラップ剤(ダイヤモンド・炭化ケイ素・アルミナなど)を流し、テーブルを回転させて対象物表面を削る研磨方法のことです。

- A
- 側面図
- B
- スラリー
- C
- スラリーフィーダー
- D
- ウェハ
- E
- キャリアフィルム
- F
- 研磨パッド
- G
- 研磨回転テーブル
バフ研磨
布製またはその他の材料で作られた研磨輪(バフ)に研磨剤を染み込ませたり表面に塗布し、回転させ、対象物を押し付けることで表面の面粗度を向上させる研磨方法のことです。

電解研磨
電解研磨液と呼ばれる酸性の液体に対象物を浸漬し、対象物を陽極として電流を流します。対極の表面から微量の鉄やニッケル原子が溶け出し、対象物がエッチングされます。陰極の設置によって狙ったところが削れ、結果として少ないエッチング量で細かい粗度に仕上げることができます。

- A
- 電源
- B
- 電解液
- C
- 対極(カソード)
- D
- 製品(アノード)

- (1)研磨前(製品表面)
- 数μm程度の凹凸
- (2)研磨時(製品表面)
- 凸部が優先的に溶出
- (3)研磨後(製品表面)
- 平滑化
電解による凸部の優先的溶解で平滑化。
化学研磨
化学研磨液と呼ばれる酸性液体に対象物を投入し、対象物表面を溶かします、液が触れている部分は、対象物の表でも裏でも均一にエッチングされ、電解研磨のような選択性はありません。
電解研磨 | 化学研磨 | |
---|---|---|
研磨量 |
概ね1〜5μ |
概ね1〜20μ |
到達精度 |
サブミクロン |
ミクロン |
電極 |
必要 |
不要 |
樹脂の磨耗量解析事例
評価前と評価後の表面性状や磨耗の仕方、量などの傾向を解析することで、材料配合や化学合成の条件を細かく分類、数値化し、無駄な製造コストを改善できました。
従来方法
触針式表面粗さ計で評価
- 樹脂の場合、触針の測定圧による傷が生じる。
- 測定ポイントのバラつきをなくすため、N数をこなす必要があり、解析工数がかかる。
導入効果
- 複数の評価データを、一括で同じ評価条件での解析ができる。
- 面で評価できるため、粗さ、体積、表面積などの多角的な解析ができる。



研磨パッドの形状測定事例
研磨パッドの表面状態が研磨対象の平坦度や均一性などの、仕上がりに影響するため重要になります。
表面状態を定量評価することで、品質が改善できました。
従来方法
SEMで評価
- 観察できる範囲が狭いのでN数をこなす必要がある。
- サンプルの加工、蒸着など前処理が必要なため、解析に時間がかかる。
導入効果
- 測定範囲が広く、一回で評価できる。
- 測定時間が短い。
- 表面の形状、凹凸を定量化できる。
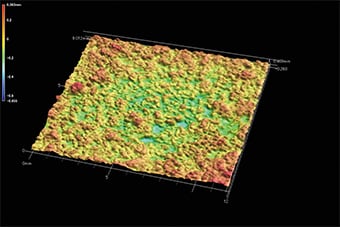

砥石の形状測定事例
台金にダイヤモンド・CBN砥粒をメッキで固定するため、台金の形状が重要になります。
電着砥石の台金の表面形状を評価することで、歩留まりが改善できました。
従来方法
SEMで評価
- 観察できる範囲が狭いのでN数をこなす必要がある。
- 解析に時間がかかる。
- 試料サイズが限定されるため、解析のための加工が必要で破壊検査となる。
導入効果
- 試料サイズの制限がないので、非破壊で評価できる。
- 表面の形状、凹凸を定量化できる。


さまざまな種類のエッチング
エッチングは、酸、アルカリなどの化学溶液を用いるウェットエッチングとイオン、ガス、ラジカルなどを用いるドライエッチングに大別されます。

ウェットエッチング
- 等方性エッチング
-
マスク開口部において、表面の放線方向と同じ速度でエッチングされるためマスクの直下がえぐられます(サイドエッチング、アンダーカット)。犠牲層を取り去るときにはこの方法が使われます。
- A
- マスク
- 異方性エッチング
-
サイドエッチングを抑え、結晶異方性を利用してある特定の方向にだけエッチングを行う方法です。
- A
- マスク
ドライエッチング
- 化学エッチング(等方向性エッチング)
-
イオン化・ラジカル化した反応ガスとエッチング対象との化学反応によるエッチング方法です。
- A
- イオンプラズマ
- B
- レジスト
- C
- Sio2などの酸化膜(絶縁材料)
- D
- シリコンウェハ
- E
- レジストのない部分がイオンによって削られる
- 方向性エッチング
-
エッチング対象に対して指向性をもつイオンや高速中性粒子を衝突させてエッチングする方法です。
金属組織の観察、エッチングによる組成分析事例
SEMでしか観られない金属組成が観え、エッチングにより腐食した部位の高さを測定することで、組織の成分も評価できます。
従来方法
SEMで評価
- 金属顕微鏡かSEMで、金属組織を目視で観察するだけだった。
- 目視による判断ではN数の評価が必要である上、測定ポイントや人によるバラつきも大きく、解析に時間がかかっていた。
導入効果
- 画質が良く、SEMでしか見えなかった金属組成が見える。
- 表面の形状、粗さを定量化し、解析に余計な工数を取る必要がない。
- エッチングにより陥没した部位を高さ測定することで、組織の成分が判断できる。


エッチング量の評価事例
時間経過や温度変化に伴う、エッチング効果を表面形状や表面粗さで定量化できます。
エッチングの条件出しなどの評価工数を削減できました。
従来方法
金属顕微鏡、触針式表面粗さ計で評価
- 拡大観察では、再現性が乏しく、信頼性が低い。
- 触針の先端Rより小さな溝は測定できない。
導入効果
- 表面形状の違いを、定量化できる。
- 触針の先端形状や磨耗の影響を受けずに、表面粗さを評価できる。
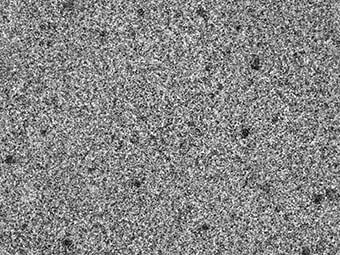

- エッチング時間
-
0分 -
5分 -
10分
化学研磨処理後の表面粗さ測定事例
化学研磨処理後の表面粗さを評価することで、化学研磨による母材への影響の評価が可能になり、歩留まりを改善できました。
従来方法
SEMで評価
- 金属顕微鏡で、金属表面を目視で観察。
- 触針式表面粗さ計での表面粗さ評価では、測定ポイントによって数値がバラつくためN数の評価が必要であり、解析に時間がかかっていた。
導入効果
- 表面の形状、粗さを定量化できる。
- 面で評価できるため、再現性の高い評価ができる。



