変形した基板の正確な3D形状を瞬時に測定・分析する方法
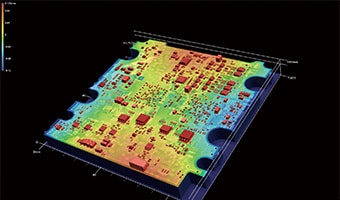
基板は、電子部品・デバイス実装時のリフロー工程において、クリームはんだ(はんだペースト)やボンドでの接合、加熱によるストレスを受けます。リフロー工程は、効率的な部品実装を実現しますが、加熱によるストレスは、基板の反りやうねり、ひずみといった熱変形を招く場合があります。基板が変形すると、部品の接合強度や、筐体との嵌合性が低下するなど、歩留まり率に大きく影響してします。
ここでは、基板の変形に関する基礎知識から、変形を測定する際の課題、そして最新の測定方法までを解説します。
- 基板の「変形」とは
- 基板の変形のシミュレーション解析と評価
- 従来の測定機器での基板の変形測定・評価の課題
- 基板の変形の測定における課題解決方法
- まとめ:正確な測定が難しい、基板全体の変形の測定を飛躍的に改善・効率化
基板の「変形」とは
基板(プリント配線板)の表面は、部品を正しく実装するために平面であるべきですが、熱による過剰なストレスによって、反ったりうねったり熱変形を起こすことがあります。基板の変形が問題として顕在化した背景や、その影響を以下に挙げます。
基板の熱変形の背景
電子部品実装基板の多層化および小型化、そして実装の高密度化が進み、リフロー方式を用いた部品実装を採用するようになりました。リフロー工程は、基板にはんだペースト(クリームはんだ)を必要な箇所に印刷し、部品固定用のボンドを塗布して、マウンターで電子部品を基板に配置。それを炉に入れて熱ではんだ付けやボンドを硬化させることで、効率的な部品実装が可能です。
リフロー工程では、環境に配慮した鉛フリーはんだの導入を背景に、従来よりもはんだの溶融に高い温度が求められるようになりました。リフロー炉内の温度を上げると、基板への熱によるストレスが増加します。基板が高温の炉内で反ったり、うねったりと熱変形するトラブルが増加しました。
基板の変形による影響
基板が変形すると、位置ズレなどによって正しくはんだ付けできていなかったり、はんだ付け部分に応力が加わって接続不良が発生したり、大きく変形した場合には、筐体との組み付けの嵌め合いの精度が低下してしまうなどのトラブルに繋がります。こうした不具合は、歩留まり率を大きく低下させる場合があります。
また、基板の部分的あるいは全体の微妙な変形に気づかず、筐体に組み付けて出荷した場合、後に電子部品の接続不良による製品の故障が発生し、クレームに繋がる可能性があります。特に自動車や航空機などの制御基板においては、故障が事故に繋がる可能性があるため、基板の形状は、リード浮きやはんだフィレットの形状と同様に重要なチェック項目であるといえます。
基板の変形のシミュレーション解析と評価
基板の変形を抑えるための改善には、設計や実際に加熱しての評価など、さまざまな段階で加熱条件を検討・検証・評価する必要があります。
ソフトウェアを使った変形のシミュレーション解析
基板の設計段階では、CADのデータを使ったシミュレーション解析を用いることがあります。物体が変形する挙動をシミュレートし、評価するために用いられる手法の1つとして、「有限要素法(FEM:Finite Method Element )」があります。
有限要素法とは
有限要素法(FEM)とは、複雑な形状であっても単純な形状の集合体(要素)になるまで分割(離散化)し、まずその単純形状のごとの応力や変形を求めるシミュレーション解析法です。各単純構造を積み重ねて元の全体構造まで積み重ねることで、全体における各部の応力や変形を想定します。これをコンピュータのソフトウェア上で対象となる製品のCADデータを用いて行うことで、剛性・強度・耐振動性・塑性変形・破壊・熱変形などのシミュ―レーション解析を行うことができます。
要素は形状によって以下の分類・種類があります。
0次元要素 (スカラー) |
![]() |
||
---|---|---|---|
1次元要素 (バー) |
![]() |
||
2次元要素 (シェル) |
![]() |
![]() |
|
3次元要素 (ソリッド) |
![]() |
![]() |
![]() |
- 0次元要素(スカラー):形状を持たない点。
- 1次元要素(バー):線状:棒や柱、梁などを線とするときなどに用いられます。
- 2次元要素(シェル):面。薄い板材などに用いられます。
- 3次元要素(ソリッド):表の左から順に、三角錐のテトラ要素・三角柱のペンタ要素・直方体のヘキサ要素と呼ばれ、この3種類が用いられます。ヘキサ要素を多く用いることで、厚みのある物体の解析精度を高めることができますが、難易度が高く、多くの計算時間が必要です。一方で、テトラ要素を用いて自動的に3次元要素のメッシュを作成する技術が進んでおり、計算時間も短いため、精度の高さよりも時間短縮を優先する場合には最適です。
シミュレーション解析の主な特徴と流れ
低次元であるほど形状を省略しているため、解析処理にかかる時間が短く、次元が増えるほど多くの時間を要しますが、より精度の高いデータを得ることができます。3次元要素基板の変形シミュレーションの一般的な流れとしては、まず基板の設計データをメッシュ状の要素に分割します。基板の設計データは2Dであることがほとんどですが、ソフトウェアによっては3D CADのフォーマットに変換する必要があります。メッシュ化した各要素に仮想でリフロー工程での温度プロファイルの加熱温度の通り温度上昇させた場合の応力を与え、想定データを取得します。
基板の加熱試験と実測・評価における要求
シミュレーションを経た基板を実際にリフロー炉に入れ、仮定した温度プロファイルでシミュレーション通りになるか検証し、評価する必要があります。
サイズにもよりますが、基板を有限要素法で3次元要素に分割すると、要素の数は約5万点におよぶ場合があるといわれます。つまり、基板全面の形状をもれなく高精度に測定できなければ、どれだけ緻密にシミュレーション解析しても、正しい検証結果を得ることができません。設計段階で改善すべきポイントを見逃さないためには、実測はとても重要なプロセスとなります。
次に従来の測定機器を用いた測定の課題や、コンピュータを使った高精度なシミュレーションとの比較・評価に対応できる、最新の測定方法について解説します。
従来の測定機器での基板の変形測定・評価の課題
従来の輪郭形状測定機や三次元測定機などの計測機では、基板全体の形状を正確に測定することは難しいため、高度なシミュレーションと試験・実測を行っても、サンプルの形状とその変化を定量的に数値化し、評価することが困難でした。従来の測定機を使った測定では、下記のような課題がありました。
輪郭形状測定機での変形の測定・評価課題
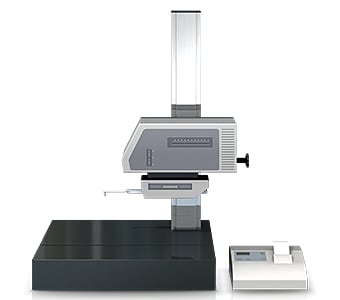
輪郭形状測定機とは、スタイラスと呼ばれる触針を用いて対象物の表面をなぞることで、その輪郭形状を測定、記録する装置です。
近年では触針の代わりにレーザーを用いて、非接触で輪郭をなぞることで複雑な形状の測定に対応した機種もあります。また、機種によっては上下両面の測定が可能なものもあります。
輪郭形状測定機を用いた基板変形の測定・評価では、下記のような課題がありました。
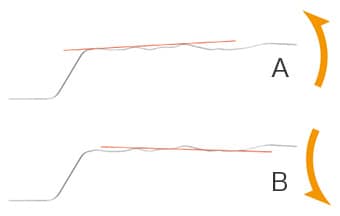
- A
- 右上がり
- B
- 右下がり
- 対象物を線でなぞって測定するため、広範囲の変形を測定・評価することは困難です。
- 対象物の表面全体の形状は把握できません。
- 表面実装後の基板のように、本来測定したい面以外に凹凸(実装部品)があると、基板自体が変形しているかどうかを測定することが困難です。
- 線での基準面設定は困難なため、測定誤差が発生することがあります(図)。
三次元測定機での変形の測定・評価課題
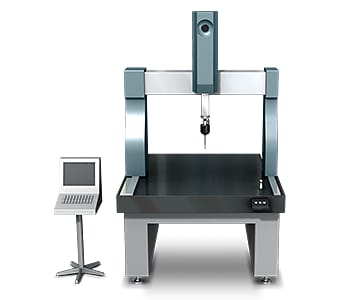
一般に、三次元測定機で基板の変形を測定するには、対象物の測定したい面の隅4か所以上にプローブ先端の接触子を当てる必要があります。
たとえば、プレート部材の場合、6~8点を測定することが一般的です。測定範囲が広い場合、測定ポイントを増やすことで、より多くの箇所の測定値を取得し、測定精度を向上させることができます。
基板の変形の測定・評価においては、下記のような課題がありました。
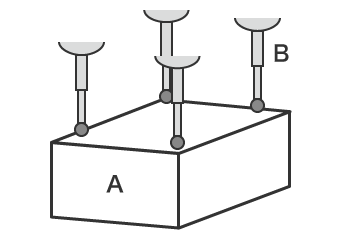
- A
- 対象物
- B
- プローブ
- 限られた点で接触して測定をする必要があるため、全体の形状を取得することができません。
- より多くの測定値を得るために多点測定するには、多くの時間を要してしまううえ、全体の形状と凹凸ができた箇所など、詳細な形状を把握することはできません。
基板の変形の測定における課題解決方法
従来の測定機は、線や点で測定するため、変形した基板全体の形状が把握できませんでした。また、対象物全体におけるすべての凹凸の最大値・最小値を得たり、すぐ定量的に比較することは困難です。
こうした測定の課題を解決すべく、キーエンスでは、ワンショット3D形状測定機「VRシリーズ」を開発しました。
対象物の3D形状を非接触で、かつ「面」で正確に捉えることができます。また、ステージ上の対象物を最速1秒で3Dスキャンして3次元形状を高精度に測定することができます。このため、測定結果がバラつくことなく、瞬時に定量的な測定を実施することが可能です。ここでは、その具体的なメリットを紹介します。
メリット1:最速1秒。「面」で対象物全体の3D形状を一括取得。
「VRシリーズ」は最速1秒で実装基板に対して、非接触・ワンショットで80万点の「面」データを取得することができます。取得した3D形状の最大・最小の凹凸(高さ・深さ)をカラーマップで表現できるため、対象物全体から変形した箇所を「見える化」することができます。
また、スキャンしたデータに対して、直感的な操作で任意の箇所に円周状・直線・平行線・垂線など多彩なプロファイル線を引くことができます。正確なプロファイル測定が可能なため、変形した箇所の詳細なデータも素早く取得することができます。測定後であっても対象物を再びセットすることなく、過去に3Dスキャンした広範囲のデータから別の箇所をプロファイル測定することもできます。
さらに、設計データまたは加熱前の基板のスキャンデータとの形状比較や、異なる加熱条件を与えた複数の基板の測定データの形状比較、そして複数のデータに測定項目を一括適用することも可能です。
これにより、正確な測定・比較・評価はもちろん、飛躍的な工数削減、業務効率の向上が実現します。
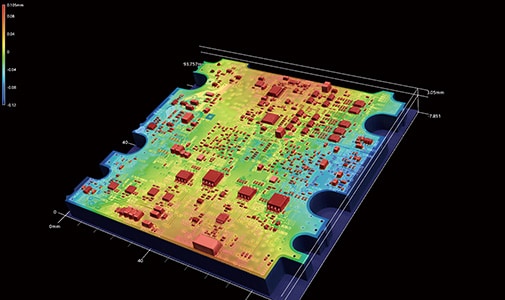
メリット2:簡単操作で、誰が測っても測定値がバラつかない
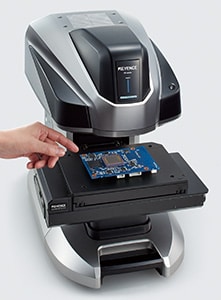
対象物をステージの上に置き、ボタンを押すだけの簡単操作で、3D形状の測定を実現しました。
低倍率/高倍率カメラを切り換えることにより、小さな基板であっても、基板の全体や細部も1台で正確に測定することができます。
また、対象物の特徴データから自動的に位置補正が可能なため、シビアな水平出しや位置決めは不要です。対象物の大きさを判断して測定範囲を自動設定・ステージ移動する「Smart Measurement機能」を業界で初めて搭載し、測定長やZ範囲などを設定する手間を一切排除しました。
さらに、豊富な補助ツールを使用することで、目的の測定内容を直感的に設定することができます。
簡単設定に加えて、初心者でも簡単な操作を実現しているため、測定に不慣れな人でも最速1秒で正確な測定が可能です。そのため、設計やシミュレーションの実証実験・評価はもちろん、量産時の測定・検査におけるN増しや傾向分析も簡単に実現します。
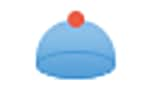
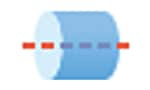
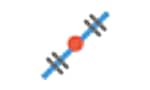
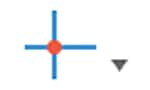
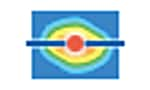
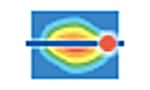
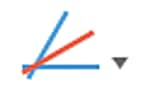
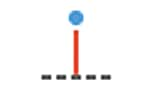
まとめ:正確な測定が難しい、基板全体の変形の測定を飛躍的に改善・効率化
「VRシリーズ」なら、高速3Dスキャンにより非接触で対象物の正確な3D形状を瞬時に測定可能です。基板全体の3次元寸法はもちろん、微細な高さ・凹凸形状の測定、複数データの比較など、これまで難しかった作業も短時間で実現します。
「VRシリーズ」を導入することで、これまでの測定における課題をすべてクリアすることができます。
- カラーマップで対象物全体における高さの違いを見える化することが可能です。
- 複数の測定データの比較や、条件の一括適用が簡単に実現するため、業務効率が飛躍的に向上します。
- 一度スキャンすれば、いつでも任意の場所のプロファイル測定や複数データの比較などが可能です。
- 位置決めなどなしに、ステージに対象物を置いてボタンを押すだけの簡単操作を実現。測定作業の属人化を解消します。
- 簡単・高速・高精度に3D形状を測定できるため、短時間で多くのN数に対応可能。品質向上に役立てることができます。
- 人による測定値のバラつきを解消し、定量的な測定が実現します。
他にも、CADデータとの比較や、公差範囲内での分布なども簡単に分析できるため、研究開発や設計、試験などの段階はもちろん、量産投入後の抜き取り検査、不良発生時の原因究明など、エレクトロニクス製品製造のさまざまなシーンで活用することができます。