ボルトやねじの首下をすばやく正確に測定する方法

ボルトやねじには多くの種類があり長さや太さ、形状によって分類され、目的に応じて使い分けられます。また、これらが規格で決められたものもあれば、ある目的のためだけに設計された、特殊なものもあります。どのボルトやねじにも共通していえることは、規格または設計で定められた公差内に高い精度で加工しなければならないということです。
ここでは、これらのなかでも最も高い精度が要求される首下といわれる部分について、基礎知識と役割、測定の課題、そしてその解決方法について説明します。
首下とは
表面積とは、立体の表面の面積のことであり、見える部分の面積です。表面積は質感・密着性・滑り性・放熱性など、粗さなどの指標と並んで、機能性評価における重要な指標の1つです。たとえば金属破断面や摩擦面、PGAやレーザーマーカによる刻印などは、表面積を測定することでさまざまな情報を得ることができます。
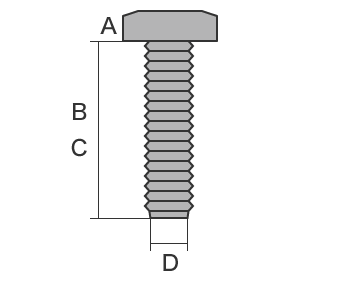
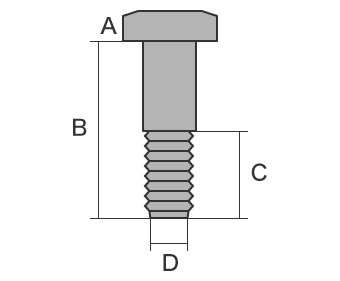
- A
- 頭部
- B
- 首下
- C
- ねじ長さ(首下長さ)
- D
- ねじ径
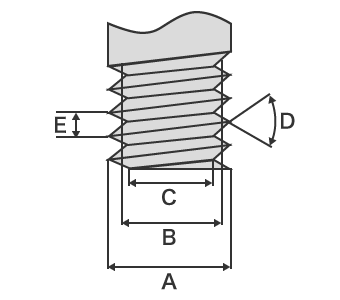
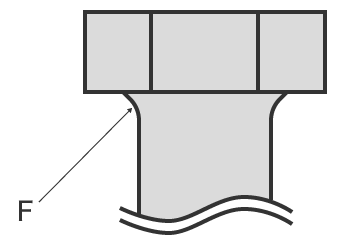
- A
- 外径
- B
- 有効径
- C
- 谷の径
- D
- ねじ山の角度
- E
- ピッチ
- F
- 首下R
ねじ山の構造
ねじ山はらせん状になっており、らせんは円筒に直角三角形を巻き付けた線になっています。この線を「つる巻線」といい、らせん状の山と谷は、摩擦力や強度・精度などの機能を実現するために、さまざまな構造を持っています。
また、ねじが1回転したときに、軸方向に進む距離を「リード」といい、一条ねじでは、リードとピッチは等しくなります。リードに対するねじ1回転分の長さが作る角度を「リード角」といいます。
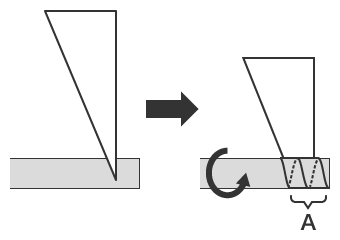
- A
- つる巻線
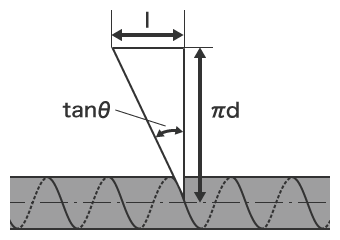
- tan θ
- リード角
- l
- リード(mm)
- π d
- ねじ1回転分の長さ(mm)
全ねじと半ねじの違い
ボルトやねじのねじ山には、最も重要な機能である締結力(ねじの締め付けによる固定力)と、部品同士を張り合わせる力があります。そして、ねじ山の種類には、首下のすべてにねじ山がある「全ねじ」と、途中までしかねじ山がない「半ねじ」があります。
全ねじは締結力が強いため、強力な固定力を発揮します。しかし、たとえば2枚の板の間にすき間がある場合、隙間をなくして貼り合わせることはできません。一方半ねじは、締結力を一方の板にのみ与えることができるため、重ね合わせた部品をすき間なく貼り合わせる場合に使用します。
なお、ねじ部の長さ範囲はJISで定められています。その長さは一般に径の2.5倍ですが、首下の長さやメーカーによって、範囲内で異なる場合があります。
例:2枚の板を固定する場合
全ねじでは頭部まで締まると、それ以上締め込んでも隙間は残る。
半ねじの場合、片方の板だけにねじの力が加わり引き寄せられるため、隙間がなくなる。
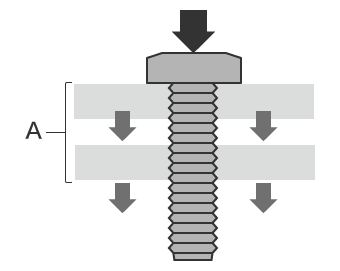
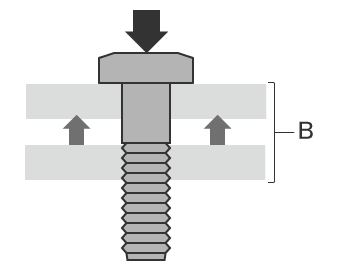
- 締結力
- 板にかかる力
首下Rの役割り
頭部と首下には、断面の変化が急激であるため、応力集中が発生して疲労破壊による「頭飛び」といわれる現象が生じる場合があります。これを避けるために施される加工が「首下R」です。この部分を角Rにし、さらに表面の凹凸をなくすことで、疲労強度の向上を図ることができます。このように、首下Rはボルトやねじの強度に大きく影響するためJISにおいても規格化されています。また、近年では応力集中への対策としてはRとテーパーを組み合わせた形状の方が有効であるとの研究結果も報告されています。
なお、首下Rは「首下転圧」といわれる工法で高精度に加工する必要があり、特に高い強度が要求される航空機エンジン用ボルトなどに適用されています。
従来の首下のR測定の課題
ねじの品質は製造技術の発展に連れて向上しましたが、完全に不良の発生を防ぐことは困難です。バリや割れ、欠け(クラック)、変形、寸法ズレ、首下Rの成形不良などが発生すれば、締結部品としての機能を果たせないばかりか、そのねじ・ボルトを使用した製品の破損といったトラブルにつながります。こちらでは、ねじ・ボルトの製造工程における一般的な不良と発生要因をご紹介します。
投影機による首下のR測定の課題
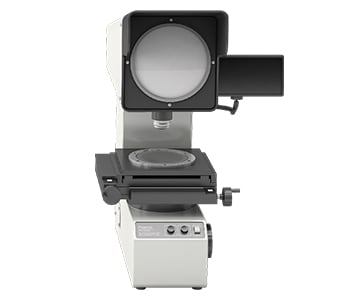
光学測定機の一種で、測定の原理は光学顕微鏡に似ています。対象物を台に乗せて、下から光を当てることで、対象物の輪郭がスクリーン上に投影されます。大型のものではスクリーンが直径1mを超えるものもあります。ねじの首下のR測定をする場合は、ねじを正確に位置合わせする必要があります。
- 形状が立体的なので、首下全面にピントをあわせるのが困難です。また、2次元投影した図ではどこまでが首下Rとするかの定義が難しく、個人によって異なるため測定値にバラつきが出ます。さらに、寸法や図面との相違箇所の数値を取得できず、輪郭形状はトレース紙への転写などが必要で、データの保存や比較が困難です。
- 投影機は、切断面に垂直な方向から観測してのみ断面形状が得られるため、対象物を首下のR部分が確認できるように置き、正確に水平出した状態で測定しなければなりません。このとき、対象物の置き方が定まらないという問題がありました。
このように、現場の誰もが正確に測定できるわけではなく、また測定できない箇所があり、さらに対象物によっては切断が必要になるなど、大きな課題となっていました。
輪郭形状測定機による首下のR測定の課題
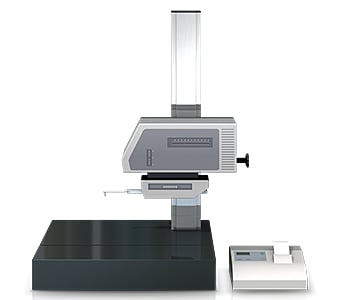
輪郭形状測定機は、スタイラスと呼ばれる触針を用いて対象物の表面をなぞることで、その輪郭形状を測定、記録する装置です。近年は触針の代わりにレーザーを用いて、非接触で輪郭をなぞることで複雑な形状の測定に対応した機種もあります。また、機種によっては上下両面の測定が可能なものもあります。
輪郭形状測定機ではボルトやねじを測定する場合は、水平出しをします。
この測定方法には、下記のような課題があります。

- 対象物を治具に固定したり、水平出ししたりなどの作業に時間がかかってしまいます。また、正確に水平出しするためには、輪郭形状測定機に関する知識やスキルが必須です。
- 輪郭形状測定機の触針は、触針アーム上の支点を中心に上下に円弧運動し、触針先端位置はX方向にも動くため、X軸データにも誤差が発生します。
- 狙った通りに針を通す作業は非常に困難で、微妙な針のズレが測定値のバラつきの原因となります。
ボルト・ねじ測定における課題解決方法
従来から使用されている一般的な測定機には、対象物の固定に時間がかかる、立体的な対象物・測定箇所に対して点や線で接触しながら測定している、という課題があります。こうした測定の課題を解決すべく、キーエンスでは、ワンショット3D形状測定機「VRシリーズ」を開発しました。
対象物の3D形状を非接触で、かつ面で正確に捉えることができます。また、ステージ上の対象物を最速1秒で3Dスキャンして3次元形状を高精度に測定することができます。このため、測定結果がバラつくことなく、瞬時に定量的な測定を実施することが可能です。ここでは、その具体的なメリットについて紹介します。
メリット1:「面」全体の形状を取得。だから誰でも測定できる
測定アルゴリズムとハードウェアを全面的に見直し、最速1秒という測定スピードを実現。一瞬で面全体の情報をスキャンします。ねじの首下Rやねじ山のピッチなど、狙ったポイントも自由に測定が可能。人による測定値のバラつきもありません。
「VRシリーズ」は、最速1秒という圧倒的なスピードで、大幅なN増しや業務時間の短縮を実現します。これにより測定品質の向上、検査要員から生産要員への転換、増産の後押しなどにつながります。試作品の評価や出荷前の検査など、速さがあらゆる測定業務を改善します。

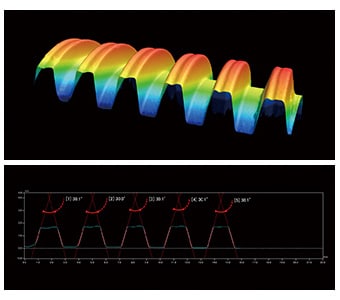
メリット2:バラつきが生じない
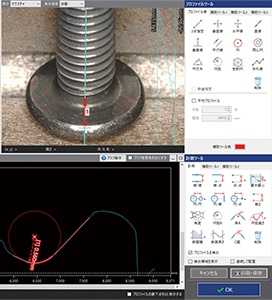
スキャンした3D形状のデータに対して、パソコンの画面上で多彩な補助ツールを使って、任意の位置に正しく垂直なプロファイル線を引くことができるため、測定結果にバラつきが生じません。たとえば、ツールの円筒軸ツールを使うと、ボルトやねじに対してバラツキなく、測定ラインを決定できます。
一度ワークをスキャンすれば、過去の測定時とは異なる箇所のプロファイル(断面形状)を測定することも可能です。わざわざ同一の固体を再び用意して再測定する必要はありません。また、過去のデータを活用して、ロットや加工条件、材料などが異なる同一形状のワークとの差分チェックも簡単に実現します。
メリット3:対象物の大きさを判断し測定範囲を自動設定
「VRシリーズ」は、対象物の広がりや高さを自動的に認識し、最適な測定範囲を自動設定するSmart
Measurement機能を搭載。一般的な測定機における測定長やZ範囲などの設定が一切不要なので、一部だけ測定し損ねる、というようなミスが起こりません。
また、3次元での位置も、自動で精度高く合わせることができます。傾きや基準面、高さのズレなど、さまざまな要素を加味して、微調整が簡単に行えます。
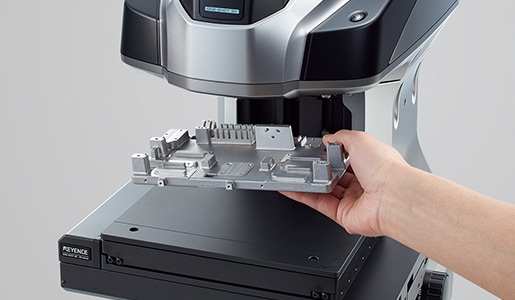
まとめ:測定しづらいボルトやねじ各部の形状測定を飛躍的に改善・効率化
「VRシリーズ」なら、高速3Dスキャンにより非接触で対象物の正確な3D形状を瞬時に測定可能。外径や有効径、谷の径やねじ山の角度、さらにピッチや首下Rなど難しい測定も最速1秒で完了。従来の測定機における課題をすべてクリアすることができます。
- 非接触なので、スタイラスが届かない部分も断面測定が可能。首下Rもねじ山ピッチも簡単かつ正確に測定することができます。
- 人による測定値のバラつきを解消し、定量的な測定が実現します。
- 位置決めなどなしに、ステージに対象物を置いてボタンを押すだけの簡単操作を実現。測定作業の属人化を解消します。
- 簡単・高速・高精度に3D形状を測定できるため、短時間で多くの対象物を測定することができ、品質向上に役立てることができます。
他にも、過去の3D形状データやCADデータとの比較、公差範囲内での分布などを簡単に分析できるため、製品開発や製造の傾向分析、抜き取り検査などさまざまな用途で活用することができます。