樹脂成形品のうねり・反りを可視化する方法
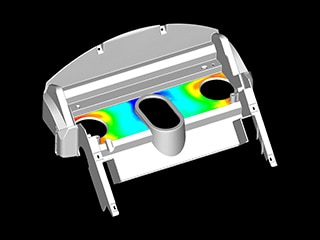
樹脂成形(プラスチック)品で多いトラブルとして『うねり』『反り(ソリ)』などの形状変化が挙げられます。安定して樹脂成形を行うには、温度や圧力、樹脂材料の量や注入速度、成形条件の管理が重要。さらに樹脂は、一般的に温度が高いほど膨張し、低いほど収縮するという特性を持つため、成形収縮率も考慮した金型設計なども求められます。そこで『うねり』『反り(ソリ)』などをいち早く発見し、原因究明および再発防止対策を講じなければなりません。そのためには樹脂成形品の表面形状を正確に計測する必要があります。しかし、従来の方法では、表面全体の正確な測定が困難でした。
キーエンスの3Dスキャナ型 三次元測定機『VL-700シリーズ』は、『うねり』『反り(ソリ)』などを可視化することが可能です。ここでは、樹脂製品における形状や表面の欠陥・不良の種類、それらが発生するメカニズムなどの基礎知識に加え、従来の測定方法における課題と、キーエンス『VL-700シリーズ』による課題解決ソリューションを紹介します。
- 樹脂成形品における欠陥・不良の種類
- 樹脂成形品で欠陥・不良が発生するメカニズム
- 従来のうねり・反りの測定方法と問題点
- 樹脂成形品のうねり・反りの可視化を実現する方法
- 従来は不可能だったうねり・反りの可視化を実現
樹脂成形品における欠陥・不良の種類
次に樹脂成形品における形状や表面の欠陥・不良について紹介します。 『うねり・反り』のほか、さまざまな欠陥・不良があり、樹脂成形においては注意すべき項目となります。
- 反り(そり)・うねり
-
成形品が一方向に歪んでいる状態を『反り(そり)』と言います。また、製品の表面に緩やかな凹凸状の形状変化がある状態を『うねり』と呼びます。反りの要因は、金型から取り外す際の外力、また融解樹脂の収縮率の違い、そのほか金型温度、射出速度、冷却時間、射出・保圧時間、形状・構造、残留応力など、さまざまな要因が考えられます。
- ヒケ(シンマーク)
-
ヒケとは、成形品の表面がくぼんでしまう現象です。樹脂は、冷却・固化するときに収縮しますが、その際に樹脂の絶対量が不足することにより発生します。また、ヒケが成形品内部に発生する現象を『気泡(ボイド)』や『内ヒケ』とも言います。
樹脂成形品で欠陥・不良が発生するメカニズム
樹脂成形品でうねり・反りが発生する要因はさまざまですが、射出成形などの金型成形品の場合、「金型温度」「射出速度」「冷却時間」「射出・保圧時間」「形状・構造」「残留応力」など考えられます。
- 金型温度
-
一般的に金型温度が低いほうがうねり・反りが発生しにくくなります。ただし、低温で成形しても成形品の使用温度が高い場合は、後収縮による変形が発生する恐れがあります。そのため、金型温度は使用条件を考慮して設定する必要があります。また、金型温度が不均一な場合でも温度差によるうねり・反りが発生する可能性があります。
- 射出速度
-
射出速度が速い、または遅い場合にうねり・反りが発生することがあります。うねり・反りが発生する場合、射出速度の調整を行い、変形量の少ない条件に調整する必要があります。
- 冷却時間
-
成形時の冷却時間が長いほうが変形を抑えられます。ただし、冷却回路が長い場合、IN側とOUT側で冷却に時間差が発生し、それが温度差となり、うねり・反りの原因になる場合もあるので注意が必要です。変形を抑えるためには、全体を均一に時間をかけて冷却することが大切ですが、時間をかければ生産効率が低下します。
- 射出・保圧時間
-
一般的に射出時間と保圧時間の合計がゲートシール時間(金型に樹脂が充填され、ゲートが固化するまでの時間)より長くなるように設定します。この射出・保圧時間がゲートシール時間より短いと変形が発生する可能性があります。さらに保圧時間が短いと金型内から樹脂が逆流して品質のばらつきにつながります。
- 形状・構造
-
リブ形状の問題による剛性不足や板厚の不均一など、形状や構造に問題がある場合もうねり・反りが発生します。このように形・構造の場合は設計から見直す必要があります。
- 残留応力
-
残留応力が残っていると、加工後にうねり・反りが発生する可能性があり、成形直後は問題がなくても、その後に徐々に変形が起こることもあります。
従来のうねり・反りの測定方法と問題点
樹脂成形品のうねり・反りの測定方法には、一般的に『ノギス』『三次元測定機』『輪郭形状測定機』などが用いられます。ただ、正確にうねり・反りの測定ができない、あるいは非常に時間がかかるなどの問題点がありました。
- ノギス
-
ノギスは、長さのほか、外径や内径、段差などを測るための測定機です。対象物を挟んで長さや外径を測ったり、測定対象間にクチバシを差し込んで内径を測ったり、デプスバーもしくはステップを用いて段差や穴の深さを測ります。ただし、手作業での測定になるため時間もかかり、接触式のため表面にキズをつけてしまう恐れもあります。さらに1点ずつ測定するので、全体形状を捉えることができないという課題がありました。
- 三次元測定機
-
三次元測定機は、ステージ上の対象物に接触子を当て、縦・横・高さから三次元の座標を取得し、対象物の寸法・位置関係・輪郭形状・幾何公差などを高精度に測定できる測定機です。ノギスでは不可能な形状測定も可能ですが、点で測定するということは同様です。そのため、どうしても全体形状を正確に可視化するという面で不利でした。また、うねり・反りのような変形を可視化するためには、測定箇所を増やす必要があり、時間と手間がかかります。
- 輪郭形状測定機
-
輪郭形状測定機は、スタイラスと呼ばれる触針を使い、対象物の表面をなぞりながら輪郭形状を測定する装置です。形状変化を測定するという点においては適していますが、線で測定するので全体把握ができないという欠点があります。さらに面以外の構造物があると測定できないので、サンプルによっては測定不可の場合もあります。そのほか、スタイラスで表面をなぞるように測定するので、キズがついてしまう可能性もあります。
樹脂成形品のうねり・反りの可視化を実現する方法
従来使用されている測定機には課題があり、『立体的な対象物・測定箇所にたいして、点や線で接触しながら測定する』という共通点があります。こうした課題を解決するために誕生したのがキーエンスの3Dスキャナ型 三次元測定機『VL-700シリーズ』です。3D形状の対象物を非接触かつ面で正確に捉えることで、これまで不可能だったうねり・反りの可視化を実現します。
メリット1:うねりや反りを一発で測定。歪み箇所を即特定!
複雑な形状をノギスや三次元測定機、輪郭形状測定機で測定すると、多くのポイントを測定する必要があるので時間がかかり、点や線での測定になるので3D形状の測定が困難でした。そのため最適な成形条件を決定するには、時間をかけて測定し、その後に組み付けて確認し、金型や成形条件を再設定するという繰り返しが必要です。
しかし、キーエンスの3Dスキャナ型 三次元測定機『VL-700シリーズ』があれば、ワンショット8秒のスキャンと簡単操作で測定が完了します。対象物全体の3D形状を面で捉えて、形状の不良箇所とその詳しい数値などを可視化できるので、大幅な時間短縮が可能です。さらに偏差を数値だけではなく、カラーマップで表示できるので一目瞭然です。
たとえば、嵌合部などの取付部については、幾何公差“平面度測定”を実施することで、歪み箇所をすぐに特定でき、成形時の条件を素早く修正できます。また、量産品であれば、組み付け不良の原因特定・対策もスムーズになり、定量的に測定した形状データが得られるので、うねり・反りの許容値(公差)を数値で管理したり、傾向分析にも役立てたりすることができます。


メリット2:自由形状、複雑形状も非接触で簡単に測定!
ノギスや三次元測定機、輪郭形状測定機などの接触測定とは違い、キーエンスの3Dスキャナ型 三次元測定機『VL-700シリーズ』は非接触で形状を測定可能です。何百万点の形状データを一瞬でスキャンするので、これまで測定が困難だった自由形状・複雑形状の全体形状の把握が可能になります。さらに測定したデータをCADと比較し、最適な金型寸法を決定することにも役立ちます。

メリット3:カラーマッピングで形状を可視化できる!
樹脂成形品において、意図としない、うねりや反りなどの形状不良には注意が必要です。しかし、従来の非接触式測定機では、全体のうねり・反りの測定が困難でした。
キーエンスの3Dスキャナ型 三次元測定機『VL-700シリーズ』なら、スキャンしたデータの高さなどをカラーマッピングが可能。対象物のうねり・反りを視覚的に判断しやすいカラーマップ画像データを出力でき、不良箇所の把握が容易に行なえ、共有も簡単です。また、『VL-700シリーズ』は、対象物のシビアな位置決め不要で、対象物をステージに置くだけで自動的に画像を補正し、定量的な測定・検査が実現します。

従来は不可能だったうねり・反りの可視化を実現
キーエンスの3Dスキャナ型 三次元測定機『VL-700シリーズ』なら、非接触でうねり・反りなどの形状変化を正確に測定可能です。
- 面で捉えるので対象物全体において、うねり・反りを可視化できます。
- 非接触なので柔らかい素材でも変形を気にせず、高精度な形状測定が可能です。
- 位置決めは不要。対象物をステージにおいてボタンを押すだけの簡単操作で測定が完了します。
- 3D形状をカラーマップで表現可能。視覚的にわかりやすいデータを共有できます。
- 複数の測定データの定量的な比較・分析が簡単にできます。
今回は、樹脂成形品のうねり・反りの可視化について説明しましたが、半導体の現場でも欠かせないウェハなどのうねり・反りの可視化、スパッタリングによって形成された薄膜のうねり・反りの可視化など、使用できる場所は多岐にわたります。