テーパーの形状を正確かつ簡単に測定する方法
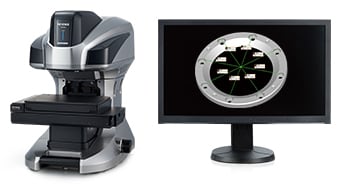
テーパー(taper)は、傾きや傾斜を示すために使われる用語です。JIS Z
8114:1999では、「投影図または断面図における相交わる二直線間の相対的な広がりの度合い」となっています。似た形状に「勾配」がありますが、設計上テーパーとは使い分けられることが一般的です。
本項では、テーパーを施す目的やテーパーを用いる部品、計算方法や加工方法などの基礎知識と、測定の課題と解決方法を紹介します。
テーパーとは
テーパーとは、細長い構造物の径・幅・厚みなどが、先細りになっている状態を指します。テーパーの形状にはさまざまな種類があり、目的に応じて使い分けられます。テーパーは構造物に強度を持たせたり、嵌合を容易にすることができ、プレスまたは切削加工などで成形します。
なお、テーパー状に設計することを「テーパーをつける」といい、テーパーの角度が大きい場合は「テーパーがきつい」、小さい場合は「テーパーがゆるい」といいます。テーパーに似た言葉に勾配がありますが、これらは厳密に使い分ける必要があります。
テーパーと勾配の違い
両側に角度の傾斜が付いている形状を「テーパー」、一方が水平で片側にだけ傾斜が付いている形状を「勾配」といいます。たとえば、同じ円錐上の素材で、中心線を基準に片側だけの傾きを対象にするのであれば勾配ですが、両側の傾斜を対象にするのであればテーパ―になります。

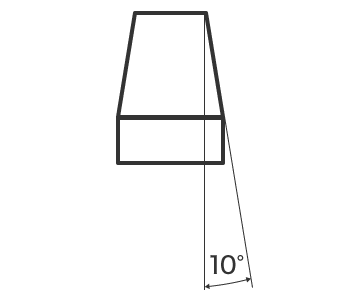
テーパーと勾配の図面表記
テーパーと勾配は、それぞれ記号と数値で示します。テーパーの大きさは、テーパー角やテーパー比で表します。一方、勾配は勾配比という値で表します。

- A
- テーパー記号とテーパー形状を同じ向きにする。
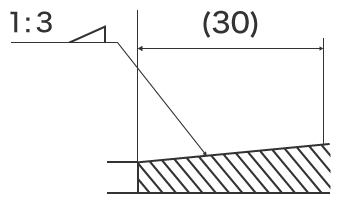
テーパーを用いた部品
テーパーはピンや軸を支えるベアリング、配管さらにヒートシンクやフランジなど、多くの部品に用いられています。形状はテーパーですが、それぞれ目的は異なり、その形状にも特徴があります。
ねじ・ベアリング・嵌合部など
距離に対し、径が線形に変わるテーパー(線形テーパー)が用いられます。側面の角度は一定で、テーパーの度合いはテーパー角(角度)またはテーパー比で表されます。
エンジン冷却フィン・ヒートシンク
距離に対し、径が指数関数的に変わるテーパー(指数関数テーパー)が用いられます。側面の形状は、根元から離れると急に細くなり、先は非常に細くなります。このため、ピッチを小さくすることができ、重量や振動を軽減できます。
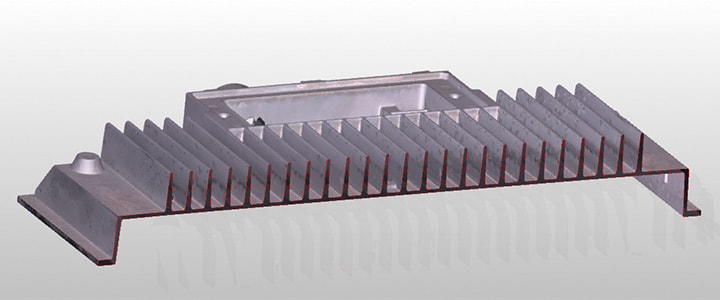
その他、配管や航空機の機体など流体の抵抗を抑えたい部品には、放物線のような形状の「放物線テーパー」が用いられます。また、ピンなど部品同士を結合する部品には通常のテーパーとは逆に、先ほど太くなる「逆テーパー」が用いられます。
テーパー角の計算
通常、図面ではテーパーはテーパー比で表します。しかし、旋盤による加工などでは、テーパー角の値が必要になる場合があります。
テーパー比
太い方の寸法と細い方の寸法の比率です。たとえばテーパー比が3:100なら100mmあたり直径が3mm細くなります。
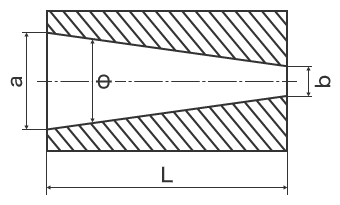
- a
- 大きい方の径
- b
- 小さい方の径
- L
- 長さ
- Φ
- テーパー角
テーパー角
テーパー角は以下の式で計算することができます。
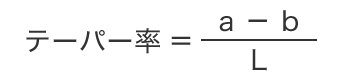

たとえば、図面に指示されたテーパー率が3/100の場合、テーパー角は以下のように計算できます。

テーパーの加工法
テーパーは、旋盤やプレスで加工します。プレス加工の場合は金型を作るときにテーパーを設定します。旋盤の場合は、刃物台の角度調整を使って加工します。ここでは、旋盤によるテーパー加工を紹介します。
旋盤とは、材料を回転させて削る工作機械のことです。加工する物を回転させ、固定した工具によって工作物を削って作ります。加工物を回転して削ることから、先に向かって細くなっていくテーパー加工に適しています。旋盤では、テーパー刃エンドミルの角度をテーパー角の1/2で指定します。なお、テーパー角の1/2は勾配角です。
①旋盤を回転させて、角度を調整する
↓
②旋盤のハンドルを操作して削る
↓
③端まで削ったら刃先が外れるまで戻す
↓
④これを繰り返し、求める形状になるまで削る
超精密旋盤では、マイクロオーダーの微細テーパーも加工可能です。したがって、品質管理には精度の高い測定機が必要になります。
従来のテーパー測定の課題
テーパーの加工によって狙い通りの寸法(公差内)・形状が得られているかどうかの確認は非常に重要です。特に円錐状のテーパーは立体的な形状であるため、高精度かつ定量的な3D形状の測定が求められます。
しかし、従来の投影機や輪郭形状測定機、テーパーゲージなどの場合、正確に測定するには難易度が高くバラつきが出るなど、さまざまな課題がありました。
投影機によるテーパー測定の課題
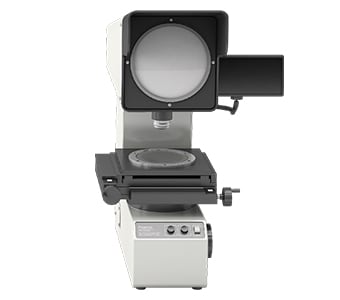
光学測定機の一種で、測定の原理は光学顕微鏡に似ています。対象物を台に乗せて、下から光を当てることで、対象物の輪郭がスクリーン上に投影されます。大型のものではスクリーンが直径1mを超えるものもあります。2次元投影では確認できない奥まったテーパー部分は、サンプルを切断して測定します。
この測定方法には、下記のような課題があります。
- 一般的な投影機のレンズは、対象物の一部にしかピントが合いません。そのため、測定箇所ごとに手動でピント合わせが必要です。たとえば、対象物が円錐形の場合、測定箇所ごとに細かいピント合わせが求められます。人によってピントを合わせる位置が異なると測定誤差が生じるほか、測定箇所が多いほどピント合わせに時間がかかるという問題があります。そして、断面形状は、対象物を切断して測定する必要があります。
- 形状比較をするとき、10倍に拡大した図面を投影像に重ね合わせ、差異を目視で確認する必要があります。また、寸法や図面との相違箇所の数値を取得できず、輪郭形状はトレース紙に転写するなどが必要で、データの保存や比較が困難です。
このように、現場の誰もが正確に測定できるわけではなく、また測定できない箇所があり、さらに対象物によっては切断が必要になるなど、大きな課題となっていました。
輪郭形状測定機によるテーパー測定の課題
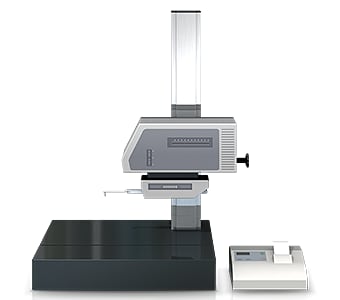
輪郭形状測定機は、スタイラスと呼ばれる触針を用いて対象物の表面をなぞることで、その輪郭形状を測定、記録する装置です。近年は触針の代わりにレーザーを用いて、非接触で輪郭をなぞることで複雑な形状の測定に対応した機種もあります。また、機種によっては上下両面の測定が可能なものもあります。
輪郭形状測定機では、測定したいテーパーの形状に対して、垂直方向に正確な測定ラインを取る必要があります。
そこで、下記のような課題がありました。

- サンプルを治具に固定したり、水平出ししたりなどの作業に時間がかかってしまいます。また、正確に水平出しするためには、輪郭形状測定機に関する知識やスキルが必須です。
- 輪郭形状測定機の触針は、触針アーム上の支点を中心に上下に円弧運動し、触針先端位置はX方向にも動くため、X軸データにも誤差が発生します。
- 狙った通りに針を通す作業は非常に困難で、微妙な針のズレが測定値のバラつきの原因となります。
テーパー測定における課題解決方法
従来から使用されている一般的な測定機での課題を見直すと、ある共通点がわかります。それは、立体的な対象物・測定箇所に対して、点や線で接触しながら測定しているということです。
こうした測定の課題を解決すべく、キーエンスでは、ワンショット3D形状測定機「VRシリーズ」を開発しました。対象物の3D形状を非接触で、かつ面で正確に捉えることができます。ステージ上の対象物を最速1秒で3Dスキャンして3次元形状を高精度に測定することができます。そのため、測定結果がバラつくことなく、瞬時に定量的な測定を実施することが可能です。具体的なメリットを下記に挙げます。
メリット1:サンプルカットしなくても測定できる
たとえば、刃先工具やヒートシンクのフィンのようにピッチが小さく奥まった対象物の場合、接触式測定機では底面までプローブなどの測定子が届かないため測定は困難です。
「VRシリーズ」なら、断面をカットして平面測定をしていたような対象物でも、仮想的に切断することでテーパーなど断面形状を測定することができます。このため、断面をカットすることなく奥まった部分の測定が可能です。
また、事前に測定項目を登録できる解析テンプレートを使用してワークの形状解析ができるので、これまで時間がかかっていたり、不可能だった測定も短時間で可能になります。
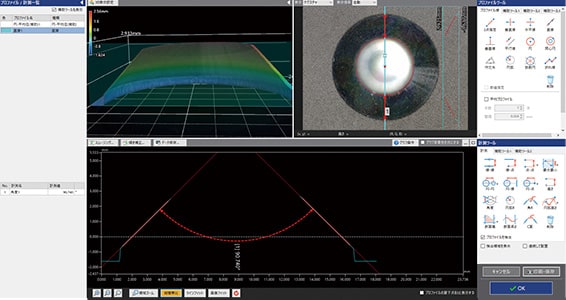
メリット2:最大200mm×100mmの広範囲を測定可能
測定に必要な作業は、対象物をステージに置いて、ボタンを押すだけ。厳密な位置決めなどの事前準備が不要なので、測定機の知識や経験がなくても、すぐに高精度な測定が可能です。
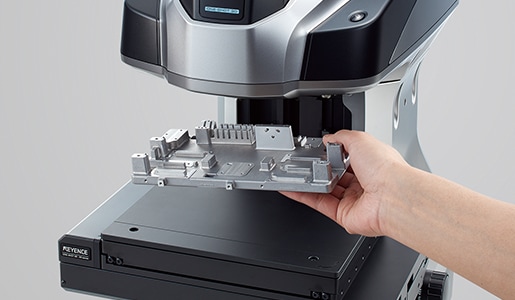
従来の測定機と異なり、ステージに置いた対象物の特徴を抽出し、自動的に位置補正することができます。これまで多くの手間と時間を要した厳密な位置調整は不要です。そのため、測定作業が属人化することなく、不慣れな方でも簡単・瞬時に測定することができます。
まとめ:測定しづらいテーパー面形状測定を飛躍的に改善・効率化
高速3Dスキャンにより、非接触で対象物の正確な3D形状を瞬時に測定できる「VRシリーズ」であれば、従来の測定機における課題をクリアすることできます。
- 対象物を切断することなく断面測定が可能です。
- 人による測定値のバラつきを解消し、定量的な測定が実現します。
- 位置決めなどなしに、ステージに対象物を置いてボタンを押すだけの簡単操作を実現。測定作業の属人化を解消します。
- 簡単・高速・高精度に3D形状を測定できるため、短時間で多くの対象物を測定することができ、品質向上に役立てることができます。
他にも、過去の3D形状データやCADデータとの比較、公差範囲内での分布などを簡単に分析できるため、製品開発や製造の傾向分析、抜き取り検査などさまざまな用途で活用することができます。