シボをすばやく正確に測定する方法
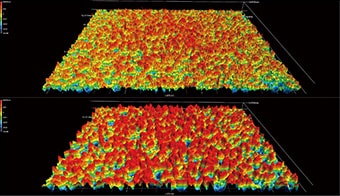
金属やプラスチック、ガラス・石などの表面に与えられた、自然の樹木や皮革模様をシボといいます。シボは、高級感や付加価値はもちろん、ときには耐久性や安全性を高めるために施し、パソコンやプリンターといったOA機器から自動車の内装パネル、携帯電話や家庭用ゲーム機などさまざまな製品に使用されています。
ここでは、シボの金型作成の原理やポイントなどの基礎知識や、測定における課題とその解決方法について説明します。
シボとは
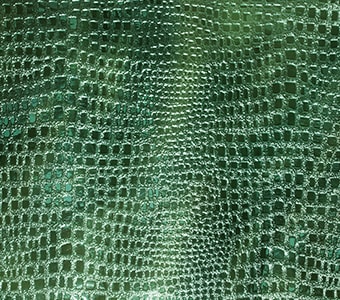
「シボ」といえば、革の表面の説明で見かけることが多いかと思います。漢字では「皺」と書き、英語では「texture」と言われます。製品の表面に自然の樹木や皮革模様、つや消し模様を付与するシボ加工は製品の寿命を長く保ち、外観の美しさや高級感を演出します。
シボを施す加工を「シボ加工」といい、梨地処理またはエッチングとも呼ばれます。加工法には、凹凸に加工した金型(キャビティまたはコア)を対象物に転写する方法や、薬品によって金属を溶解するため化学腐食(ケミカルエッチング)、サンドブラストなどがあります。
シボ金型作成の原理
シボは、シボ金型に描かれた柄を対象物に転写して再現します。このため、シボ金型は、より本物に近く立体感のあるシボを再現するために、精巧な加工が必要です。その加工は、転写と腐食を繰り返して行います。どのような柄を再現する場合でも、加工原理は共通しています。その工程を以下の断面図を使って示します。
-
1回目の転写
-
1回目の腐食
- A
- 金型
- B
- 耐酸インク
- C
- 耐酸インクを塗布していない部分の金属は、腐食し除去される。
-
2回目の転写
-
2回目の腐食
- A
- 金型
- B
- 耐酸インク
- C
- 1回目で除去された部分は、さらに深くなる。
- D
- 2回目の腐食で新たに除去された部分。
-
3回目の転写
-
3回目の腐食
- A
- 金型
- B
- 耐酸インク
- C
- 3回目の腐食で新たに除去された部分。
このように転写と腐食を繰り返すことで、立体感のある表情豊かなシボ金型ができあがります。単純なシボ柄なら1回、複雑な柄では10回以上を繰り返す場合があります。
なお、シボ加工は全工程の中で約8割が手作業で行われます。特に転写は職人技ともいえる技術と丹念な作業が要求され、多くの工数を要する工程です。
シボ加工のポイント
多くの場合、シボ加工は機械加工や磨き作業が終了した後に行います。このため、修正や修正が不可能なほどの欠陥が発生した場合、生産計画に大きなダメージを与えます。このことから、シボ加工は大変大きなリスクを背負っている最終工程であることが理解できると思います。
そこで、一般的なシボ加工における、不具合の発生リスクを低減させるために、留意すべきポイントを以下に挙げます。
金型表面をサンドペーパーや砥粒で磨く
金型表面のマイクロクラックや機械加工による表面変質層をきれいに取り除きます。
金型の材質による欠陥を防ぐ
金型には、ボイド(気泡)、不純物、炭化物の混入など、材料欠陥が含まれる確率の低い鋼材を選定します。
鋼材の熱処理、切り出し方向、圧延方向はできるだけ同一にする
むらになったり、均一なシボを得ることができません。また、溶接補修した部分にはシボ加工を行わないことも重要です。
抜き勾配と肉厚に注意する
金型側面の処理では、抜き勾配をできるだけ大きく設定します。また、金型側面に処理する場合には成形品の肉厚を厚くして収縮量を意図的に大きくし、金型表面の温度制御がしやすい構造の冷却構造やカートリッジヒーター構造を採用します。
その他、シボ加工した後に機械加工するように工程を変更しても、品質が向上する場合があります。さらに、成形材料の種類、着色、ガラス繊維の配合などによってもシボのでき栄えは視覚的に変化します。この場合、過去のデータを参考に、シボの種類や深さなどを選定すると良いでしょう。
従来のシボの測定における課題
シボは、深さや高さ、パターンの形状が品質に大きく影響します。そして、シボの欠陥は美観や手触りだけでなく、滑り止めを目的としたシボの場合は安全性やグリップ感、表面欠陥を目立たなくするためのシボの場合は生産性に影響を与えます。このため、全面にわたって設計通りのシボが施されていることを確認するために、測定・検査しなければなりません。
従来、シボの測定や定量化のためには、顕微鏡や粗さ計を使用していました。しかし、以下のような測定課題がありました。
粗さ計や変位計によるシボの測定課題
粗さ計は表面の粗さの測定は、高さ方向は点または線でしか測定できないため、正確に形状を把握するには測定箇所を増やす必要があります。プローブまたは針を移動することで測定するため、測定箇所が多くなるほど測定時間がかかります。また、対象物設置後の設置補正などが必要で、測定ポイントが測定者によってもバラつき、測定値の信頼性に欠けます。
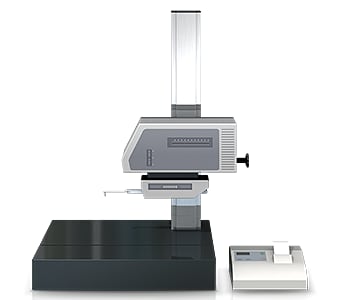
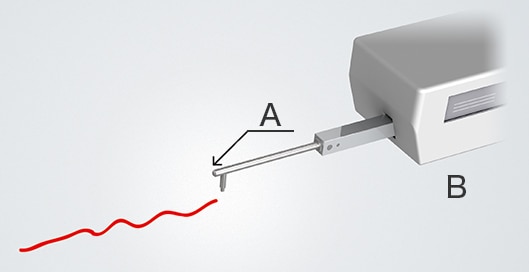
- A
- 触針
- B
- 検出器
顕微鏡によるシボの測定課題
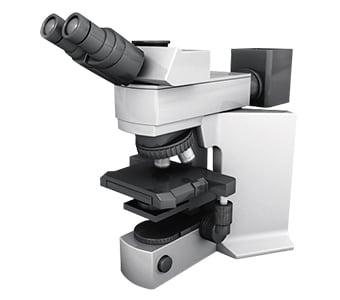
顕微鏡は粗さ計とは異なり「面」で情報をとらえることができます。ステージの移動量で溝の幅を、ピント合わせの移動量で深さ方向を測ることもできます。
ただ、人が目合わせで測定するため、測定結果に個人差が出たり、そもそも測定機ではないので、測定結果を定量化できなかったり、定量化した測定値の信頼性が低いという不安があります。
シボの測定における課題解決方法
従来から使用されている一般的な測定機には、立体的な対象物・測定箇所に対して点や線で接触しながら測定している、測定値の信頼性が低い、という課題があります。こうした測定の課題を解決すべく、キーエンスでは、ワンショット3D形状測定機「VRシリーズ」を開発しました。
対象物の3D形状を非接触で、かつ面で正確に捉えることができます。また、ステージ上の対象物を最速1秒で3Dスキャンして3次元形状を高精度に測定することができます。このため、測定結果がバラつくことなく、瞬時に定量的な測定を実施することが可能です。ここでは、その具体的なメリットについて紹介します。
メリット1:最大200mm×100mmの広範囲を測定可能
測定に必要な作業は、対象物をステージに置いて、ボタンを押すだけ。厳密な位置決めなどの事前準備が不要なので、測定機の知識や経験がなくても、すぐに高精度な測定が可能です。
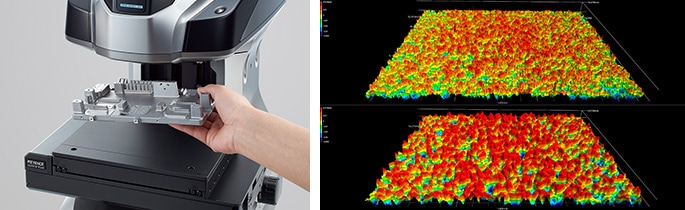
従来の測定機と異なり、これまで多くの手間と時間を要した広い面積に点在するシボの高さパラメータも測定できます。また、さまざまな測定を簡単に実現できる計測ツールを搭載。測定作業が属人化することなく、不慣れな方でも簡単・瞬時に測定することができます。
メリット2:トレーサビリティに対応した測定システム
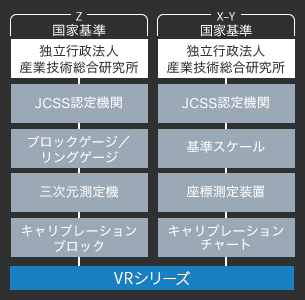
「VRシリーズ」は非接触式の三次元測定機でありながら、国家基準につながるトレーサビリティを確保。測定精度は正確性、繰り返し性の2つの性能保証をしており、安心できる測定結果、信頼性の高い測定結果を得ることができます。また、本体とキャリブレーションボードに証明書を標準添付しています。
このように、「VRシリーズ」はトレーサビリティに基づいた測定システムのため、測定機器として使用できます。
さらに、標準で検査成績書・校正証明書付きのキャリブレーションゲージを添付。ゲージは、JCSS認定事業者の基準スケールにつながります。どなたでも、現地で正確に校正をしていただくことが可能です。
まとめ:測定しづらいシボの形状測定を飛躍的に改善・効率化
「VRシリーズ」なら、高速3Dスキャンにより非接触で対象物の正確な3D形状を瞬時に測定可能。シボの高さや粗さなどの難しい測定も最速1秒で完了。従来の測定機における課題をすべてクリアすることができます。
- 面で測定するので、広い面積のシボも簡単に測定可能。粗さのさまざまなパラメータも測定することができます。
- 人による測定値のバラつきを解消し、定量的な測定が実現します。
- 位置決めなどなしに、ステージに対象物を置いてボタンを押すだけの簡単操作を実現。測定作業の属人化を解消します。
- 簡単・高速・高精度に3D形状を測定できるため、短時間で多くの対象物を測定することができ、品質向上に役立てることができます。
他にも、過去の3D形状データやCADデータとの比較、公差範囲内での分布などを簡単に分析できるため、製品開発や製造の傾向分析、抜き取り検査などさまざまな用途で活用することができます。