溶接ビードの複雑な3D形状を瞬時かつ正確に測定する方法
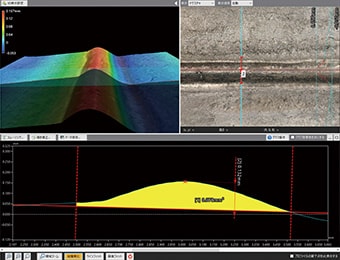
溶接は、2つの部材(母材)の接合部に、熱または圧力などのエネルギーを用いて、両方の部材もしくは溶加材を加え、一体化する接合方法です。このとき溶接部分(溶接肉盛り部)にできる溶接ビードは、接合強度と製品品質に大きく関わる重要箇所です。溶接ビードの形状によって、適切に溶接できているか、欠陥・不良がないかを評価することができます。しかし、溶接ビードを的確に評価するには、その複雑な3次元形状を定量的に測定する必要があり、それにはさまざまな課題がありました。
ここでは、溶接ビードの基礎知識から、簡単かつ瞬時に溶接ビードの3D形状を正確に測定する最新の手法までを解説します。
溶接ビードとは
溶接ビードとは、アーク溶接やレーザー溶接など各種溶接方法で母材を接合したとき、接合部分の表面でかまぼこのような凸形状に盛り上がっている部分を指します。ビードがひも状であることから、ひも出し加工と呼ばれることもあります。
配管など金属パイプの製造においては、ロール成形の後に高周波溶接で母材を結合した部分に溶接ビードができます。他にもさまざまな手法での溶接において、起伏がほとんどない形状であっても金属が母材と溶融した接合部分は溶接ビードといわれます。

最適な溶接ビードの寸法と形状について
代表的な溶接手法の1つであるアーク溶接で、溶接ビード形状について解説します。
溶接ビードは、寸法の規定を満たすことで適切な形状となります。
溶接ビード寸法の規定と形状
溶接ビードの寸法は規格化されています。これらの要件を満たすことで最適な溶接ビードの形状が得られます。開発・設計段階での考慮はもちろん、工程で要件を満たしているかどうかも重要です。
溶接ビードの最小厚さである「のど厚」や、母材が溶融した部分の頂点から母材表面の長さである「溶け込み深さ」など溶接部断面における寸法が規定されています。
そして、外観からわかる寸法の規定項目としては、接合の付け根部分にあたる溶接ルート部から溶接ビード止端までの最小長さ「脚長(きゃくちょう)」があります。たとえば、すみ肉溶接では下図のように、脚長が薄いほうの母材の板厚の80%以上の長さを満たしているかどうかが、最適なビード幅の判断基準となります。たとえば、薄いほうの母材の板厚が20mmの場合、16mm程度の脚長が必要となり、ビード幅を決定します。脚長の例を以下の図に示します。
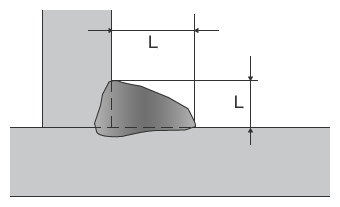
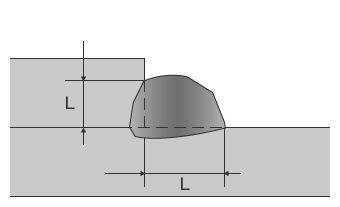
溶接ビードの寸法と電流量
アーク溶接では、溶接時の電流量が、溶接ビードの寸法を左右する要因の1つに挙げられます。電流が大きいほど大きくなり、小さい電流の場合は小さな形状の溶接ビードができます。溶接ビードが規定の寸法・形状を満たしていない場合、電流量やトーチの移動速度など、各種の溶接条件を見直す必要があります。
溶接ビード形状の欠陥・不良
溶接ビード表面の形状(外観)において、寸法以外にも注意すべき欠陥・不良があります。「溶接部外観検査基準(JASS 6-20011)」では、それぞれの表面欠陥に対する管理許容差や限界許容差が詳細に定義されており、欠陥に該当するか否かの判断には精度の高い検査が求められます。以下では、溶接ビードの代表的な欠陥・不良現象と原因を図とともに解説します。
オーバーラップ
- 【現象】
- オーバーラップとは、母材表面にあふれ出た溶融金属が、母材を溶融しないまま溶接ビードとして冷え固まった状態のことです。
- 【発生原因】
- 溶接速度が低いと、溶着金属量が過剰になり発生します。また、すみ肉溶接で発生する場合は、過剰な溶融金属が重力で垂れ下がり発生します。
-
余盛り不足
- 【現象】
- 余盛りとは、「開先又はすみ肉溶接で必要寸法以上に表面から盛り上がった溶着金属」とJISで定義されています。
- 【発生原因】
- 溶接条件(電流量や速度)が適切でないことが原因となり、発生します。
-
アンダーカット
- 【現象】
- アンダーカットとは、「母材または既溶接の上に溶接して生じた止端の溝」であるとJISで定義されています。
- 【発生原因】
- 一般的に溶接電流や溶接速度が過剰に高いことなどが原因となります。
-
ピット
- 【現象】
- ピットとは、「開口欠陥」とも呼ばれ、溶接金属内部に発生したガス孔が、ビード表面に放出されたときに穴となって固まった表面欠陥です。なお、溶接ビード内部のガス孔は、「ブローホール」と呼ばれる内部欠陥です。
- 【発生原因】
- シールドガスの不良や脱酸材の不足、母材開先面の油分や錆、メッキなどの表面付着材、材料中の水分などが挙げられます。
-
- A
- ピット
- B
- ブローホール
割れ(溶接ビードや母材の表面)
- 【種類と現象】
- 割れとは、溶接直後の高温状態で溶接部に発生するひび割れのことです。「凝固割れ」「液化割れ」に大別され、凝固割れは凝固時に発生する割れです。液化割れは多層溶接時に前の溶接層が次の溶接により溶けて発生する割れです。また、発生位置や形状によって、「縦割れ」「止端割れ」「横割れ」「クレーター割れ」などに分類されます。
-
- A
- 縦割れ
- B
- 止端割れ
- C
- 横割れ
- D
- クレーター割れ
形状・外観からわかる欠陥・不良以外にも、熱量の不足によって必要な溶け込み深さに対して溶け込み量が不足する「溶け込み不足」や、部分的に溶融金属が母材に溶け込んでいない「融合不良」など、接合強度に影響する欠陥・不良もあります。これらは、内部欠陥であるため、断面サンプルでの検証などが必要です。
溶接ビードの形状測定における課題解決方法
溶接ビードの品質を担保するには検査が欠かせません。良品見本やゲージと目視で比較するには高いスキルと時間を要し、人によって判断が異なることがあります。また、インラインでの自動検査装置は、多くの場合、システムや精度において研究開発段階や溶接条件出しのためのテスト、抜き取り検査や少量多品種の全数検査といった目的には向いていませんでした。
こうした溶接ビードの測定の課題を解決すべく、キーエンスでは、ワンショット3D形状測定機「VRシリーズ」を開発しました。
対象物の3D形状を非接触で、かつ面で正確に捉えることができます。また、ステージ上の対象物を最速1秒で3Dスキャンして3次元形状を高精度に測定することができます。このため、測定結果がバラつくことなく、瞬時に定量的な測定を実施することが可能です。ここでは、その具体的なメリットについて紹介します。
メリット1:最速1秒。「面」で対象物全体の3D形状を一括取得。
「VRシリーズ」は最速1秒で、面データ(ワンショットで80万点のデータ)を取得することができます。それにより、複雑な溶接ビードの3次元形状を瞬時かつ高精度に測定し、定量的な評価が可能です。
最大・最小の凹凸をカラーマップでわかりやすく表現でき、不良箇所を判別することができます。また、不良部分など任意の箇所を指定して詳細なプロファイルデータを取得することが可能です。
測定後であっても対象物を再びセットすることなく、過去に3Dスキャンしたデータから別の箇所のプロファイルデータを取得することもできます。また複数の対象物の測定データを並べて比較したり、目的の条件を複数のデータに一括適用することができます。これにより、飛躍的な工数削減と業務効率の向上が実現します。
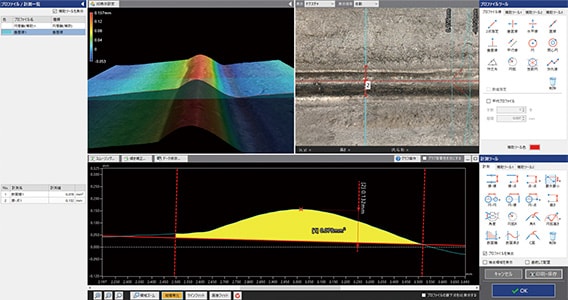
メリット2:簡単操作で、誰が測っても測定値がバラつかない
対象物をステージの上に置き、ボタンを押すだけの簡単操作で、3D形状の測定を実現しました。対象物の特徴データから自動的に位置補正が可能なため、シビアな水平出しや位置決めは不要です。また、対象物の大きさを判断して測定範囲を自動設定・ステージ移動する「Smart Measurement機能」を業界で初めて搭載し、測定長やZ範囲などを設定する手間を一切排除しました。
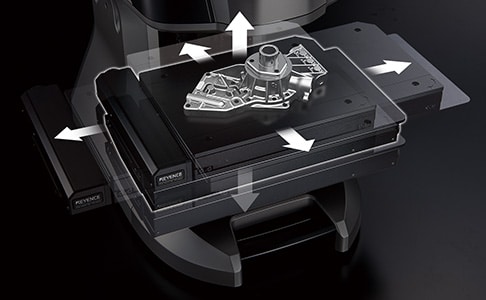
さらに、豊富な補助ツールを使用することで、目的の測定内容を直感的に設定することができます。
簡単設定に加えて、初心者でも簡単な操作を実現しているため、測定に不慣れな人でも最速1秒で正確な測定が可能です。そのため、研究開発や条件出しのテスト時だけでなく、製品の測定・検査におけるN増しも簡単に実現します。
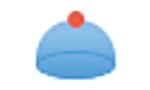
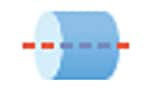
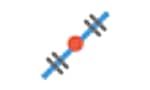
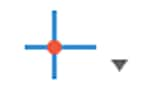
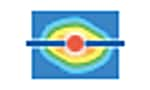
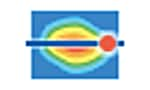
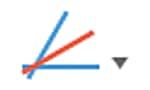
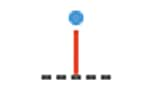
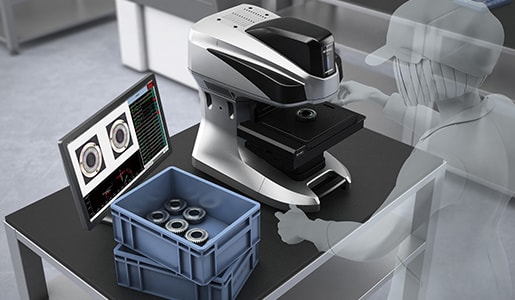
まとめ:正確な測定が難しい、溶接ビードの形状測定を飛躍的に改善・効率化
「VRシリーズ」なら、高速3Dスキャンにより非接触で対象物の正確な3D形状を瞬時に測定可能です。溶接ビードの3次元寸法や複雑な凹凸形状の把握、欠陥・不良の判別など難しい測定項目も最速1秒で完了。これまでの測定における課題をすべてクリアすることができます。
- カラーマップで溶接ビードの異常箇所を見える化することが可能です。
- 一度スキャンすれば、いつでも任意の場所のプロファイル測定や複数データの比較などが可能です。
- 位置決めなどなしに、ステージに対象物を置いてボタンを押すだけの簡単操作を実現。測定作業の属人化を解消します。
- 簡単・高速・高精度に3D形状を測定できるため、短時間で多くのN数に対応可能。品質向上に役立てることができます。
- 人による測定値のバラつきを解消し、定量的な測定が実現します。
他にも、CADデータとの比較や、公差範囲内での分布なども簡単にデータ分析ができるため、研究開発や溶接条件出しから、抜き取り検査や小ロット品の全数検査、傾向分析などさまざまな用途で活用することができます。