測定誤差について
ここでは、測定誤差の原因とその解消方法についてご説明します。
測定誤差とは
あるべき測定結果(測定値)に対して、何らかの要素が影響して測定結果が異なるとき、その差を「測定誤差」と呼びます。
測定誤差の原因は様々であり、原因に応じた対処が必要になります。測定誤差が生じたときには、「なぜその測定誤差が発生したのか」を十分に検討したうえで対策をおこない、製造物の品質安定につなげることが重要です。
測定誤差の原因
測定誤差は、測定器に依存した測定誤差・測定者に依存した測定誤差・環境条件や対象物に依存した測定誤差の3つのパターンに分類することができます。各パターンにおける代表的な原因を下記にまとめます。
測定誤差の種類 | 測定誤差の原因 |
---|---|
測定器に依存した測定誤差 |
|
測定者に依存した測定誤差 |
|
環境条件や対象物に依存した測定誤差 |
|
測定器に依存した測定誤差の解消方法
使用している測定器のスペックと測定用途を合わせることはもちろん、設置・使用の方法によっても誤差を解消できることがあります。また、経年による消耗品の劣化などによる測定精度の低下といったことが原因となる測定誤差の解消方法を挙げます。
基準距離での測定による繰り返し精度向上
三角測距方式(三角測量方式・三角測定方式)の変位計では、対象物の場所によって繰り返し精度が変わります。下図のように対象物が基準距離に近いほどスポット径が絞られた状態になり、繰り返し精度が向上します。測定距離を変更することが難しい場合は、基準距離が合った光学系を持つ測定器を選定・使用することで、測定誤差を抑えることができます。
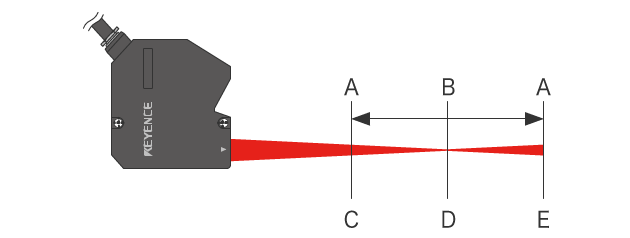
- A
- 悪い
- B
- 良い
- C
- NEAR側
- D
- 基準距離
- E
- FAR側
ただし、レーザ変位計における繰り返し精度は、測定精度とは異なります。繰り返し精度とは、“ワークもセンサヘッドも静止させた状態での測定値のバラつき”のことです。つまり、同一の物体を繰り返し移動し、まったく同じポイントで測定したときの測定値のバラつき量のことです。しかし、レーザ変位計は対象物の表面粗さや反射率の影響で誤差が発生するため(詳細や対策については、後述)、まったく同じポイントを同じ条件で測定することは現実的とはいえません。
なお、対象物の表面状態によってどれだけの誤差が発生するかは、レンズなどの光学設計や測定アルゴリズムに依存し(実力値が異なり)、レーザ変位計の性能に伴う価格差やレンズの大さによるヘッドサイズの違いなどに現れます。
治具の見直しやフィルターでの微振動対策
繰り返し精度が改善しても、測定値のバラつきが残る場合、取付治具の振動が原因になっている可能性があります。変位計の測定方向が水平ではない場合、人が出入りする場所では必ず鉛直方向に微振動が発生しています。その微振動によって測定値に0.1μm~数μmのバラつきが生じていることが考えられ、次のような対策が有効です。
- ローパスフィルタ機能を使用する(または、ローパスフィルタ搭載の変位計を使用する)
- センサとワークを一体化した治具で固定する。
直線性の改善による対策
ガラスや鏡面など、入射角と反射角が同じになるワークの場合、正反射によるエラーを回避するためにセンサヘッドを傾けます。その際、設置角度のズレによる直線性の悪化を抑えることで、測定誤差を是正できる場合があります。
突き出しピンに押し当てながらセンサヘッドをネジ固定するなど、設置に十分な配慮が必要です。また使用するレンジを極力狭くし、その範囲内でマスタワーク(基準とするワーク)を使ってスパン補正することで、直線性を改善することも可能です。
ただし、測定器自体が持つ直線性は、光学系に依存する割合が高いため、たとえば、移動平均などのフィルタをかけるといった対策をしても効果がありません。正反射設置での直線性がスペックに明示されていないセンサヘッドの場合、直線性は予想以上に悪くなる可能性があるため注意が必要です。
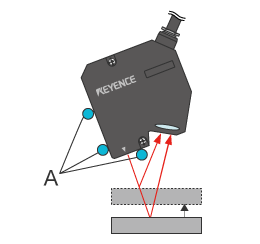
- A
- 突き出しピン
定期的な校正(キャリブレーション)の実施
定期的な校正(キャリブレーション)は、測定器の精度維持に欠かせません。適切な間隔で校正・メンテナンスを行うことで、測定誤差の根本原因を断つことができます。校正間隔に関しては測定器の構造や部品の消耗・劣化の早さなどによって異なるため、通常、測定器メーカーが奨励する校正間隔があり、それに準じることが重要です。過酷な環境下で使用していたり、強い衝撃が加わったりしたことにより、測定誤差が改善されない場合はメンテナンスや修理の必要性も考えられます。そのような場合は、校正時期にかかわらずメーカーに相談することをおすすめします。
測定者に依存した測定誤差の解消方法
オフラインでノギスやマイクロメータなどの測定器を使用する場合、測定箇所が測定者によってバラついたり、経験や技量の差によっても測定結果に誤差が生じたりしてしまいます。教育や訓練を徹底し、可能な限りバラつきを抑える努力が求められますが、測定値を完全に定量化することは不可能です。また、対象物の小さなバリや欠け、ゴミの付着に接触して測定すると測定値に誤差が生じるため、測定箇所の状態を念入りに目視確認する必要があります。さらに、リアルタイムに測定値をデータで把握することができないため、検査と製造を並行している場合、歩留まり率が低下したり、いつ頃から不合格品が発生し始めたかを統計データから判断したりできません。
また、投影機や測定顕微鏡、CNC画像測定機、三次元測定機などの測定機器では、測定者による誤差に加え、専門的な知識を要します。測定業務の属人化といった課題を解決するには、教育・訓練を徹底し、長期的に測定者を育成する必要があります。
オフライン測定での測定誤差を解消する測定器
キーエンスでは、これらの課題を解決するため、ステージに対象物を置いてボタンを押すだけで、複数の対象物の複数箇所を一括で高精度に測定できる画像寸法測定器を開発しました。ワークの位置や向きを自動補正するため、位置決めや向き合わせ、さらに原点出しなどの作業が不要です。
測定者の経験や技術、知識を問わず、短時間でより多くの対象物をバラつきなく定量的に測定することができます。測定結果はすべてデータ化されるため、ネットワークを通じて遠隔からすぐに検査結果を把握したり、データ分析の作業を効率化したりすることが可能です。
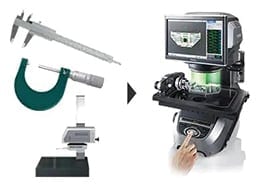
環境条件や対象物に依存した測定誤差の解消方法
電源を入れてからの時間や周囲温度と変位計の温度特性の関係、対象物の材質によって生じる測定誤差の原因と解消方法について説明します。
温度変化とドリフトによる誤差の把握
各部の温度によるドリフトを把握することで、測定誤差を解消することができます。測定システム全体のドリフトには、変位計単体のドリフト成分・治具単体のドリフト成分に分けることができます。そのなかでも、変位計単体のドリフト成分には、初期ドリフト・温度ドリフト・経時変化があります。ここではスペックから算出しやすい変位計単体のドリフトとそれにより生じる誤差の把握方法を解説します。
- 初期ドリフト
- 電源を入れてから変位計の内部温度が安定するまでに測定値が変化する成分のことです。通常、入電後30分から1時間経つと、内部温度と測定値が安定します。
- 温度ドリフト
-
使用環境の周囲温度が変化した際に、測定値が変化する量のことです。スペック上では、温度特性として「〇〇% of F.S./℃」と表記されます。
たとえば、測定レンジが±5mm(つまり10mmの範囲)で、温度特性が「0.01% of F.S./℃」の場合、
周囲温度が10℃変化したときの温度ドリフトは、下記の式で求めることができます。0.01%(温度特性)×10mm(測定レンジ)×10℃(周囲温度)=10μm(温度ドリフト)
これにより、周囲温度が10℃変化すると、変位計の温度ドリフトで10μmの測定誤差が生じることがわかります。
センサヘッドからコントローラにアナログ信号で伝送している場合、コントローラの温度ドリフトも考慮し、コントローラの温度特性スペックをもとに同様の計算をします。現在の変位計の主流であるデジタル信号での伝送の場合は、上記の式で問題ありません。
また、センサヘッドの筐体内温度がどれくらい上昇するのかがわかれば、初期ドリフトの目安を温度ドリフトをもとに計算し、電源を入れてからすぐに使用してもそれを考慮して測定することができます。その求め方は下記の通りとなります。
内部温度上昇(T℃)×温度特性(〇〇% of F.S./℃)×測定レンジ(mm)
- 経時変化
-
変位計単体の経時変化は、光学系を固定している接着剤がわずかな温度変化で膨張・収縮することなどが原因で生じます。経時変化もセンサヘッドによって温度特性が異なり、ドリフト方向にも個体差があります。一般的に、変位計の温度特性が小さければ小さいほど、しっかりした構造を持ち、経時変化も小さいといわれています。
他にも治具や固定ネジにもドリフトが生じます。高い精度が求められる場合は、治具の材質の膨張係数や膨張方向、さらには固定ネジの残留応力などからもドリフトによる誤差を計算することはできますが、要素が複雑になればなるほど、実際に生じる測定誤差算出の難易度は高くなります。
対象物の表面状態による誤差・バラつきへの対策
高精度なレーザ変位計であっても対象物の表面状態の影響を受ける場合があります。それは、ワークへの依存性が高いためです。これは、測定誤差発生の原因として最も多いケースですが、スペックやカタログを見るだけでは、どの程度バラつくかはわかりません。
対象物の表面状態の影響による誤差要因は、色シフト成分・表面の凹凸の影響による誤差成分・表面の反射率の変化の3つに分類することができます。
これらの中でも代表的な誤差の発生要因である、対象物表面の凹凸の影響への対策・解消方法について解説します。表面の凹凸度合いによる影響を抑えるには、下記の3つの対策が考えられます。
- できる限り、対象物の凹凸を少なくする
- もし研磨など表面処理の工程があれば、その前ではなく後で測定したり、表面が滑らかな面があればそちら側を測定したりすることで誤差を解消できる場合があります。また、可能であれば表面を研磨して凹凸を抑えたり、セラミックを貼り付けたりすることも有効ですが、測定のためだけに工程を増やすことは現実的ではありません。
- フィルタ処理を使用する
-
移動平均やローパスフィルタ、メディアンフィルタを用いて測定データのバラつきを抑えます。対象物が動いている場合は、移動平均のフィルタ処理を使用することで、表面状態による影響を抑えることができます。
たとえば、高さ1mm程度で凹凸を持つワークを搬送中に測定し、測定値がバラついたとします。ワークの移動中に複数回測定した平均値を算出する移動平均のフィルタで処理することにより、測定値を安定させることができます。ただし、フィルタをかけすぎると本来の波形がわからなくなるため、フィルタの設定には注意が必要です。例:コピーブレードのうねり測定 移動平均のフィルタ処理なし 移動平均をかけることでデータが安定 また、表面状態が場所によって異なる金属ヘアラインのような対象物を測定する場合、場所によってレーザの当たり方が異なるため、対象物を動かして表面状態の異なる複数箇所の測定値を平均することにより、測定値のバラつきを抑えることができます。
- 投光するレーザー光や受光素子をワイド化する
-
小スポットのレーザー光よりもワイドなスポット光を投光することで、凹凸による値のバラつきを抑えることができます。投光レンズに特殊形状のシンドリカルレンズを搭載した変位計を使用することで、横幅のみが広いライン状のレーザースポットを投光することができます。
また、ワイド化した受光素子(CMOSやCCD)を採用することでワイド化した反射光全域をそのまま受光できるため、散乱光による受光位置のバラつきを吸収することができます。
広範囲の微細な凹凸形状を高精度に測定する必要がある場合は、帯状のスリットレーザーを採用した高精細なレーザ変位計を使用することで、2次元プロファイルデータや3次元形状を数値飛びなく高速かつ正確に測定することが可能です。
例:基板のスクリーン印刷厚み測定 2次元プロファイルデータ 3次元画像処理
他にも測定誤差の原因や解消方法について3冊の技術資料でより詳しく解説しています。ぜひ下のボタンからダウンロードしてご覧ください。