検査の課題と解決
検査は、製造した部品や製品の品質が規定値に適合しているかを評価し、品質を担保する重要な工程です。なかでも外観・寸法・形状の検査は、OK/NG判別のみによる不良品流出防止だけでなく、欠陥・不良の情報・状態の詳細情報を得ることで、原因の特定や再発防止などに役立てることができます。
また、複数の部品から成る製品の場合、組立工程で全数検査することにより不良品流出を未然に防ぐことができます。たとえば、接着や溶接の状態、電子部品のプロセス品質、電子基板の実装状態などは、後工程や完成品の品質・性能に大きく影響します。
検査の実施方法と課題
検査の実施方法は、下記の2つに大別されます。
抜き取り検査
検査対象とするロットから複数の試料を抜き取って検査を行い、その結果からロットの合否を判定します。
- 抜き取り検査の課題
- 検査にかかる手間・時間・コストを削減できる反面、抜き取った試料が良品であっても、ロット内に不良品が混在する可能性があります。同時に、ロットの大多数が良品だったとしても、試料が不良品だったためにロットごとNGとなり、ロスが生じてしまう可能性もあります。
全数検査
製造したすべての製品または部品などを検査します。不良品の流出を阻止でき、ロット内のすべての部品・製品の品質を担保できることが最大のメリットです。
- 全数検査の課題
- 全数検査は理想的である反面、検査手法や対象物の数によっては、検査時間・コストが、タクトタイム・製品単価と合わなくなるケースが多数あります。また、従来の検査装置では、要求される検査項目への対応力や精度・スピード・安定性が得られず、全数検査の自動化と低コスト化が進まないケースは少なくありません。
正確で安定した自動全数検査の実現
- 事例を探す
各種検査手法と課題
現在、FAではAOIやAVI装置、近赤外線カメラなどさまざまな手法が検査に用いられています。ここでは、製造現場で用いられている代表的な非破壊検査手法と、検査における諸課題について解説します。
官能検査(目視検査など)
人の五感による官能検査のなかでも代表的なのが、検査員が目で見て行う「目視検査」です。他に感触や味覚、聴覚・嗅覚を使って製品をテストします。多くの場合、特別な設備・装置などの導入費用がかかりません。
- 課題
- 検査員の人数・検査工数に比例して人件費が増加。量産品の全数検査には膨大なコストがかかる。
- 検査人員の確保と教育が必要で、経験・習熟度が問われる。
- 検査員によって検査結果にバラつきが生じる。
- 検査対象物に限界がある。たとえば精密な部品の極小箇所などの検査は困難。
- 熟練者であってもヒューマンエラーが生じる場合があり、完全なポカヨケが困難。
X線検査
対象物に当てたX線の透過経路での吸収量の違いから、内部欠陥や食品などの異物混入の検査などに広く用いられています。FAにおいては、AXI装置などの専用の一体型検査装置が代表的です。
- 課題
- 法令に則った設置・届け出、管理・運用が必要。一般的に資格保持者(X線作業主任者など)と管理区域が要求される。
- 対象物によっては撮像時間がかかるため、全数検査への対応が困難。
- 組立または封止後の不良発見では、歩留まりが低下してしまう。
- 1方向からを2次元撮像する場合、立体物は多方向からの撮像が必要となり、より時間がかかる。
- 電子デバイスなどの微細な剥離やクラックなどは検出が難しい。
赤外線検査
赤外線とは可視光線とマイクロ波の間の不可視光で、波長によって近・中・遠赤外線に分類されます。対象物の表面または裏面から赤外線を照射し、表面からの輻射光を赤外線カメラで検出して画像処理・判定します。赤外線量の変化により内部のクラックや表面の傷を検出することができます。他に光線照射せず熱作用を近赤外線などの帯域で捉えるカメラなど、さまざまな種類があります。
- 課題
- 対象物に赤外線の反射・吸収・透過特性が異なる部分が混在する場合、異常検出が困難。
- 厚みがある対象物、または、厚みが均一でない場合、内部のクラック検出が困難。
- 長時間にわたり光線照射を目にしていると、目の健康を害する恐れがあるため、運用管理と注意が必要。
超音波検査
UT(Ultrasonic Testing)と呼ばれ、可聴範囲を超える高い振動数の弾性振動波(音波)の指向性を利用し、対象物の反射信号(エコー)の有無や強弱を画像化し測定します。対象物表面から内部の空洞(ボイド)や剥離、クラックなどの検査が可能です。
- 課題
- 対象物の厚みによっては検査が困難な場合がある。
- 大気中で検査する場合、伝搬特性が低下するため対象物表面にプローブを接触させる必要があり、対象物が限られる。
- 測定スポットが大きいため、小さな箇所の形状検査が困難。
- 対象物表面の傷や凹凸など外観検査には不向き。
過流探傷検査(過電流探傷検査)
ET(Eddy current Testing)と呼ばれ、渦電流(Eddy Current)の発生状態の変化から金属材料の欠陥などを調べます。コイルに高周波電圧を印加して交流磁界を発生させ、その磁界中に対象物を置くことで渦電流が発生します。材質・欠陥・異種金属・形状変化などで過電流の発生状態が異なり、それを検出用コイルで信号として捉えて解析します。電気信号処理のみで素早い判定が可能なため、製造ラインでの自動探傷試験・検査から原子力分野の配管検査まで広く用いられます。
- 課題
- 対象物が金属に限定される。
- 測定距離が短いため、検査条件が限られる。
接触式検査(接触式変位計)
ノギスやマイクロメータなどの手動測定器具が代表的ですが、インラインでは接触式変位センサの活用が一般的です。接触子を対象物に直接触れさせることで、その変位から高さ・厚み・反りなどを測定します。
- 課題
- 接触子が直接触れるため、やわらかい材質や食品、電子部品などデリケートな製品への使用は困難。
- 測定面が小さいため、大きな対象物の検査には複数のセンサまたは複数回の測定が必要。
- 接触子より小さい溝などは測定不可能。
2次元画像検査(画像センサ・エリアカメラ)
一般的にカメラで対象物を矩形のエリアで撮像し、その画像を用いて検査する手法です。部品の有無判別や輪郭形状によるOK/NG判別など、汎用的に用いられています。
- 課題
- 反射光の量で判別するため、正確な高さ測定ができない。
- 曲面や球面など奥行きがある対象物は、一部にしかピントが合わず測定が困難。
- 凹凸のある金属など、光の反射が不規則な場合、照明条件の対応が困難。
- 画像の濃淡で判別するため、対象物の表面状態により、外観不良を安定して検出できない。
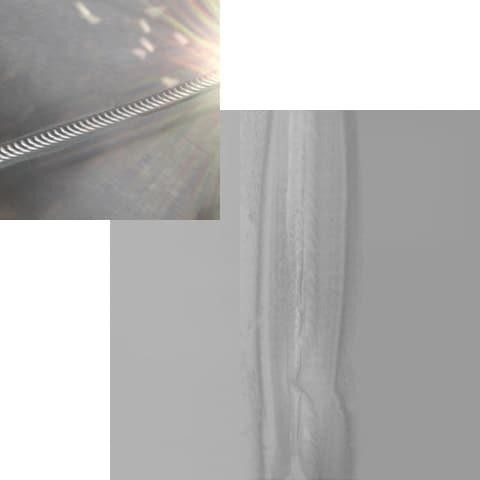
1次元非接触式検査(ポイントレーザ変位計)
従来の1次元レーザ変位計(三角測距方式、共焦点方式など)は、一般的に赤色のポイントレーザを対象物の表面の1点に照射し、反射光との差異からその点の高さを測定します。
- 課題
- 点で測定するため、多点測定するにはステージ移動に時間がかる。
- 奥行きのある対象物の場合、反射光が遮られることで死角ができるため、測定が困難な場合がある。
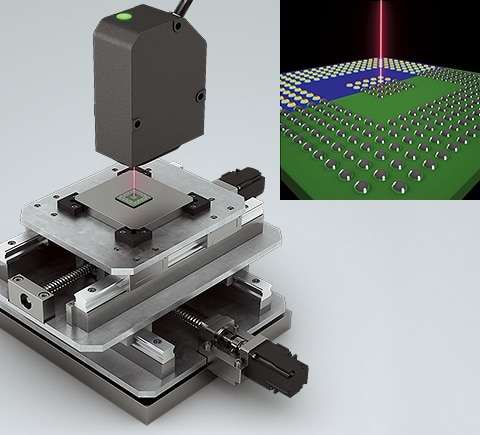
検査の課題解決
これまでのFAにおけるインライン検査は、有無判別やOK/NG判別などを主流とし、高い精度が要求される項目は、オフラインで抜き取り検査を実施するケースが多くみられました。しかし、これらの方法では
- 検査工程・コストの増加
- 不良品流出のリスク
- 不良原因の特定や分析が困難
- 製造とのタイムラグによる歩留まり率低下
などさまざまな課題が伴いました。
近年は、これらの課題を解決する手段として、3次元情報を活用したインライン全数検査が注目されています。
- インライン3次元検査のメリット
- 自動化によるコスト低減
- 全数検査による不良品流出防止
- タクトタイムを落とさず、高さを含む正確な3次元情報を素早く取得
- 対象物の材質・色・光沢・形状の影響を受けず、安定した検査が可能
- 外観・寸法・形状など複数の項目を同時に検査し、工程を合理化
- リアルタイムな検査で、歩留まり率を向上
- 全数の詳細な検査データは、不良再発防止・傾向分析・統計・トレーサビリティ・予知保全などに活用可能
- リアルタイムなデータ取得により、装置のフィードバック制御にも活用可能
インライン3次元検査の実現と導入
新しい技術や測定/計測原理により安定して正確なデータを取得できる、プロファイル測定器や3D変位計、パターンプロジェクション方式を採用した3次元カメラや照明システムをラインに導入します。それらで取得したデータを3次元画像処理することで、タクトタイムに影響せず、さまざまな対象物・条件・検査項目に対応する自動全数検査が可能となります。
詳しくは、業界別の課題解決事例を参照ください。