段取り八分!だからこそ知っておきたい、段取り改善の手順とコツ
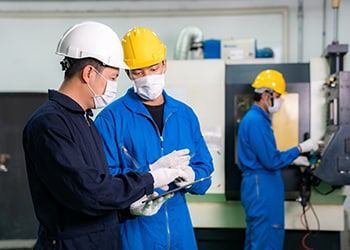
「段取り」は、製造業の現場はもちろん、日常生活や趣味など、あらゆるシーンで馴染みのある言葉です。また、事前の準備・手順が仕事の質の8割を占めるという「段取り八分」は、製造現場の業務において、ほとんどの人が共感できるフレーズでしょう。
昨今の製造業では、多品種少量生産の増加や、製品サイクルの短期化に伴う短納期化要求が高まりました。同時に、タイムリーな製品供給によって不良在庫を抱えるリスクを回避する必要もあります。
こうした傾向を背景に、段取りの効率化や工数削減など「段取り改善」の重要性が増す一方です。そこで今回は、段取りの言葉の意味から、段取りの効率化・工数削減といった改善に役立つ手順やコツなどについて解説・考察していきます。
- この記事でわかること
段取りとは
「段取り」とは、「物事を行う順序や手順。また、その準備」といった意味を持つ言葉です。
段取りの語源には諸説あり、歌舞伎の楽屋用語で、話の区切りや一幕を「段」と呼び、芝居の筋や構成のことを「段取り」と呼んでいた説が代表的です。
また、坂道に石段を設けるとき、勾配から段数を見積もることを「段を取る」と言い、石段の仕上がりを評価するとき「段取りが良い・悪い」と表現したことに由来するという説もあります。いずれも、現代のものづくりの仕事における段取りに通じる考え方といえます。
製造現場では、製造する製品に合わせて、加工機や冶具・装置などの設置や設定する段取り、それらを変更する段取り替えの作業が発生します。段取り作業では、装置および生産を停止させる必要があるため、直接付加価値を生んでいない非生産的な状態を含みます。そのため、段取りにかかる時間は短ければ短いほど良く、段取り工数の削減は重要なミッションであるといえます。
段取りが不十分な場合、生産開始後に不具合や不良品が発生してしまい、本末転倒となるため、無作為に作業手順を省略することもできません。段取り改善は簡単に進めることができるものではないため、順を追って改善内容を検討し、実行していく必要があります。
製造現場での段取り改善の手順
段取りという言葉の意味に、「順序や手順」という語が含まれていました。段取り改善を一挙に行うことは難しく、以下のような順序・手順に沿ってムダを減らし、改善を進めていく必要があります。
段取り作業を内段取りと外段取りに分類
まず段取りを大きく「内段取り」と「外段取り」の2つに分類します。
- 内段取り
- 内段取りとは、機械や作業をいったん停止させてから、作業しなければならない段取り作業のことです。
- 外段取り
- 外段取りとは、機械を動かしながら、または作業者が作業しながら、ライン・工程の外で行うことができる段取り作業のことです。
段取り作業を内段取り・外段取りにわけて整理し、次にそれぞれの改善項目を検討します。
内段取り・外段取りそれぞれの改善項目を挙げる
まずは、内段取り・外段取りそれぞれの改善すべき項目をさまざまな角度からリストアップし、具体的な改善策を探っていきます。その例を以下に挙げます。
- 内段取りの改善案の例
-
- 治具を工夫することはできないか
- 複数人による並行作業で時間短縮できないか
- 調整や設定作業の属人化を減らし、誰でもできるよう標準化できないか
- 作業の教育・訓練を標準化できないか、または作業を簡易化できないか
- 外段取りの改善案
-
- 作業姿勢や環境の改善策を検討しムダを減らすことができないか
- 作業手順の見直しで作業時間のバラつきを低減できないか
- 他に外段取りで済ませられる作業はないか
内段取りを外段取り化する
前述の改善例の最後にもあるように、内段取り(装置稼働や作業を停止して行う段取り)と外段取り(装置稼働や作業を止めずに行う段取り)の相互改善も重要な課題となります。
できるだけ外段取りで作業を済ますことにより、内段取りの時間(=生産停止時間)を減らすことができます。簡単なことではありませんが、新しい方法やテクノロジーを駆使するなどして、外段取り化を積み重ねていくことが重要です。
具体的には下記のような例が挙げられます。
- テスト・調整の外段取り化
- 生産ラインと同条件のテスト環境を持つことは難しいかもしれません。しかし近年は、各種シミュレーションソフトウェアの精度が向上しているため、それらを用いて確度を向上し、内段取りでのテスト時間を大幅に短縮できることがあります。
- 装置設定の外段取り化
- 過去に取り扱ったことのある工程であれば、設定を保存・再現できる装置の導入・活用は効果的です。品種が増えるほど設定データの資産が増えていくため、長期的にみても費用対効果が高い投資といえます。
- 設定・設置作業のそのものの廃止
- 極端に聞こえるかもしれませんが、内段取りからも外段取りからも廃止できる作業は実際に存在します。最新の装置は設定の自動化が進んでいるため、従来と劇的に異なるワークや工程でない限り、段取り替え時にほとんどそのままの状態で問題ない場合があります。特にライン上に多数あるセンサの配線や設定などの作業、検査に使う測定機器のキャリブレーション作業などを排除するだけでも、大幅な時間短縮が可能です。
もう行き詰らない。段取り改善のコツ
これまで段取りに関する改善を検討する機会が幾度もあり、もう改善の余地がないという気分になることは珍しいことではありません。そこで、改善のアイディア出しに行き詰らないための思考法の活用や、改善に役立つ情報収集などのコツをいくつか紹介します。
改善点の洗い出しに行き詰ったら
過去に何度も類似する事案の段取り改善に挑戦していると、内段取り・外段取りの改善項目を挙げること自体が困難になる場合も少なくありません。そこで活用したいのが、製造現場の改善に役立つさまざまな思考法です。それぞれの詳細については、このサイトでも詳しく紹介していますので、ぜひ参考にしてみてください。
- ・「ECRSの4原則」引き算の改善法
- 業務のムダを減らし、時短するという目的においては、改善の方向性を見出すうえで比較的採り入れやすいといえます。
- ・「オズボーンのチェックリスト」思考を整理して効率的に発想
- チェックリスト法を活用することで、内段取り・外段取りそれぞれの改善点を効率的に列挙していくことができます。
- ・「MECE」ロジカルシンキングで漏れ・重複なく洗い出し
- 複雑な段取りの改善では、意図せず漏れや重複が起こりがちです。検討すべき項目を洗い出すためのロジカルな思考法「MECE」は、改善の余地や優先順位を見つけるために有効です。
最新の機器・素材などの情報を収集する
内段取りの外段取り化の例でも挙げた通り、製造現場のハード・ソフトはデジタル技術の発展と現場のニーズに沿って、常に進化し続けています。また、加工効率や装置の省メンテナンス性を向上させた新素材なども同様です。このような新しい機器・素材の導入は、段取り工数削減において大きな費用対効果をもたらすケースが少なくありません。
多くの業界向けメディアは大きな動向を掴むことに役立ちますが、自分の現場に直接関係する最新技術や素材などの情報は、自ら進んで探しにいかなければならないことがほとんどです。日頃から最新情報を収集しておくことで、これまでの段取り作業の当たり前を覆し、努力だけでは成しえなかった段取り工数の削減が実現します。
- 関連ページ