ロボットハンド、ロボットアームの選定方法・選定基準
産業用ロボットの導入では、ロボットアームのほか、ロボットハンド、架台、安全柵、ベルトコンベア、ストッカーなどの周辺機器・設備も重要です。
中でもロボットアームは作業の精度や速度に大きく影響します。また、ロボットハンドは、工程に合わせて都度製作する必要があり、適切な形状・仕様でないと生産の効率化が図れないばかりか、作業ができず、作り直しになる可能性もあります。
そこで産業用ロボット導入のファーストステップとなる、ロボットアームとロボットハンドの選定方法・選定基準の基礎知識を紹介します。
ロボットアーム(マニピュレータ)、ロボットハンド(エンドエフェクタ)とは
「ロボットアーム」「ロボットハンド」とは、人間の手や腕のような働きをする機械的な手や腕の一種で、動作は通常、プログラムで制御します。
ロボットアームは、装置全体を指す場合や、大きくて複雑なロボットの一部を指す場合があります。回転や動力を伝達する接続部はジョイントで繋がれており、これを「軸」といいます。
一方、ロボットハンドはロボットアームの先端に取り付けられ、人間の手のような働きをし、掴む・回すなどのハンドリング作業を行います。ロボットハンドの機能は、指の本数やジョイント数の設計によって決まります。多指ハンドといわれるロボットハンドでは、握りや操りなど、対象物体の自在なハンドリングが可能です。
ロボットアーム(マニピュレータ)の動きと軸数
人間の腕に代わって働くロボットアームの動きは、軸の数(軸数)と軸の動きによって決まります。また、軸をまったく使わないロボットアームもあります。
ロボットアーム
ロボットアームの軸には、以下の機能があります。
- L軸
- 全体を前後に動かす。
- S軸
- 全体を回転させる。
- U軸
- 腕を上下に動かす。
- R軸
- 腕を回転させる。
- T軸
- 手首を回転させる。
- B軸
- 手首を上下に振る。
- 例:垂直多関節ロボット(6軸)
- A
- ロボットハンド
- B
- ロボットアーム
- C
- 軸
垂直多関節ロボットのアーム
産業用ロボットでは6軸機構が主流です。ロボットハンドやリンクはサーボモーターで回転する軸で直列に繋がっており、このアームの構造から、垂直多関節ロボットは「シリアルリンクロボット」ともいわれます。
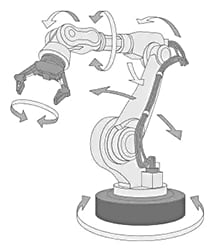
スカラロボットのアーム
軸とリンクはすべてXY(水平)方向に動作します。このアームの構造からスカラロボットは、「水平多関節ロボット」ともいわれます。先端部はZ(上下)方向に動き、ワークに対して作業をします。上下方向の剛性が高く、水平方向にはしなやかな動きが可能です。
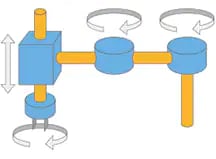
パラレルリンクロボットのアーム
リンクと軸で構成するアームを並列に複数配置した構造になっています。リンクと軸の組み合わせにより、多様な動作が可能です。また、並列なリンクを介して複数のサーボモーターの出力を1点に集中することができます。

直交ロボットのロボットアーム
直交するスライド軸を組み合わせたロボットアームです。リンクがスライド軸上を動くことから、このアームを備えたロボットは「ガントリーロボット」ともいわれます。

ロボットハンド(エンドエフェクタ)の機能
人間の手に代わって働くロボットハンドには、人の手の構造や大きさを模倣した指または爪で対象物をクランプしたりチャックして掴むもの、へら状のもの、真空吸着や磁石で吸着するものがあります。また、電動ドライバーや切削機などの工具をしっかりと握るなど強力な力を発揮する一方で、傷付きやすい物を傷付けずに掴むといったこともできます。
通常、ロボットハンドは対象物の重さや形状、硬さや材質などに合わせて専用に設計します。そして、指や爪は電動・空気圧・油圧・機械的動作を応用した力で動作します。
指や爪で対象物を挟んで掴むロボットハンドは、「把持ハンド」といわれます。2本指掴みや3本指掴みがあり、大きい対象物を掴んだり抱えたりする4本以上の爪や指があるタイプもあります。また、対象物を吸着するロボットハンドは「吸着ハンド」といわれます。吸着には真空吸着や磁石が使われます。
- 例:2本掴み把持ハンド
- A
- ロボットハンド駆動台
- B
- サーボモーター
- C
- 指または爪
- 例:6点式吸着ハンド
- A
- ロボットハンド駆動台
- B
- 吸着部
ロボットアーム(マニピュレータ)、ロボットハンド(エンドエフェクタ)の性能とは
産業用ロボットは工場の規模の大小や生産数の過多にかかわらず、さまざまな製造現場において容易に自動化を実現します。しかし、ロボット導入による製造効率の向上は、ロボットの性能に左右されます。中でも、対象物にアクセスするロボットハンドとロボットアームの性能はロボットの導入効果に大きな影響を与えます。ここではロボットハンド・ロボットアームの性能に影響する重要な要素を説明します。

精度と剛性
ロボットの精度には、「繰り返し位置決め精度」と「絶対位置決め精度」があります。この2つの精度は、ロボットハンド、ロボットアームの「軌跡精度」「絶対精度」「剛性」で決まります。
- 軌跡精度
- ロボットが動作する軌跡の精度です。
- 絶対精度
- ロボットの移動量とプログラムでの指示が一致する精度です。絶対精度が低いとプログラムどおりの動作になりません。
- 剛性
- 対象物の重量や反発力など、ロボットに外部からの働く力に耐える強さです。
周辺機器との関係
ロボットハンド、ロボットアームは、位置決め装置・整列器、カメラなど多くの周辺機器の中で動作します。たとえば、パーツの供給装置やコンベア・パレタイザといった装置などとの関係を考慮する必要があります。さらに、近年普及しつつある協働ロボットでは、人に対する安全性や作業性といった親和性が求められています。
処理量
ロボットハンド、ロボットアームは、タクトタイムを短縮し、処理量を増やすための設備です。このため、ロボットによる処理量は、前後の工程の処理量に対して適切である必要があります。
安全性
作業の効率化に貢献してくれるロボットハンド、ロボットアームですが、安全への配慮を怠ると、大きな事故を引き起こすリスクがあります。作業員が作業スペースに入ると同時にロボットの動作を減速または停止させるための、セーフティーライトカーテンやセーフティースキャナの導入が可能かも検討すべきポイントです。
信頼性
ロボットハンド、ロボットアームの信頼性とは、当初の機能を長期間にわたって安定して維持し続ける性能のことです。特にロボットハンドやロボットアームは常に動作し大きな負荷がかかっているため、部品の劣化や消耗が激しく、こまめなメンテナンスが必要です。ロボットには一般に、以下のようなメンテナンスが必要です。
- 日常点検
- 生産開始前や生産終了時に、ロボットハンドやロボットアームの軸部分にガタや異音が発生していないかなどを耳や目で確認します。
- 定期点検
- 1年ごと、または所定時間稼動時といった定期的なロボット内部の点検です。点検結果を基に、異常が認められた部品は直ちに交換します。
- 予防的部品交換
- 寿命がわかっている部品は、長期生産停止期間や操業が停止しているときに交換します。
以上から、これらのメンテナンスを確実に実施し、緊急の事態にも対応できるサポート体制が整ったロボットメーカーを選定することが重要であるといえます。
ロボットアーム(マニピュレータ)の選定基準
こちらでは、ロボットアームを選定する際に抑えておきたい5つのポイントをわかりやすく解説します。
1:自由度(可動範囲)
人間の関節にあたる軸数です。軸数が多いほど自由度が高く(可動範囲が広く)、複雑な作業が可能で、3次元空間の作業に適しています。そのため生産現場では、自由度の高い垂直多関節ロボットが主流になっています。
一方、直交ロボットは軸数が2から4と自由度が低く単純な動作しかできません。しかし、動作速度が速く精度が高い割に安価というメリットがあり、垂直多関節ロボットを補佐する作業に用いられることがあります。
- 選定のポイント:
- ロボットアームを選定する際は、単純な組み立て工程を自由度の低い軸数が少ないロボットが行い、アクセスが難しい奥まった場所での作業は自由度が高い垂直多関節ロボットが行うなど、それぞれの特徴を活かしたシステム構成が必要です。
2:可搬重量(ペイロード)
ロボットアームが持ち上げることのできる最大重量です。メーカーが可搬重量(ペイロード)を設定しているので、運搬するワークの重量を考慮して選択します。
可搬重量は、ロボットアームの軸数やリンクの接続の方式と密接な関係があります。たとえば、垂直多関節ロボットや水平多関節ロボットは、モーターの先にモーターが繋がった構造であるため、根元の軸に近いほど大型のモーターが必要です。このため、ロボット本体のサイズや重量の割に可搬重量が小さくなります。
一方、パラレルリンクロボットは根元にある複数のモーターでロボットの先端だけを動作させるため、ロボット本体のサイズや重量に対して可搬重量が大きく、高速での動作が可能です。
- 選定のポイント:
- ロボットアームはロボット全体の重量バランスを考慮し、運搬する対象物の重量に合わせて選択することが重要です。
3:駆動方式
油圧、空圧、電動、手動などのロボットアームの駆動方式です。駆動方式により、マニピュレーターの速度や強度、精度などが決まります。
最も一般的な駆動方式は電気です。電気による駆動は、制御がしやすく高速の動作に向いており、装置をコンパクトにできるというメリットがあります。
油圧駆動は大きな力を出しやすく、外部からの衝撃に強いため、重量物の運搬するロボットなどに使われています。空気圧駆動は電気駆動に比べて高精度な位置決めなどの精度は劣りますが、空気の圧縮性を利用した柔らかな力の制御が可能です。また、油圧ほどではありませんが大きな力が出しやすいというメリットもあります。
- 選定のポイント:
- 対象物の重量、動作の速度・精度を考慮し選定します。また、駆動装置の大きさも大切な検討要素です。
4:速度
ロボットアームの作業速度で、速い方がタイムラグなく作業できます。生産ラインの速度に合わせて選定することが大切です。
これは、ロボットの動作が必要以上に速いと、前後の工程で待ち時間が増えたりムダな在庫が発生し、処理量増加の効果が相殺されてしまうためです。
また、安全柵を設けないロボットや協働ロボットでは人への安全対策が必要です。
これらのロボットの動作速度には規定された制限があり、ロボットハンドが対象物に触れる点の中心であるTCP(ツール・センター・ポイント)速度は250mm/s以下とされています。どうしてもロボットを高速で作業させたい場合はロボットを安全柵で囲んで人が立ち入らないような安全対策が必要です。
- 選定のポイント:
- ロボット動作速度は、人を含めた製造ライン全体の流れや生産計画に対し適切であることが大切です。また、作業速度を検討するときには、同時に安全対策にも配慮する必要があります。
5:精度
ロボットアームの精度を判断する指標として「繰り返し位置決め精度」と「絶対位置決め精度」があります。産業ロボットを用いた生産では、同じ動作を繰り返して行うので精度が重要です。
一般に、関節数と精度は反比例する傾向にあり、関節数が多くても剛性やサーボモーターの品質を上げると、精度も上げることができます。しかし、ここで問題になるのがロボットの価格で、高い精度を備えた多関節ロボットは、一般的に高価です。
このように、相反する条件の解消策としては、「センサーフィードバック」という技術が注目されています。センサーフィードバックはロボットハンドの先端に画像センサーを取り付け、画像センサーからの位置情報を基に相手座標系を基準としロボットアームやロボットハンドを制御します。このため、高性能なロボットに交換することに比べ、低コストで確実に精度不足を補うことができるというメリットがあります。
- 選定のポイント:
- 高精度な多関節ロボットは価格が高くなる傾向にあります。このようなロボットの導入が困難である場合は、高い精度と剛性を低コストで実現できる「センサーフィードバック」技術を利用したシステムの導入が有効です。
ロボットハンド(エンドエフェクタ)の種類と選定基準

ロボットアームやロボットハンドには、さまざまな種類がありますが、ここでは製品・部品を運搬するロボットハンドの種類と選定基準を紹介します。
ロボットハンド(エンドエフェクタ)の種類
ロボットハンドは、ワークに対して直接触れる部分です。したがって、ワークの数だけ種類があるといっても過言ではありません。ここでは、その中から最も一般的なタイプのものを紹介します。
把持ハンド
人間の手のような指・爪をエアシリンダーやモーターで駆動し、対象物を掴むロボットハンドです。2本指や3本指、4本指など、掴む対象物に合わせたタイプがあります。比較的軽いものや小さいものは2本指タイプでも対応可能ですが、大きなものや複雑な形状のもの、把持したときに安定感が必要な場合は指の本数が多いタイプを選定します。
4本指や3本指タイプは、強力な握力で工具を把持する一方、柔らかい物を傷つけずに掴むこともできます。このため溶接・切削業界はもちろん、食品・医療機器業界でのデリケートなハンドリングが要求されるシーンでも使用されます。一方、2本指タイプの動作は単純ですが、シンプルな構造で小型・軽量化が可能であるため、小さな部品を掴んだり狭い場所での作業に用いられます。
さらに近年では袋の中に粉体などを詰めて真空発生器などで袋の中の空気を抜くと固く締まる「ジャミング効果」を利用し、さまざまな形状の対象物の把持が可能な把持ハンドも開発されています。このような把持ハンドは「ユニバーサルグリッパ」といわれ、多くの研究者が開発・研究を続けており、一部は製品化されています。
- 例:3本指タイプ把持ハンド
吸着ハンド
エアを利用し、真空パッドで吸着させてワークを移動させるロボットハンドです。真空を用いて吸着させるタイプのほか、磁力によって吸着させるタイプもあります。磁力を利用した吸着ハンドは、材質によっては運搬できないので注意が必要です。
真空パッドによる吸着では、真空発生器で真空を発生させ、真空パッドに対象物を吸着させて運びます。対象物の表面に穴が開いていたり、多孔質の表面でなければ、材質を問わず吸着できます。一方、 磁力による吸着は、主に電磁石の入/切で物体を吸着させます。電磁石の入/切は電流で行い、鉄系の素材(鉄やニッケルコバルト)を吸着することができます。しかし、非鉄金属(アルミや銅)は吸着することができません。また、ステンレスはフェライト系やマルテンサイト系は吸着できますが、オーステナイト系は吸着できません。
- 例:吸着ハンド
ロボットハンド(エンドエフェクタ)の選定基準
以下は、一般的なロボットハンドの選定基準です。
ワークに関わる選定基準
- 重量
- 保持できる重量は、ロボットハンドによって異なります。また、重量のほか重心位置も考慮して選定します。
- 形状
- ワークの曲面や凹凸の形状、穴の有無を考慮して、対応可能なロボットハンドを選定します。
- 品種
- 同一ラインで複数の異なるワークを扱う場合には、ロボットハンドの汎用性や互換性も検討材料になります。
- 柔軟性・材質
- ワークの柔らかさや材質によって対応するロボットハンドが異なります。材質によっては、掴んだときに傷が付いてしまったり、吸着跡が残ってしまったりすることもあるので注意が必要です。
環境に関わる選定基準
- 保守性
- 生産効率を考えた場合に忘れてはいけないのが保守性です。エアを使った吸着ハンドは、フィルターの目詰まりやパッドの摩耗が起こります。また、磁力を利用した吸着ハンドも経年劣化で磁力が弱くなります。
- 搬送速度
- 生産ラインに対応可能な搬送速度を有しているかも重要な選定基準です。生産ラインに対してロボットアームやロボットハンドの搬送速度が遅いと、ライン全体の生産能力低下を招きます。
- 箱や安全策などの周辺環境
- ロボットを導入する際によくあるトラブルには、ワークの入った箱へのロボットアームやロボットハンドの衝突や、ワークをしっかりと掴めない、箱の隅にあるワークをピッキングできないなどがあります。同様に安全柵に接触して止まってしまうといった問題も考えられます。そこで周辺環境を考慮して、ロボットアームの可動範囲や大きさ、ロボットハンドの形状を吟味する必要があります。
ロボットアーム(マニピュレータ)、ロボットハンド(エンドエフェクタ)の選定課題
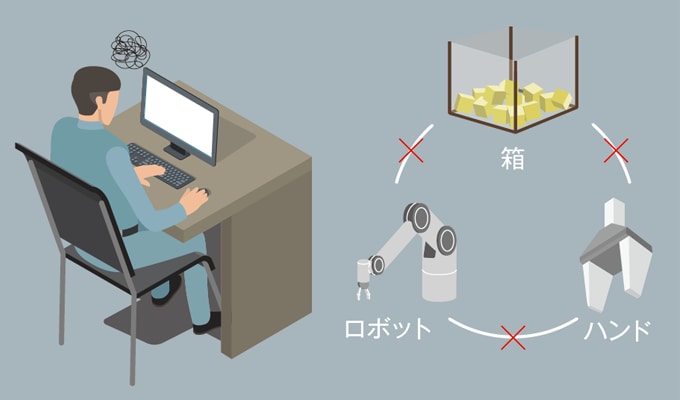
ロボットアームは、汎用品としてメーカーが販売していますが、ロボットハンドはワークや工程に合わせて都度製作する必要があります。そして、形状の最適化や多品種への対応といった判断は、経験豊富な技術者に委ねられていました。
ロボットアームやロボットハンドが決まると、現場のレイアウトを検討し、現物で最終チェックを行います。
その際にワークの位置や傾きによって、周辺設備や箱と干渉したり、無理な姿勢で止まってしまったりと、予期せぬトラブルが発生することがよくあります。そうなるとロボットアームやロボットハンドの選定からやり直すことになり、大きな手戻りになります。また、複雑なロボットの動きを制御するためにプログラミングの手間もかかります。

アームが壁にぶつかる無理な姿勢でとまってしまう etc.
特に近年は、作業に高い精度が求められ、複数のロボットによる協調制御も増え、生産ラインの高度化が進んでいます。さらに短期間での生産ライン構築が求められ、現物合わせのような方法は非効率的です。そこでロボットアームやロボットハンドの選定段階でシミュレーションを行ったり、周辺設備やロボット姿勢を考慮した適切な経路を予測するなど、立ち上げ前の準備が課題になっています。
ロボットアーム(マニピュレータ)、ロボットハンド(エンドエフェクタ)選定の課題解決
ロボットアームとロボットハンドには多くの種類と機能があり、その選定は熟練技術者の知識や経験をもってしても困難です。
キーエンスでは、技術者の経験に頼っていたロボットアームやロボットハンドの選定やプログラミングの課題解決として、3Dロボットビジョンシステムを提案しています。その解決策が「ピッキングシミュレーター」と「経路生成ツール」です。


PC上で現場を想定したシミュレーションが可能
「ピッキングシミュレーター」
ピッキングシミュレーターは、 PC上でロボットアームやロボットハンドの種類、ワークの形状や傾き、周辺設備などを考慮し、現場を想定したシミュレーションが可能なソフトウェアです。シミュレーションを繰り返してから実際にロボットハンドを選定することで、導入後のトラブルを防止し、無駄な手戻りも回避します。技術者の経験に頼っていたロボットアームやロボットハンドの選定も容易になり、シミュレーション段階でハンド形状やレイアウトの最適化を実現します。
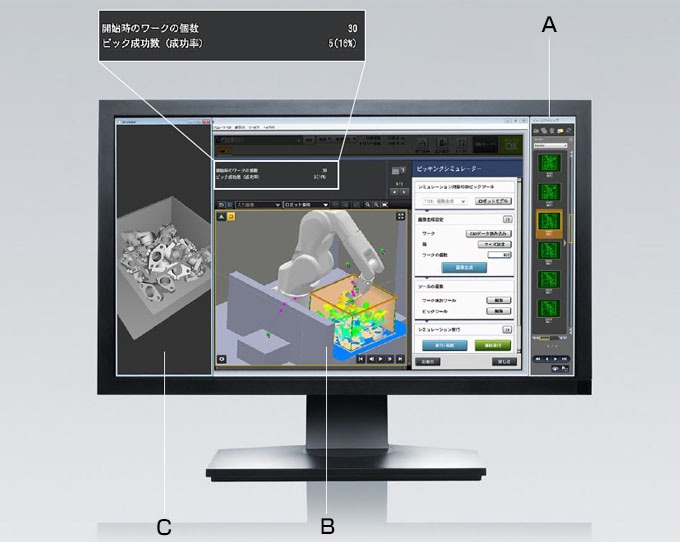
- A
- ワークを1個ピックするたびに、ピッキング後の画像を新たに生成。ピッキングが完了するまでのすべての画像が履歴として残ります。
- B
- ピックごとのロボットの動作経路を確認できます。もしもピック不可だった場合に設定を見直して再計測し、改善できたかの 確認がすぐにできます
- C
- ピックごとのロボットの動作経路を確認できます。もしもピック不可だった場合に設定を見直して再計測し、改善できたかの ワークをピックするたびにバラ積みの変化をシミュレーションし、リアルな荷崩れの状態まで再現します。
最適な動作を自動で算出してプログラム作成の手間を省く
「経路生成ツール」
正確なロボットの動作には、複雑なプログラム作成が必要不可欠でした。しかし、3Dロボットビジョンの経路生成ツールを使えば、周辺設備やロボットの姿勢を考慮し、最適なロボット動作を算出して、安定した稼働を実現します。障害物を回避する軌道を自動算出し、ロボットアームやロボットハンドが干渉しないようにプログラミングを行います。
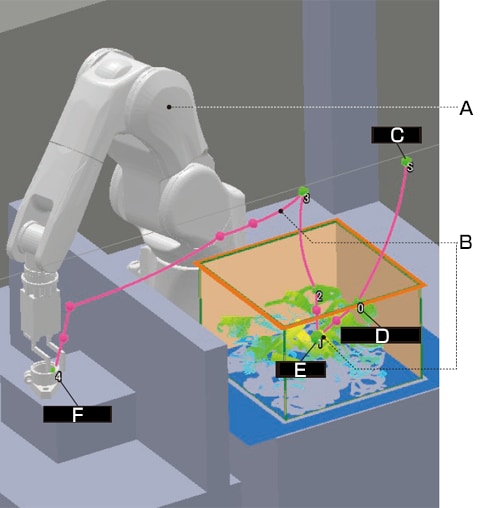
- A
- ロボットの各軸の状態を把握してボットに無理のない動作を算出。動作経路上に特異点があっても安全に通過します。
- B
- アームやハンド、把持中のワークが周辺設備に接触しない把持姿勢などを含んだ 「ロボット動作」を自動算出。
- C
- 開始位置
- D
- アプローチ位置
- E
- 把持位置
- F
- プレース位置
- 経路生成ツール・ピッキングシミュレーターで
確実で無駄のないロボットアーム・ロボットハンドの選定が可能に! - キーエンスの3Dロボットビジョンシステムに搭載された経路生成ツールおよび、ピッキングシミュレーターを活用すれば、ロボットアームやロボットハンドの選定も確実かつ簡単になります。経路生成ツールやピッキングシミュレーターについて詳しくは、以下のダウンロード資料をご覧ください。