物流の機能(保管・荷役)
物流の機能の中でも輸配送とともに中核的な機能となる「保管」と「荷役(にやく)」についてご説明します。保管は一般的な言葉なので理解しやすいですが、荷役は倉庫や物流センターでの積み下ろしから運搬、入出庫管理、仕分け、荷揃えまで多岐にわたるのでイメージしにくいものです。しかし物流コストにおいて大きなウェイトを占める部分なので、しっかりと理解しておきましょう。
保管・荷役とは
「保管」と「荷役」の意味や違い、役割について解説します。
時間的ギャップを埋め、市場に安定供給するために必要な「保管」
保管は、倉庫や物流センターで商品を保管する活動で、生産者と消費者の時間的ギャップを埋めて市場に安定供給することが役割です。また、倉庫や物流センターで品質を保ち、商品の価値を維持することも重要な役割です。例えば鮮魚や野菜、果物などは、冷凍・冷蔵倉庫の誕生によって保管機能が飛躍的に向上しました。保管で重要な物流センターには、「在庫型物流センター(ディストリビューションセンター:DC)」「通過型物流センター(トランスファーセンター:TC)」「流通加工・在庫型センター( プロセスディストリビューションセンター:PDC )」などがあります。
倉庫・物流センターでの荷物の運搬活動全般を指す「荷役(にやく)」
荷役(にやく)は、倉庫や物流センターでの荷物の積み下ろしや運搬、入出庫、ピッキング、仕分けなどの活動全般を表す言葉です。荷役の主な作業は、「荷揃え」「積み付け/棚卸し」「運搬」「保管(棚入れ)」「仕分け」「集荷(ピッキングなど)」の6つに分かれ、それぞれの作業が物流の生産性や品質に大きな影響を及ぼします。また、荷役は、物流の中でも大きなウェイトを占め、荷役のロスは物流コスト増加に直結します。荷役の作業は多岐にわたるので、その中でもよく出てくるキーワードを以下で詳しく解説します。
入荷検品とは
一般的に小売業は、販売する商品を仕入れ、その商品をエンドユーザーに販売します。製造業であれば必要な原材料や部品を仕入れて製品として出荷します。物流も同様に日々多くの荷物を受け取り、検品し、保管し、市場へと出荷しています。
- 荷物が入荷する
- 入荷した荷物を検品(検収)する
- 入庫する
- 保管・流通加工・包装などを行う
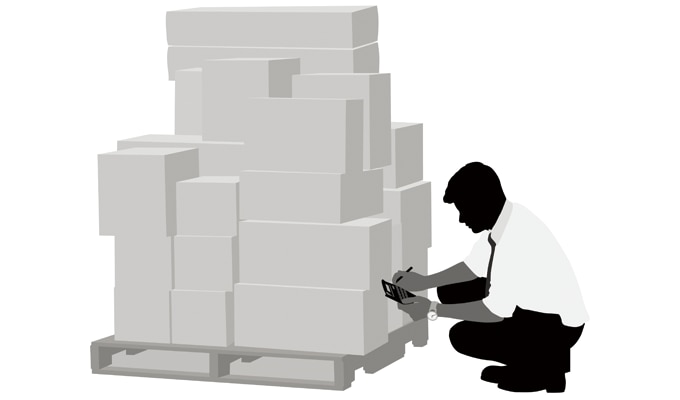
まず、入荷した荷物を入荷予定リストと照らし合わせて商品・数量・品質などを検品します。検品のことを「検収(けんしゅう)」という場合もありますが、入荷した荷物に問題がなければ入庫します。その後、必要に応じて保管・流通加工・包装などを行います。入庫検品のデータ管理は、少量であれば帳簿などの紙に記録しても大丈夫ですが、倉庫や物流センターの場合、受け取る荷物の量が多いため一般的にハンディターミナルなどを使い実施します。入荷時にハンディターミナルを使って検品し、そのデータを元に荷物を保管から出荷まで在庫管理。紙への記録では時間がかかっていたこれらの流れを、的確かつスムーズに行うことが可能になりました。
マテハン(マテリアルハンドリング)とは

マテハンは、荷揃えや積み下ろし、運搬、仕分けなどの荷役作業を効率化する機械の総称です。「マテリアルハンドリング」の略称で、直訳すると機械による作業という意味ですが、わかりやすく言えば荷物の移動を楽にする、または自動化するような機械全般と言えるでしょう。身近なところでは台車やパレット、フォークリフトやコンベア、そのほか省人化や作業のロードタイムを短縮する産業用ロボットや自動倉庫、近年増えている事例としては自動ピッキングマシンやRFIDを利用した商品管理システム、自動搬送や自動仕分けのマシンまでマテハン(マテリアルハンドリング)に含まれます。
棚卸しとは

棚卸しは、すべての在庫数・種類・品質などを確かめる作業です。小さな小売店でも決算前などに行うのでイメージできる方も多いでしょう。残っている商品の在庫数を数え、在庫の金額を確かめることで正確な利益を把握でき、経営判断に役立てることができます。棚卸しは在庫管理や経営を行ううえで非常に重要ですが、すべての荷物を確認する必要があるので倉庫・物流センターのような大規模になれば莫大な労力・時間・コストがかかることが難点です。棚卸し期間中に操業をとりやめる、または部分的に停止する必要もでてきます。しかし、日々の業務で入出庫管理を正確に行えば、そのデータを集計することで棚卸しの負担を大幅に軽減できます。さらにリアルタイムで在庫管理でき、素早い経営判断にも役立つでしょう。
ピッキングとは

ピッキングとは、出荷指示書(ピッキングリスト)に書かれた品番と数量を確認しながら出荷する商品を集める作業です。ピッキングには、発送先ごとに個別に商品を集める「摘み取り方式」と事前に商品を集めておき発送先ごとに仕分けする「種まき式」の2種類があります。
摘み取り方式は、出荷指示書(ピッキングリスト)に書かれた商品を探して出荷するという最も一般的な手法です。「シングルピッキング」「オーダーピッキング」と呼ばれ、多種多様な商品を多くの発送先に送る場合に用いられます。柔軟性が高く、ピッキング後すぐに出荷できるので通販などに適しています。しかし、作業者が倉庫内から商品を探し出す手間と時間がかかります。
種まき方式は、「トータルピッキング」「アソート式」とも呼ばれ、少ない納品先に少ない品種を大量に出荷する場合に最適な方法です。まとめて商品を集めるので作業者の負担は抑えられますが、荷捌きスペースを確保する必要があります。また、仕分け状況の把握が難しく、急な商品追加などに対応しづらいというデメリットもあります。
様々なピッキングシステム
ピッキングシステムについても簡単にご紹介します。もっとも簡単なピッキングの方法は、出荷指示書(ピッキングリスト)を見ながら人間が探すことです。しかし、人為的ミスが発生する可能性も高く、手間と時間がかかるという難点があります。そこで現在では、用途や商品に合わせてさまざまなピッキングシステムが活用されています。
- リストピッキング
- 出荷指示書(ピッキングリスト)を見ながら品名と数量を確認し、商品を探すもっとも基本的なピッキング方法です。簡単に導入できる反面、作業者に正確さやスピードが依存し、人的ミスが発生する可能性も高まります。そこでミスが発生しないように出荷前にバーコード検品などの確認作業が必要になります。
- デジタルピッキングシステム(DPS)
- 荷物や商品が保管されている棚にデジタル表示器を取り付け、表示器の指示に従って商品を集めるピッキング方法です。作業者は指示器を見ながらピッキングするだけなので経験や知識がなくても簡単に作業ができ、人的ミスを最小限に抑えられることがメリットです。どのような保管場所にでも表示器を取り付けられるので導入が手軽な点も魅力でしょう。
- バーコード
- 出荷指示情報をバーコード化し、商品のバーコードを読み取りながらピッキングを行う方法です。対象外の商品を選んだ場合、バーコードスキャナやハンディターミナルからエラー音や振動などで知らせることで取り違いを防止できます。
- RFID
- 無線で情報をやり取りできるRFID(Radio Frequency IDentifier)を商品棚などに取り付けておくことで商品の取り間違えを防止するシステムです。バーコードのように読み取る必要がないことがメリットでスピーディな作業実現に効果的です。
仕分け
ピッキングと同様に出荷作業の中心になるのが「仕分け」です。仕分けは、商品を品種別・出荷先別などに分ける作業です。仕分けの方法は、大きくわけると「手仕分け」と「自動仕分け」の2つです。その違いは人が行うか、機械が行うかということです。自動仕分けは、主にソーターと呼ばれる機械が使われます。また、仕分け場に荷物がどのように持ち込まれるかによって仕分けは大きく3つの型に分類されます。
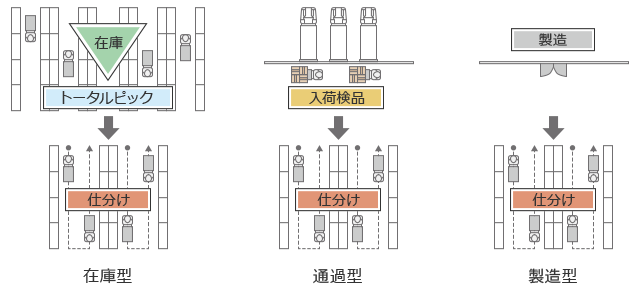
- 在庫型(DC)
- 物流センターに在庫があり、そこからピッキングされた荷物を仕分ける
- DC(ディストリビューションセンター)についてはこちら
- 通過型(TC)
- 物流センターに在庫がなく、入荷した商品を仕分ける
- TC(トランスファーセンター)についてはこちら
- 流通加工・在庫型(PDC)
- 工場で製造された製品がそのまま持ち込まれて仕分けをする
- PDC(プロセスディストリビューションセンター)についてはこちら
出荷検品とは
入荷時と同様、出荷時に内容に誤りがないか検品(検収)を実施します。これを出荷検品といいます。
- 受注内容に合わせて出荷指示書(ピッキングリスト)を作成する
- 出荷指示書(ピッキングリスト)に従い商品をピッキングする
- 流通加工を行う
- 検品(検収)を行う
- 包装を行う
- 出荷する
出荷では、受注内容に合わせて出荷指示書(ピッキングリスト)を作成し、作業者は出荷指示書(ピッキングリスト)に従って商品をピッキングします。ピッキング後は、必要に応じて流通加工を行い、包装前に内容に間違いがないか出荷検品を実施し、包装後に出荷します。ピッキングや出荷検品時も入荷時と同様にデータを記録します。入庫時にバーコードや2次元コードなどを付与し、ハンディターミナルなどで管理すれば入出庫管理・在庫管理を正確に行うことが可能です。