【物流業】
物流業界でのハンディターミナルの活用事例を紹介します。物流業界における各工程での課題、ハンディターミナルを導入するメリットを事例を交えて解説します。
- 物流について
- 物流における課題
- ハンディターミナル導入による課題解決
- 代表的な工程と製造の流れ(倉庫・物流センター)
- 工程別 ハンディターミナル導入によるメリット
- 代表的な「荷物輸送」の流れ
- 文字認識ハンディターミナルで運用改善
- まとめ
物流について
物流とは、その名の通り「物の流れ」です。企業が自社の商品を消費者へ届けるすべての過程、プロセスを含む一連のフローを物流と呼びます。物流には、物流センターや倉庫などの保管場所、大型トラックによる配送、船や航空機などによる輸送、商品を届けるための物流システムなどが含まれます。物流業界の傾向としては、製造業に比べると人手に頼る工程が多く、ピッキングミスや発送間違いなどが起こりやすい傾向にあります。
物流における課題

物流の現場では、IT化が進んだ現代でも検品や在庫管理など多くの作業を人力や目視に頼っているため、人為的なミスや非効率が生じやすいことが特徴です。とくに入出荷時の検品では、リストと商品の照合を目視で行うため、見落としや記入漏れなど発生しやすく、在庫管理にズレが生じやすくなっています。近年は、ネット通販の台頭で取扱荷物数も急激に増えており、倉庫や物流センターの効率化は急務となっています。
生産者と消費者の仲立ちとなり、商品や製品を必要とする人や企業へ、必要なタイミングで届けること──それが倉庫や配送センターなど物流業の大きな役割です。しかし、そのためには、物流の現場が入荷から出荷までの工程や在庫状況を厳密に管理する必要があります。ところが、機械化や自動化が高度に進んだ製造業の現場とは異なり、物流では「入荷」から「出荷」までの各工程で人の目や手に多くを依存しており、誤出荷などのミスが日常的に発生しています。
ハンディターミナル導入による課題解決
入出荷検品などは、ハンディターミナルを活用することで、目視や紙の記録に頼らない正確性が手に入ります。入荷時にバーコードや2次元コードを付与し、倉庫・物流センター内での管理から出荷まで共通のバーコード・2次元コードを利用すれば確実な商品管理が実現できます。また、ピッキングにおいてもハンディターミナルを用いることで経験やスキルを問わず、誰でも同じ精度・速度での作業が可能です。
代表的な工程と製造の流れ(倉庫・物流センター)
物流における具体的なハンディターミナルの導入事例を工程別に説明します。まずは倉庫・物流センター物流の代表的な工程と製造の流れは以下のようになります。

工程別 ハンディターミナル導入によるメリット
倉庫・物流センターの代表的な工程別にハンディターミナルを導入するメリット、実際の活用事例を説明します。こちらではとくに重要な工程を中心に解説します。より詳しく物流について学びたい方は、「物流効率化のキホン」を併せてご覧ください。
入荷検品
「入荷検品」は、届いた品物と一緒に送られてきた納品書を照合して品番や数量に間違いがないか、品物自体に損傷や品質異常がないかを点検する作業です。入荷検品は、目視で行うと必ず見落としや見誤りが発生し、台帳への記入漏れなどが生じやすくなります。この段階でミスが発生すると棚入れやピッキングにその間違いが引き継がれてしまい、最終的には誤出荷を招きます。この入荷検品にハンディターミナルを活用すれば、人為的なミスの多くを解消し誤出荷を防止できます。
ラベル発行
入荷の時点で商品や梱包にバーコードが付与されていない場合は、棚入れ作業が煩雑になり、格納場所を間違えるといったミスが生じやすくなります。ミスが発生すると後工程であるピッキング作業で混乱を招きます。ハンディターミナルを導入し、入荷検品データからバーコードラベルを発行・梱包単位で貼り付けておけば、効率的な棚入れ・在庫管理が可能になります。
棚入れ
棚入れと同時に前工程で作成したバーコードラベルをケースやラックに貼り付けておくことで棚入れ作業の能率が上がり、棚入れチェック(データ照合)も簡単に行えるようになります。
ピッキング
ハンディターミナルを活用すれば、ピッキングリストをスキャンするだけで商品のある棚をすぐに探し出せ、ムダな移動が減り業務の効率化が図れます。棚に貼り付けたバーコードと商品を照合できるのでピッキングミスを防ぎます。さらに記憶や経験に頼る必要がないため、経験の浅いスタッフでも現場に配置できます。
出荷検品
出荷検品のミスは、ピッキングリストや出荷指示書を見ながら作業者が目視で行ってきたことが主な原因です。その点、ハンディターミナルによるバーコード検品なら照合精度が飛躍的に向上します。また、システムとの連携により、出荷確認された商品と数量の情報はスキャンと同時にリアルタイムでシステムにフィードバックされるので、その場で正確な在庫データを把握することが可能になります。
代表的な「荷物輸送」の流れ
荷物輸送、特に宅配業務でありがちなトラブルが貨物紛失です。紛失したままで現物が出てこなければ大問題ですが、仮に紛失した貨物が見つかったとしても予定したスケジュールで荷受人の元に届かなければクレームの対象となり、信用問題に発展します。そこでハンディターミナルを活用した「荷物追跡データベース」を構築し、「集荷」から「配達完了」まですべての工程を一元的に管理できれば、どこで紛失が発生したのかがすぐに洗い出せます。
ハンディターミナルを活用した荷物追跡データベースは、貨物紛失を回避するためだけのものではありません。集荷から配達完了までの全工程でハンディターミナルから送られてくる情報を集約できるので、途中の経路にムダなどがあれば配送ルートやドライバーの配置を最適化して業務の効率化を促進することができます。また、荷受人(ユーザー)は追跡番号をネット上で検索するだけで自分に届く荷物の状況を知ることができます。また、必要なら宅配業者のサイトで配達日時を変更することも可能です。このように、荷物追跡データベースは顧客サービスを向上させるツールでもあります。

集荷
営業所に所属するドライバーがコンビニなどの取扱店を巡回して荷送人が依頼した荷物を集荷します。また、荷送人の下へ直接集荷に向かうこともあります。このとき、荷物に貼られた伝票には追跡用のバーコードが印刷されており、ドライバーは集荷ごとにハンディターミナルでスキャンします。そのデータは携帯の回線で本部に自動送信されます。また、このデータを基にハンディターミナルから小型プリンタを作動させ、配送先エリアを示す「仕分けラベル」を貼ります。

集荷降(おろし)
担当の営業所に集荷した荷を降ろすことを「集荷降」と言います。ここでも、ハンディターミナルでバーコードをスキャンすると、集荷時のデータと照合が行われ降ろした荷に過不足がないかをチェックでき、貨物紛失があればこの時点で発見できます。

積込
集荷降後の荷物はさらにハンディターミナルで送り状のバーコードと仕分けラベルのバーコードをスキャンしたうえで、配送先エリアごとにまとめられます。こうして、準備が整ったらトラックに積み込まれ目的地に向けて出発します。荷物の管理に手書きなどは一切必要がなく、すべてハンディターミナルによるスキャンだけで入力が行われるので見間違えや記入漏れといった人為的なミスが発生しません。もちろん業務の効率化も大幅に図られています。
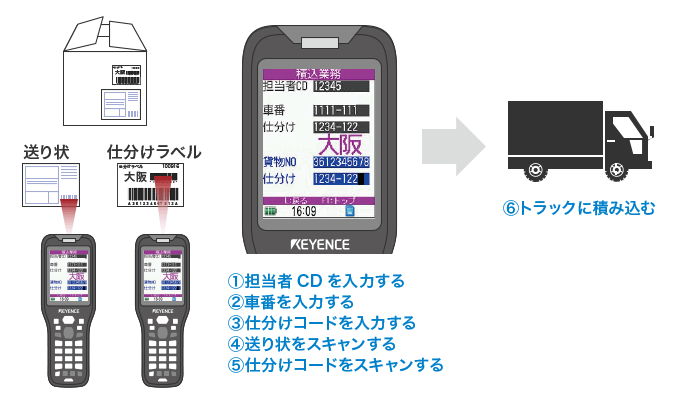
到着卸
到着地でトラックから降ろされた荷物はここでも送り状にあるバーコードをハンディターミナルでスキャンし、集荷データとの照合が行われ貨物の過不足、紛失がないかチェックが行われます。
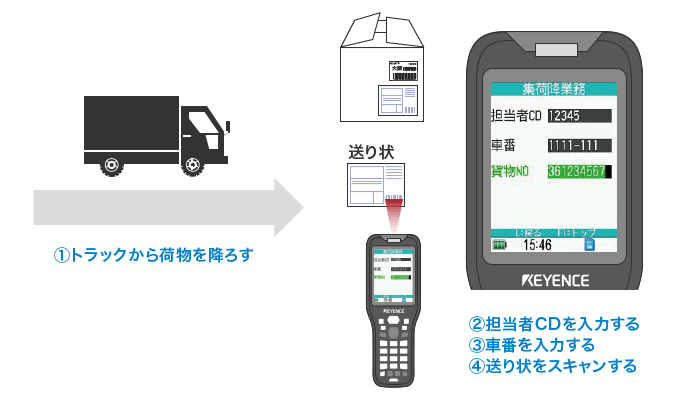
持出
到着降で荷物の状況に問題がなければ「持出」となり、荷受人の元へ配達が行われます。なお、荷受人から配達時間の変更が入った場合はすぐにドライバーのハンディターミナルへメッセージが届きます。
配達完了
荷受人の元に到着し、予定通り荷を受け渡したら、担当ドライバーが送り状をスキャンして配達完了を本部に知らせます。なお、ハンディターミナルのデータを逐一送信することで、本部はほぼリアルタイムで荷物を追跡管理できることになります。

文字認識ハンディターミナルで運用改善
物流の現場では、入庫時の現品票にバーコードがなく、シリアルNo.やロットNo.のみが記載されている場合もあります。通常、バーコードがない場合は、目視検査になりますが、似た文字列を誤認識する恐れがあり、その後の管理でシリアルNo.やロットNo.を手書きでメモしたり、パソコンに入力する際にミスすることもあります。さらにシリアルNo.やロットNo.は、その後の管理でも手間がかかります。目視検査を文字認識(OCR)に対応したハンディターミナルに置き換えることで、誤認識や入力間違えなどを大幅に削減可能で、商品管理の手間も抑えられます。キーエンスのハンディターミナル「BTシリーズ」は、文字認識(OCR)に対応しているので、以下のようなシーンで力を発揮します。
現場でラベル発行

部品や原材料の入庫時にハンディターミナルを使用しシリアルNo.やロットNo.の文字を読み取ることで、目視検査で発生する誤認識を防止できます。さらに読み取ったデータをバーコード化し、携帯プリンタで印刷して貼付することで、その後の工程をバーコード管理できます。社内システムのバーコード化を簡単・安価に始められます。
従来
- 目視チェック&パソコン手入力
改善
- 文字をスキャンするだけ。
ラクラクプリンタ発行
まとめ
このページでは、物流業界における課題と、ハンディターミナル活用による改善事例を紹介しました。まとめると以下の通りです。
- 各工程で人の目や手に多くを依存しており、誤出荷などのミスが発生しやすい
- 人的ミスを防止し、入荷/ピッキングから出荷まで確実な管理を実践するには、ハンディターミナルの活用が有効
具体的には、以下のようなメリットが得られます。
- 入荷検品時にハンディターミナルで読み取ったデータから、バーコードラベルをすぐに発行
- 梱包/ケース/棚の情報を一元管理することで、棚入れ/ピッキング作業の精度が向上
- 入荷/出荷などの情報はすぐデータに反映されるため、最新の在庫状況を把握可能
また、宅配便など「荷物輸送」においては、集荷時のバーコード発行から配達完了までのデータの一元管理とリアルタイムな追跡が実現するなど、さまざまなメリットをもたらしてくれます。
ハンディターミナルの活用方法や導入手順をまとめた資料「ハンディターミナル活用ガイド」を下記よりダウンロードいただけます。商品カタログとあわせてご覧ください。