お客様導入事例株式会社リボン 様
株式会社リボン 製造部次長 長谷川圭昭氏にUVレーザプリンタを導入した経緯とその効果について詳しく聞きました。
「生梅飴」をはじめ各種パッケージへの賞味期限印字にUVレーザプリンタを採用
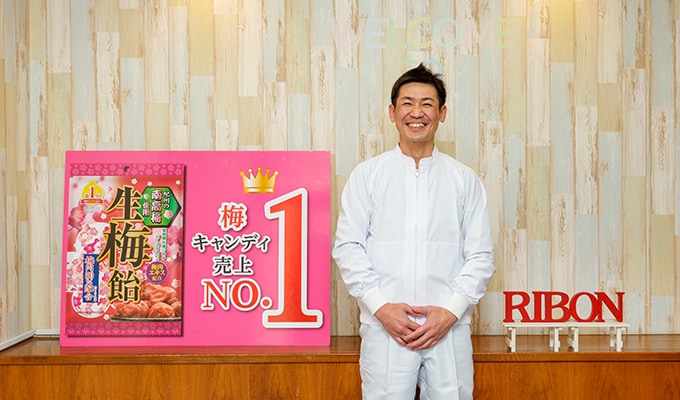
サーマルプリンタで当たり前だったあらゆる手間を、UVレーザプリンタがすべて解消してくれました。
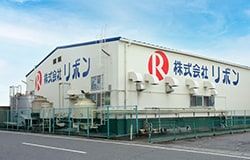
株式会社リボンについて
リボンは、「生梅飴」「北海道ソフト」をはじめ、長年にわたって愛され続けているロングセラーヒット商品を生み出している食品メーカーです。「夢とおいしさに満ちたお菓子を創造し、お客様の笑顔を通じて社員さんの幸せを実現する」を経営理念に据え、綿密な市場調査、原材料へのこだわり、新素品の開発、度重なる試作等を通じて、世の中が必要とする商品を提供し続けています。
UVレーザプリンタを検討することになった背景について教えてください
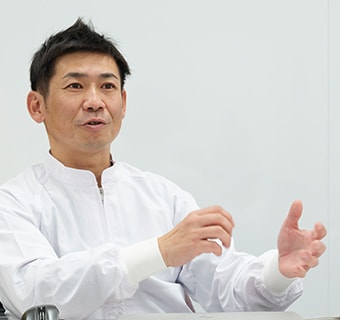
当社では従来サーマルプリンタを使用していたのですが、「メンテナンス・印字不良時のライン停止」「インクリボン管理の手間」という点において大きな課題を抱えていました。まず、「メンテナンス・印字不良時のライン停止」についてですが、当社では1日に1~2回はインクリボン交換をおこなうため、必ずその交換タイミングでは包装ラインを止める必要がありました。また、サーマルヘッドの経年劣化やヘッド詰まりなどの要因で印字不良によるライン停止も定期的に発生していたのですが、その不良の原因が何かを特定するために長い時間を要してしまうことが課題になっていました。例えば、印字された文字に線が入ってしまって検査カメラがNGを出した場合などでも、経験のある担当者であればすぐ原因を特定して対処することができるのですが、経験の浅い担当者の場合は原因特定に時間を要したり、対処できる担当者が現場に来るまで何十分もラインを止めて待ったりする状況が生まれていました。結果として、その長期ライン停止の間包装できない製品が発生するロスに繋がっていました。次に、「インクリボン管理の手間」についてですが、当社では商品ラインナップが多岐に渡る分、それぞれの包装フィルムごとに付着力の相性と消耗品コストのバランスが最適なインクリボンを選定して使用していました。その運用の中で課題だったのが、資材不足などの背景でインクリボンの供給元から、これまで使用していたインクリボンが供給停止となったりインク成分が変更となったりと、代替品のインクリボンの検証対応に追われていたことでした。当社としては、付着性などがしっかり信頼できる賞味期限印字で商品をお客様にお届けする必要がありますので、品質保証部と連携しながら新しいインクリボンを実際にラインに取り付けての試運転と擦過テストを毎回おこなっていました。
こういった対応にも多くの人手と時間を要するため負担となっていました。このような課題を解決する方法を模索する中で、キーエンスのUVレーザーによって包装フィルムに印字できることを知り検討することになりました。
UVレーザプリンタをご採用いただくまでの経緯を教えてください
UVレーザプリンタによる印字テストをおこなう中で、UVレーザーは光で印字をおこなう方式なので印字が絶対に消えないこと、そもそもインクリボンを使わないのでわずらわしい管理も、消耗品コストもかからないこと、など魅力的なメリットがあることがわかりました。ただ、検討を開始した当時はまだ包装フィルム用UVレーザプリンタが販売される前だったので、当社の縦ピロー包装機へ搭載しようとした場合、設置スペースが限られていることから、従来のタイプのレーザマーカでは大掛かりな設備工事をおこなう必要があり、なかなか導入に踏み切ることができませんでした。そんな中、キーエンスからサーマルプリンタと同じコンパクトヘッドサイズの包装フィルム用UVレーザプリンタが発売されたことがきっかけで一気に検討が進みました。今使っている包装フィルムももちろんそのままで特別なフィルムは必要なく、サーマルプリンタから置き換えるだけで導入することができました。
UVレーザプリンタ導入後の効果を教えてください
テスト段階からの期待通り、インクリボン交換によるライン停止がゼロになっただけでなく、印字不良もゼロになったことで長期ライン停止も完全に無くなりました。結果として、現在UVレーザプリンタを採用しているラインは、本来ダウンタイムが発生していた時間も生産し続けることで年間1,000万円分以上多くの商品を生産できる包装ラインに変わったことを意味しており、単なる消耗品コスト削減以上にインパクトの大きな工程改善になっております。また、これまでわずらわしかったあらゆるインクリボン管理からも解放されました。トライ&エラーを繰り返しておこなっていたインクリボンの選定だけでなく、ヘッド清掃・交換などのメンテナンス、包装ラインごとに種類が違うインクリボンの在庫管理、使用済みインクリボン廃棄など、従来必要だった作業にまったく気を遣う必要が無くなりました。包装ラインでのダウンタイムだけでなく、インクリボン管理のまつわる関連部署皆さんの仕事のダウンタイムまで無くなったことで、本来専念するべき製造ラインでの生産活動に集中できる状態に変わってきていると実感しております。

分80回転の東京自働機械製作所の縦ピロー包装機にキーエンスのUVレーザプリンタを搭載
その他、UVレーザー導入後にわかったことなどあれば教えてください
実際にUVレーザプリンタを導入したラインでは、ダウンタイムが無いことが当たり前になっており、現場スタッフの声としても「プリンタを止めなくてよくなった」と好評の声が聞こえています。従来はダウンタイムがひとたび発生すると、早くラインを復旧させないといけない緊迫感の中で、その原因となっている工程にどうしても人手と時間を割かなければいけない状況が生じていました。UVレーザプリンタに変えてからは、包装ラインのダウンタイムが無い分、現場スタッフにも気持ちの余裕が生まれて、お互いの作業の助け合い・ノウハウ共有がされやすい環境に変わっており良いスパイラルが生まれていると感じています。今回UVレーザプリンタを導入して実際に良い効果が確認できましたので、他の印字工程でも順次採用していく予定です。これまでサーマルプリンタでは当たり前だったあらゆる手間をUVレーザプリンタがすべて解消してくれました。今後も期待しています。
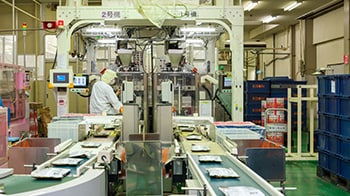
UVレーザプリンタ導入によりダウンタイムなく商品を生産できている
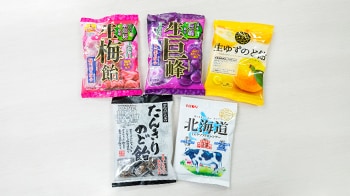
生梅飴をはじめ各種パッケージにUVレーザプリンタで
日付印字をおこなっている