レーザー溶接の原理
レーザー加工機のレーザー光は、強さやスポットの大きさを変えることで、溶接や母材表面への文字や模様の描画、切断処理などが行えます。
このうち、他の加工に使用するレーザー光に比べて極めて強いレーザー光を用い、これを熱源に母材を溶かして母材同士を接合する技術。それがレーザー溶接です。
レーザー溶接のレーザー光
溶接に使うレーザー光は、目には見えません。
レーザーを励起する媒質には、ガスや特殊な固体素材を使用します。励起して発生したレーザーをレンズで収束し、母材に当てます。このときのパワーやスポット径を変えることで、溶接以外の加工が可能になります。
マーキング
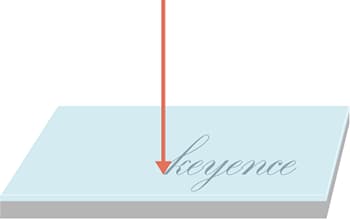
レーザー光で各種材料の表面に文字や模様などを刻む加工です。表面を熱で融解させることで刻印などの処理を行います。
溶接
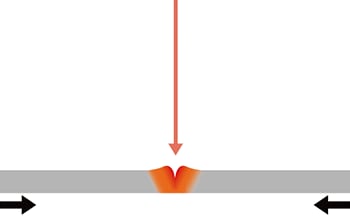
レーザー光で金属を融解させ、接合を行う加工です。通常の溶接に比べて高速で、かつ歪みの少ない溶接が実現できます。
中でもレーザー溶接に使用する高出力レーザー光は、波長・エネルギー密度といったビームの収束性、さらにレーザーの輝度やビームモード*といったレーザー光の品質を高いレベルでコントロールする必要があり、レーザー溶接が得意とする厚板から薄板にわたる微細な溶接はその実現によって可能になります。
- ※ビームモードとは? 発振器固有の光強度分布。「シングルモード(ガウスモード)」「マルチモード(多重モード)」「リングモード」などがある。レーザー溶接では、厚板で貫通溶接が必要な場合はシングルモード、ビード幅が広く深溶け込みを必要としないスポット溶接のような場合はマルチモードが有効であるとされる。
レーザー溶接機の特徴
レーザー光は、アーク溶接のアークに比べてきわめて小さく絞り込むことができます。集光レンズにより高密度化されたエネルギーで、レーザー溶接機は局所の溶接や融点の異なる材料の接合が可能です。熱影響が少なくビードは細く、加工反力も発生しないため、微細な溶接にも向いています。
- ■特徴
- レーザー光は大気中を伝送できるため、レーザー溶接の設備には電子ビーム溶接のような真空チャンバーは不要です*。電子ビーム溶接機に対してレーザー溶接機は小型で、コンピュータやロボットを利用した完全自動化と精密制御が可能です。ファイバーや伝送経路のミラーで励起装置から離れた場所で溶接することができます。これらの利点によるアプリケーションへの対応力も高く、リモートレーザー溶接やファイバレーザー溶接・ビームスキャン溶接などにより、溶接工程のさまざまなニーズに応えることができます。
クラッド鋼板の製造など、大出力レーザーを用いた一部の溶接では真空チャンバー内で溶接している。
- ■レーザー溶接機のプラズマ対策
-
レーザー照射部に存在する金属や気体の電離電圧の大きさによっては、レーザー溶接部でプラズマ(レーザー誘起プルーム)が発生する場合があります。プラズマが発生するとプラズマ内でレーザーの吸収や屈折が発生し、母材に入るレーザーパワーやエネルギー密度が低下します。これは、プラズマ内でのレーザーの吸収係数が波長の2乗に比例するためで、プラズマの状態の変化が大きい場合は溶接欠陥が発生しやすくなります。
プラズマは、電離電圧が低い金属や気体で発生しやすく、アルミニウムで約6V、鉄で約7.9Vとされています。そして、これら金属のレーザー溶接部では金属蒸気による電離が発生します。また、気体の中でもアルゴンは約15.8V、窒素は約14.5Vで、大出力のCo2レーザー溶接(炭酸ガスレーザー溶接)の場合、アルゴンガスや窒素ガスがプラズマ化します。
この現象を避けるため、電離電圧が高いヘリウムガスをアシストガスとして使用する方法が採られています。ヘリウムガスの電離電圧は約24.6Vと高く、プラズマはほとんど発生しません。溶接法によって、ヘリウムのアシストガスを溶接部の横や後ろから吹き付けることで、プラズマの発生を抑制することができます。
プラズマの発生は、溶接部を真空化することで抑制することができますが、この場合は真空化の設備が必要になります。
レーザー溶接の使用例
レーザー溶接は、アーク溶接や電子ビーム溶接に比べ、コンピュータ制御やCAD/CAMとの組み合わせが容易で、ラインへの組み込みはもちろん、ロボット化にも適した接合法です。高精度・高品質・高速・高生産性の接合法であるレーザー溶接は、高いエネルギー密度と小さなスポットという熱源の特長を活かし、自動車の外板といった大きなワークから電子部品のワイヤやピンといった微細箇所まで、幅広い分野で使用されています。


- ■自動車のフレーム/ボディーのスポット溶接
- レーザーを使ったスポット溶接では、母材の片側からレーザービームを照射して、溶接することができます。抵抗スポット溶接のように電極で母材を挟む必要がないので、ロボットアームの自由度が高く、複雑に入り組んだ場所でも溶接することができます。
- ■自動車ボディー溶接のシーム溶接化
- 高速パルスレーザーや連続発振レーザーで溶接することで、点ではなく線での溶接が可能です。線で接合することで、強度が向上し、補強用の鋼材を不要にするなど軽量化と高剛性化を実現します。
- ■電子部品のワイヤー/ピンのスポット溶接
- ビーム装置にカメラを取り付け、スポットをコンピュータ制御することで、正確に溶接点をとらえることができます。この技術により、電子部品のワイヤーやピンなどの微細溶接が可能です。
- ■電子デバイス用のセラミックパッケージの封止溶接
- 大出力のパルスレーザーの代わりに、入熱量が少ない連続発振レーザーを使うことで、変形量が小さい溶接が可能です。さらに、ろう材(溶接材:フィラーワイヤー)を用いて溶融することで、スパッタの発生を抑えることができます。
自動車車体の溶接
自動車のボディーには、商品価値のある美しいデザインと同時に強度や耐久性・防錆・衝突エネルギー耐久性・軽量性など、多くの性能が要求されます。このため、自動車のボディーに使われる鋼板は各部で厚さや材質が細かく設定されており、これらの性能を満たしたうえでの精度と生産性の向上は、自動車製造の最重要課題です。
ここでは、これらの要求に応えるべく開発され、自動車車体の溶接工程に大きな影響を与えた「テーラードブランク溶接」と「レーザーブレージング溶接」という2つの溶接法を紹介します。
- ■テーラードブランク溶接とは
-
テーラードブランク溶接は、プレス素材をプレス成形前に溶接して一枚の素材に仕上げる溶接法で、「テーラードブランク」とは複数の素材を目的に合わせて「仕立てた」プレス素材のことです。
プレス成形前に溶接し、プレス成形する。
この工法を「テーラードブランク工法」といい、主に自動車のボディーの外板製造に用いられています。- テーラードブランク工法
-
-
溶接 -
打ち抜き -
成形
-
-
- テーラードブランク溶接のメリット
-
テーラードブランク溶接による製造上のメリットとしては、複数の鋼板を1枚の鋼板に仕立てて1度にプレス成形できるためパネル数を削減でき、ボディーの精度を高めて部品点数を削減できることです。また、品質上のメリットとしては、たとえば異なる素材の鋼板を1枚の素材にできることが挙げられます。これにより、素材の最適配置が可能になり、軽量化と高剛性化など多くの要求性能を満たすことができます。
開発された当初、テーラードブランク溶接はTIG(ティグ)溶接によるサイドパネル製造に用いられていましたが、以降フロアパネルやサンルーフのリインフォース、サイドメンバからドアやサイドパネルのインナーの製造に広がってきました。なお、テーラードブランク溶接にはレーザー溶接以外にマッシュシーム溶接やプラズマ溶接が用いられ、それぞれ素材や生産性などによって使い分けられています。
-
- レーザー溶接によるテーラードブランク溶接
-
一般に、レーザー溶接のビードは幅約1mm。アーク溶接に比べ、美しい外観と熱影響による材質劣化の範囲がきわめて狭いという特長があります。溶融池は熱伝導により急速に凝固・冷却するため溶接金属は強力に焼き入れした状態になります。このため、溶接部の組織はほぼマルテンサイト*になり硬化し、強力な結合を実現します。
一方で、テーラードブランク工法では溶接後にプレス成型するため、溶接部が割れる恐れがあります。また、溶接部が周囲の鋼板より盛り上がっているとプレス金型を傷付け、その寿命が低下します。テーラードブランク溶接では、これらの問題が発生しないような技術が必要になります。
上記のような問題に対する取り組みとしては、アシストガスによるポロシティへの対策や溶接速度を調整することによるアンダーカットへの対策が講じられます。また、溶接する材料によっては溶接部や溶接熱影響部(HAZ)が割れることがあり、これに対しては、前もって発生のメカニズムや材料の特性を調査しておく必要があります。
- ※マルテンサイトとは?
- マルテンサイト変態によって生成した変態生成物のことです。マルテンサイト変態とは、せん断変形によって生じる結晶構造の変化のことで、1つの結晶は元の物質の結晶より小さくなります。これにより、結晶同士の結合が強くなり、同時に硬さが強くなります。
- ■レーザーブレージング接合とは
-
レーザーを熱源としたろう材(フィラーワイヤー)をろう付けする接合法で、レーザー溶接の欠点である溶接線のギャップへの対応性を高めた技術です。
-
- レーザーブレージングのメリット
-
一般的なレーザー溶接が「線」で接合するのに対し、レーザーブレージングは「面」で接合するため、接合部の密封性に優れています。また、低融点のろう材を使用することで、母材である鋼板をほとんど溶かすことなく接合でき、接合強度はスポット溶接の約2倍、接合速度も2倍以上の高速接合が可能です。
ろう材を使うことによるメリットは大きく、接合時の過熱および冷却時間が短くできます。たとえば、セラミックスと鋼板との異材接合で発生していた、真空炉中の炉中ろう付けでの接合素材の材質劣化はありません。また、アルミとステンレスやマグネシウム合金などの接合にも、大きなメリットがあります。
-
- レーザーブレージングを使った自動車ボディー接合
-
自動車ボディーに使われる鋼板の表面には、防錆のための亜鉛コーティング(亜鉛めっき)が施されています。レーザーブレージングは、このコーティングを傷付けることなく接合することがます。また、ルーフパネルとサイドパネルの接合では、これまでパネル同士をつないでいた樹脂部品が不要になります。この技術は、ルーフパネルとサードパネルの間はもちろん、自動車の外観各部に刻まれていたパーティングラインがなくなるというデザイン上のメリットももたらします。
高速接合と高剛性を両立し、レーザー溶接自体が持つ欠点を克服するレーザーブレージングは、商品価値のある美しいデザインと同時に強度や耐久性・防錆・衝突エネルギー耐久性・軽量性など、自動車に求められる多くの要求が作り出した接合法といえます。
-