筐体設計に3Dプリンタを使うわけ
3D-CADが一般的になり、商品設計から製造までの効率は飛躍的に向上しました。しかし、パソコンの画面上で3Dモデルを確認できるようになった今でも、手触りや組み立てなどは現物確認が必要です。特に筐体設計は、クライアントや関連部署、デザイナーやエンジニアとのコミュニケーションが大切です。そこで現物をすぐに出力できる3Dプリンタは、コミュニケーションツールとして非常に重要な役割を果たします。こちらでは、筐体設計に3Dプリンタを使うメリットやデメリットを解説します。
3Dプリンタのメリットとデメリット
特許の失効などに伴い低価格な3Dプリンタが登場したことで、導入のハードルが一気に下がることになりました。設計室に3Dプリンタを設置して、すぐに試作できる環境が整いつつあります。しかし、筐体の試作に使用するには「材料が限定される」「寸法精度が低い」といった課題を抱えています。3Dプリンタに求めている効果を得るには、メリットやデメリットを理解したうえで活用することが重要です。
- 3Dプリンタのメリット
- 金型不要で造形ができる
- 形状の自由度が高い
- 小ロットで製作できる
- 3Dプリンタのデメリット
- 材料費が高い
- 材料が限定される
- 寸法精度が低い
- 方向によって強度差がある
- 量産性が低い
筐体設計者が知っておくべき3Dプリンタの現状
1. 造形精度について
コンシューマ向けの3Dプリンタで主流の熱溶解積層方式(FDM)は、フィラメントと呼ばれる樹脂材料を熱で溶かして造形します。積層ピッチによっても異なりますが、例えば積層ピッチ0.2mmであれば、0.2mmで割り切れない数値はそのぶんだけ誤差が生じます。さらに材料を高温に熱し、冷え固めるので積層の過程で歪みが生じます。具体的には、造形モデルが冷えるときに中心に引っ張られ、両サイドに反り上がります。そのため造形精度が低く、複雑な形状の筐体になると組み付けでの使用は難しいでしょう。比較的精度の出るインクジェット方式でも反りの影響で±0.1 mm程度の誤差が生じます。
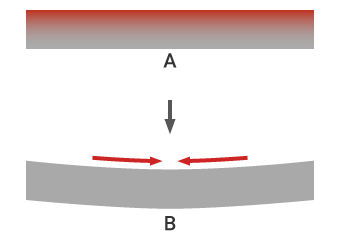
- A
- 造形中に温度差が生じる
- B
- 冷える過程で反りが発生する
2. 材料コストについて
企業向け3Dプリンタで使用する専用材料の価格は、通常の成形で使用するペレットと比較すると100倍程度の差があります。造形モデルになるモデル材のほか、型の役割をするサポート材も使用するので、金型での成形に比べると1個あたりの材料費が割高になります。
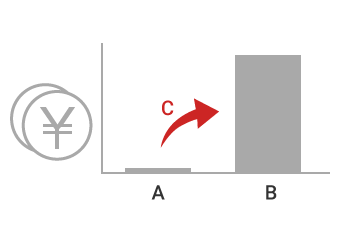
- A
- ペレット
- B
- 3Dプリンタ専用素材
- C
- 100倍
3. スピードについて
一般的な3Dプリンタは、1cm積層するのに約1時間かかります。造形モデルの大きさや形状によって異なりますが、高さ10cmのものを作るには約10時間かかることになります。3Dプリンタは、スピードと精度がトレードオフの関係になるので、どちらかを犠牲にする必要があります。スピードを優先すれば積層ピッチが広くなるので精度が下がり、精度を優先すれば積層ピッチが狭くなるのでスピードが落ちます。
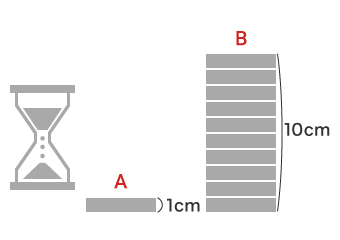
- A
- 1時間
- B
- 10時間
4. 材料について
3Dプリンタで使える材料は基本的に機種の専用材料になります。専用材料は同じ名前の材料でも、一般的な製品に使用している金属やペレットとは特性が異なります。3Dプリンタでできた造形モデルで性能評価ができないのは、このような理由からです。また、方式毎に使える材料が限定されていることも、材料面での課題と言えます。
方式 | 使える材料例 | 特長 |
---|---|---|
熱溶解方式 | ABS PLA PC | 熱可塑性の樹脂をノズルから吐出して、一筆書きで造形します。ノズル径をあまり細くできないので、0.2 mm程度の積層ピッチが一般的です。また、樹脂を高温にして造形するために、造形中の反りが比較的大きくなります。 |
レーザ粉末溶融方式 | 金属 ナイロン PP | 専用の金属粉末にレーザを照射して、焼き固めます。もともとが粉末状の材料なので表面がざらざらとした仕上がりになります。強度の高い材料を使えることがメリットになります。一方で、こちらも歪みが発生するために反りが出てしまいます。 |
光造形方式 | エポキシ アクリル | 紫外線硬化する液体材料にレーザを照射して硬めながら造形します。3Dプリンタとしては、比較的大きな造形モデルが作れることがメリットです。固めの材料が多く、靱性が不足しており、割れやすい傾向にあります。 |
面露光方式 | アクリル | 光造形のレーザをプロジェクタに置き換えて造形します。レーザのように走査させる必要がないために、スピードが早いことが特長です。しかし、分解能が限られるために、拳サイズの造形エリアになってしまいます。 |
インクジェット方式 | アクリル | インクジェットから液体のUV硬化材料を吐出して、紫外線で固めながら造形します。インクジェットの特長である少量のインクが出せることを活かして、積層ピッチが細かくできます。ただし、液体でUV硬化できる材料に限定されてしまいます。 |
前述した通り3Dプリンタでできた造形モデルでは性能評価までは行わないので、設計の検証を目的にした時には3Dプリンタの材料にこだわっても意味がなくなってしまいます。ABSなど商品に近い材料を選ぶよりも、組み付けやかん合の検証ができることが重要です。
5. 強度について
3Dプリンタは、材料を積層しながら造形するので、造形方式によっては積層境界面の結合が弱く脆いという弱点があります。ブロックが積み重なっているような状態なので、上からの衝撃には強いですが、横からの衝撃には弱くなります。残念ながら3Dプリンタの造形モデルで強度の評価は難しいと言えます。
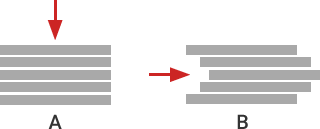
- A
- 積層方向の力には強い
- B
- 水平方向の力には弱い
3Dプリンタが筐体設計者にもたらすメリット
1. 現物でコミュニケーションが円滑になる
3Dプリンタを導入する最大のメリットは、以前であれば外部に依頼していた試作品を自社・設計部門で製作できることです。設計室に3Dプリンタがあれば、一晩で立体造形できるので、必要なときに造形モデルを作れます。
従来であれば3D-CADの画面で説明していた内容を現物で説明できるので、設計部門内はもちろん、クライアントや企画部門、デザイナーやエンジニア、製造部門や生産技術部門とのコミュニケーションが円滑になり、伝達ミスや誤解を防ぐことができます。現物を見ながら検討することで相手から多くの意見を引き出せますし、3D-CADを使っていない部署と議論もしやすくなります。

3Dプリンタの活用術は以下のページにも詳しく掲載しています。
2. 設計者への手戻りを抑えられる
現物によるコミュニケーションの円滑化は、設計精度の向上につながり、設計者への手戻りを抑える効果をもたらします。現物でレビューすることで、図面だけでは抽出できなかった課題が浮き彫りになり、早期解決につながります。さらに金型設計や製造部門への指示も現物の有無で精度が変わります。
- 設計部門内で課題を共有する
-
手戻りを抑えることは、スピーディな商品開発につながります。設計部門内でお互いの案件を共有し、誤解や見落としをなくすためには造形モデルが役立ちます。試作が手軽になれば評価の機会が増え、設計精度を高められます。
- 製造部門から問題点を引き出す
-
近年は、商品の小型・薄型・集積化が進んだことで組み立て精度が高まり、製造部門でのトラブルが増えています。造形モデルがあれば説明や検討がしやすく、図面だけでは得られない意見や要望を聞くことができ、早期に改善できます。
- 金型製作で的確な指示ができる
-
軽量化のために増えている肉薄の筐体は、金型の修正リスクが高い傾向にあります。金型の製作を依頼するときに造形モデルがあれば、業者に的確に指示でき、金型の修正も最小限に抑えられ、設計変更などの手戻りも未然に防げます。
- 実験でトラブルを早期解決する
-
筐体設計では、小型化や薄肉化が常に求められています。そんな状況で新たな機能追加の注文があれば、予期せぬトラブルがついて回ります。造形モデルがあれば、現物で実験が行え、問題の把握が早くなり、手戻りを防止できます。
手戻りが起こる原因や詳しい考え方は以下のページに掲載しています。
3. 負荷軽減で低コスト&短納期につながる
設計者は、他部門との調整業務に労力を要していますが、コミュニケーションが円滑になれば調整業務の負担が減ります。そのぶん設計業務に使うリソースが増え、設計精度を高めることができます。設計精度が高まれば、さらに手戻りも抑えられるという好循環が作れ、理想的なフロントローディングの流れを生み出すことができます。最終的に商品開発のスピードが早くなり、短納期化につながります。
設計者の負担を減らし、コスト削減と短納期化を生み出す!
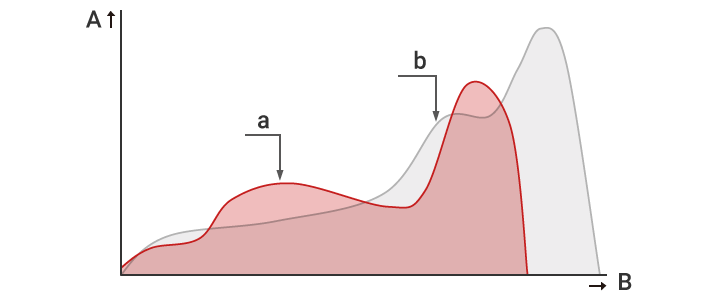
- A
- コスト
- B
- 時間
- a
- 3Dプリンタを利用した商品開発
- b
- 外部に試作を依頼する商品開発
フロントローディングの考え方については以下のページも併せてご覧ください。
試作が身近な存在になる3Dプリンタ
筐体設計に限らず、機械設計ではデザインレビューを行い、評価と修正を繰り返しながら商品化を目指します。その際に試作品を用いることで意思疎通の正確性は高まり、結果として手戻りが減り、スピーディな商品化が可能になります。

従来は、試作品のために金型を用意したり、機械加工を行ったり、外部の試作業者に依頼したりする必要があり、時間とコストがかかっていました。そのため頻繁に試作品を作り、検証することができませんでした。しかし、3Dプリンタの低価格化が進んだことで試作に対する考え方が一変します。3Dプリンタを活用すれば、コストを抑えながら数時間から一晩で造形モデルを作成でき、実物で検証を重ねながら慎重にレビューを進めることが可能です。