加工・検査・組立
「量産」のページでは、商品開発全体の量産について説明しましたが、商品と言っても筐体や内部の基盤、モーター、ソフトウェアなど多岐に渡ります。その加工や製造、検査、組立の方法もさまざまです。こちらでは筐体に注目して加工・検査・組立について説明します。
筐体の加工について
筐体の材質や形状によって加工方法はさまざまですが、こちらでは代表的な「板金加工」と「樹脂加工」について説明します。筐体の材料は、主に「金属」と「非金属」に分類されます。さらに金属は、鋼または鋼に炭素を添加した炭素鋼、クロムやニッケルを添加したステンレスなどの「鉄鋼」と、アルミニウムやニッケル、それらの金属を含んだ合金からなる「非鉄金属」の2種類に分類されます。非金属は、セラミックを代表とした「無機化学物」、プラスチックを代表とした「有機化学物」、無機化学物やプラスチック、そのほか金属などをミックスした「複合材料」の3種類に分類されます。
材料により、板金筐体やアルミ筐体、プラスチックなどの非金属を使った「樹脂筐体」などがありますが、こちらでは代表的な「板金加工」と「樹脂加工」について説明します。筐体の材料や種類について詳しくは、以下のページも併せてご覧ください。
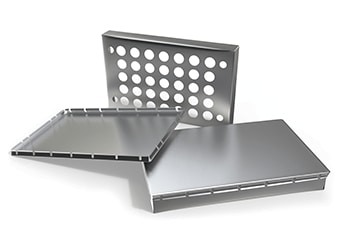
板金加工 など

射出成形 など
板金加工
金属製の筐体を作る場合は、板金加工が多く用いられます。板金加工とは、金属の板材を切断したり、曲げたり、溶接したり、表面加工を行うことで目的の形状に仕上げる加工方法です。代表的な板金加工としてプレス加工、精密板金、手板金などに分けられます。通常は、量産性に優れるプレス加工が多く用いられるので、こちらではプレス加工を用いた生産プロセスを説明します。
一般的な板金加工の流れ
材料になる金属の板材をシャーリング加工機で必要な寸法に切り出します。その後、NCタレットパンチプレスという工作機で打ち抜き加工を行います。NCタレットパンチプレスによる加工を「タレパン加工」とも呼びます。打ち抜いた板材は、ブレーキプレスという加工機で任意の形状に曲げて成形します。その後にスポット溶接などで板を接合し、必要に応じて穴開けや研磨、洗浄、塗装などを行い、筐体の完成となります。

- ①
- 板材
- ②
- シャーリング加工
- ③
- タレパン加工
- ④
- ブレーキプレス
- ⑤
- スポット溶接
- ⑥
- 穴開け・研磨
- ⑦
- 洗浄・塗装
樹脂加工
樹脂加工には、「射出成形」「ブロー成形(中空成形・吹込み成形)」「押出成形」「注型」「真空成形・圧空成型」「圧縮成形」「プレス成型」などの加工方法があります。形状や目的によって最適な加工方法を選びますが、こちらでは、筐体の加工で一般的に使われる射出成形の手順を解説します。
一般的な射出成形の流れ
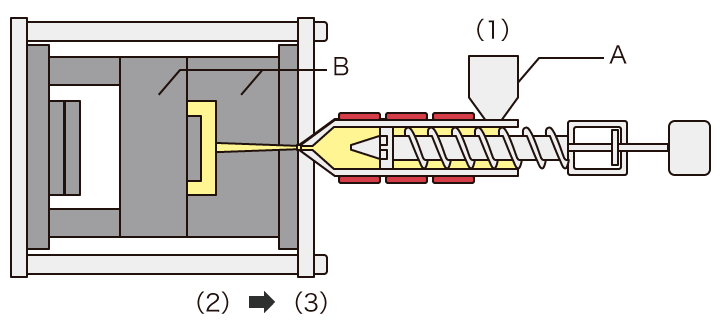
- A
- ホッパー
- B
- 金型
射出成形は、「(1)材料樹脂をホッパーから投入し、加熱溶融させ可塑化する」「(2)金型などを用いて一定の形に成形する」「(3)冷却して、金型の形状に固める」という手順で樹脂を任意の形状に加工します。複雑な形状でも高速で成形できることから大量生産品に適している加工方法で、多種多様な樹脂筐体に用いられています。また、射出成形には、「インサート成形」「多色成形・異素材成形」「加飾成形(フィルムインサート成形・フィルムインモールド成形)」などの種類があります。詳しくは以下のページをご覧ください。
筐体の検査について
加工が終わった筐体が入荷されると、図面どおりにできているか確認する「受け入れ検査」を経て、問題がなければ組立工程へ進みます。受け入れ検査とは、加工を終えた筐体の個数や形状に誤りがないか確認する作業です。通常、受け入れ検査は品質管理部門で行われ、筐体設計者が直接関わることはありません。だからといって筐体設計者は、検査しなくてもよいというわけではありません。実際に製図した筐体設計者が「図面どおりの寸法にできているか」「動作に問題はないか」「組み付けに問題はないか」を確認することで、将来の品質向上やトラブル回避につながります。
一般的な検査項目
受け入れ検査では、以下の項目を検査します。
加工依頼した数量が納品されているか
受け入れ検査では、まず加工依頼した数量が納品されているかを確認します。受け入れ検査に限らず、品番や数量の検査は基本です。近年では、トレーサビリティの観点から送り状や納品書のような紙の伝票からバーコードや二次元コードへと伝達方法が移り変わっています。

図面どおりの寸法に加工されているか
図面どおりの寸法に加工されているか、各部の長さを定規やノギス、マイクロメータ、ハイトゲージ、ダイヤルゲージなどで測定します。

図面どおりの角度に仕上がっているか
長さと同様に各部の角度を水準器や角度ブロックゲージなどで測定します。最近の製品は、小型化が進んでいるので曲げの小さなズレ、塗装や被膜の厚さの違いなども組み付け不良の要因になります。
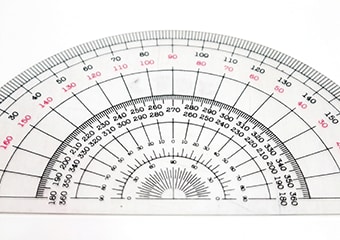
寸法公差・幾何公差に収まっているか
設計図面では、許容する誤差として「寸法公差(サイズ交差)」や「幾何公差」を指定します。寸法公差(サイズ交差)とは、文字通り各部の長さの交差です。一方で幾何公差は、形状や平行さ、傾き、位置、触れなど、製品の形・大きさ・位置関係を指す交差です。交差の測定では、隙間ゲージやブロックゲージ、三次元測定機、測定顕微鏡などを用います。
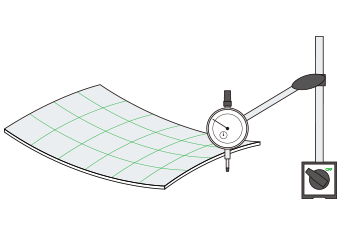
外観や表面の仕上げに問題はないか
外観のキズやバリといった不良、塗装や表面処理、表面粗さなど、外観検査を行います。外観検査は、目視などの人間の五感による官能検査を中心に、光学顕微鏡や粗さ測定器などで検査します。また、最近ではセンサや処理技術の発達により、画像処理システムで検査することも増えています。
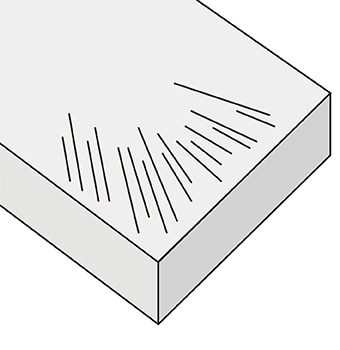
筐体の組立について
基盤やモーター、ソフトウェアなどが完成すると、筐体の中に組み付けていきます。筐体設計者の場合、3D CADを使った設計業務が中心ですが、組立作業を知ることで設計にフィードバックできることはたくさんあります。
一般的な組立のルールと設計者が知っておくべきこと
組立工程の一般常識を知ることで、より生産性に優れた筐体設計が可能になります。組立の現場で一般的なルールや起こりやすいトラブルを知れば、筐体設計の精度を高めることができます。以下はあくまで一例ですが、組立工程で気づく設計の問題は意外にも多くあります。
- 組立作業では、基本的に仮締めで放置しない
-
設計者も試作で部品の組立を行うことがありますが、そのときにはやり直しを考えて仮止めにしがちではないでしょうか?しかし、組立工程では、仮止めにすると、そのまま中途半端な状態で作業が進んでしまう可能性があるので基本NGです。組立工程も設計と同様、やり直すことが手間になるので、基本は本締めにして作業が完了してから次の工程に進みます。そのためには、設計段階で位置決めしやすいように配慮する必要もあります。
- 類似部品などは組付けミスが発生しやすい
-
設計者は、コスト削減や時間短縮のため、できるだけ共通部品を使うように設計しますが、結果として見分けにくい類似部品が増えてしまいます。例えば、左右対称に見えるが、実は穴位置が少しだけズレているなど、ちょっとした違いは組付けミスを誘発する要因です。そこで設計者は、組付けミスが発生しないように面取りを入れるなど、品番や型番だけではなく見た目で識別できる工夫を加える心遣いも大切です。それが組付けミス防止につながります。
- 短いボルトやネジは見過ごしやすい
-
ボルトやネジが長すぎる場合は、3D CAD上で干渉に気づきますが、短い場合は3D CADの干渉チェックから漏れることがあります。しかし、実際に組み立ててみるとボルト・ネジが短くて強度が不足する、生産時にボルト・ネジ等の変更が発生するといったトラブルが起こります。量産時には、ボルト・ネジが短い場合に入れ替えなどで対処しますが、短いものは組付けできてしまうので見過ごされる可能性もあります。それが後々のトラブルにつながる可能性もあるので、設計段階で注意すべき項目です。
- 組み付ける順序に左右されるケースがある
-
ネジやボルトの飛び出しなどがあると、工具が入らず組立ができないケースがあります。組立できたとしても作業手順に制約ができ、手間がかかるということはよくあることです。このような組み付ける順序に左右される設計も組立工程で気づく内容です。組付け順序に左右されるような設計は、手間が増えてコストアップにつながるので設計で配慮すべき項目です。