設計プロセスから起こりやすいトラブルとは?
商品設計の基本的な流れを理解したところで、次は実際に設計プロセスから起こりやすいトラブルについて考えます。設計にとって重要なことは、構想設計に入る準備段階と言える設計書の確定、そしてデザインレビュー(DR)の確実な実施です。しかし、「筐体ができるまで|機械設計・試作」のページでも説明したように理想的な設計フローの実施は難しく、設計書が完璧ではない状態で3D CADによるモデリングに入ってしまったり、デザインレビュー(DR)ですべての課題を洗い出すことが難しかったりというのが現状です。こちらでは、設計プロセスにおける起こりやすいトラブル事例も交えて説明します。
設計プロセスを理解する
最初に設計プロセスを再確認します。3D CADや解析ソフト(CAE)が普及する前は、2D CADで設計していました。以下は、2D CADを用いた一般的な設計プロセスです。2D CADによる設計では、評価のために試作が必要なので納期がかかり、開発期間が長くなったり、費用がかかったりという課題がありました。また、修正が発生すれば、さらにコストと時間が増大します。一方で必ず試作を行うので、より製品に近い状態で評価できるというメリットもありました。
2Dによる設計プロセス

以下は、近年一般的になっている3D CADや解析ソフト(CAE)を用いた開発プロセスです。パソコン上で3Dモデルを作成し、設計の改善や検証ができるようになり、設計プロセスは大きく変化しました。試作の回数も抑えられるので、開発期間の短縮とコスト削減にも効果的です。
解析ソフトを導入した設計プロセス
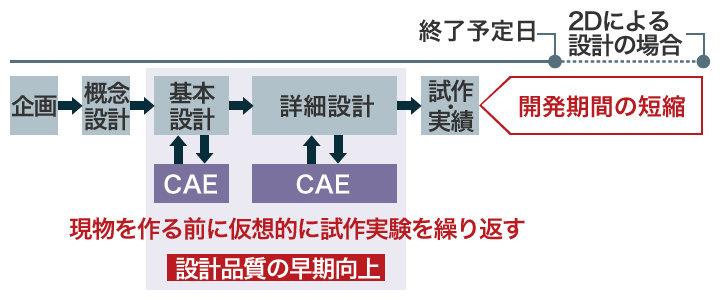
3D CADが普及したことで生まれた課題
3D CADや解析ソフト(CAE)の普及により、設計プロセスが効率的になりました。しかし、3D化が広まったことで新たな課題も生まれました。近年は、企画や構想設計の段階から3Dモデリングに入り、一番重要な設計書がおろそかになってしまうケースが増えています。また、パソコン上での3Dモデリングや検証は、ある程度の部品の干渉などは発見できますが、生産を視野に入れた設計となると経験がものを言う世界で、今でも試作による検証は必要です。
例えば、3D CAD上では手や工具などの概念がないので、生産をはじめると工作機器が入らない、組立作業ができないというトラブルもよく聞く話です。そのほかにも3D CADは厚みの変化を把握しにくく、設計難易度の高い樹脂設計でトラブルにつながるリスクも高まります。このように3D化によって便利になった反面、設計者が気をつけなければいけないことも増えています。
3D CADによるモデリングの問題例
- 組立できないものをモデリングしてしまう
- 3Dデータから造形するとイメージと異なる
- 厚みの変化がとらえにくく、成型不良の原因になる
- 強度や電気的特性(ノイズ)、放熱性など評価が難しい など
トラブルが起こる3つの要因
トラブルの多くは予測不可能なものというイメージがありますが、「新規技術」「トレードオフ」「仕様変更/部品変更など」という3つが主なトラブルの要因になります。設計者は、以下の要因を予め想定し、考えられるトラブルを予測するスキルが求められます。
新規技術
新規技術/新規設計/新規ツール/新規材料の導入、新規メーカーの採用など、今までとは異なる設計・生産手法を指します。従来と異なる設計・生産手法を用いるのでトラブルにつながる可能性が高まります。
トレードオフ
設計品質における優先順位の入れ替えです。例えば、設計初期段階の優先度は、「耐久性>低コスト」だったのに途中で「低コスト>耐久性」に変わったとしましょう。設計品質における優先順位が変われば、当たり前ですが設計や材料などの変更が発生し、手戻りとなります。
仕様変更/部品変更など
材料変更や仕入先変更、生産地変更、工程変更、担当者変更など、商品開発途中での「○○変更」です。商品開発途中での仕様変更や部品変更はよくあることですが、変更が発生すれば設計の見直しや再検証が必要になります。
よくある失敗例
設計プロセスで起こりやすいトラブルと、そのトラブルが発生する要因を理解したところで、よくある失敗例を紹介します。設計プロセスで起こるトラブルは、とても多くありますので一例ですが、設計者が配慮することでトラブルを未然に防ぐことが可能です。
失敗例1 生産プロセスからの手戻り
設計プロセスだけではなく、生産プロセスから「手戻り」が発生する可能性もあります。設計が完了し製造部門にバトンタッチしたはずが、修正が発生したという経験のある設計者も多いはずです。例えば、近年ニーズが高まる製品小型化の追求により、筐体内部に基板やハーネスを高密度で配置するケースが増加しています。その際、生産プロセスに渡ってから部品や工具の干渉で作業性が上げられないなどの問題から手戻りが発生してしまいます。そのほか、生産プロセスで機能追加が発生したり、新しい生産方法を導入したり、さまざまな要因で設計プロセスに手戻りが発生する可能性が考えられます。
失敗例2 上流工程での連携不足による設計ミス
デザイナーやエンジニア、設計者同士など、上流工程でのコミュニケーション不足や認識違いは、設計上の大きなミスにつながります。設計上のミスが見逃され、後工程で発覚すると大きな手戻りが発生します。結果として設計者には大きな負担がかかり、生産全体で見ても開発の遅れやコスト増につながります。設計自体のミスは、設計変更や金型修正に加え、納期遅れによる機会損失などの影響が出ます。
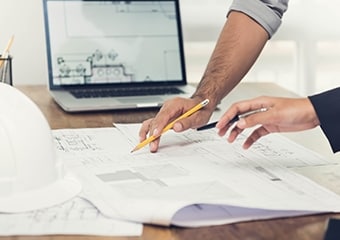
失敗例3 度重なる金型修正の発生
近年は、組み立ての難易度の高まりや軽量化を狙った薄肉の筐体の増加により、金型の修正のリスクが高まっています。金型の修正は、大きなコストと時間がかかり、修正できない場合は設計から見直すケースもあります。しかし、肉厚やリブなどは図面だけで正確に伝えることが難しく、結果的に金型修正を繰り返すケースも珍しくありません。また、樹脂成形品の設計難易度は高く、ヒケなどが発生する可能性も予測しておく必要があります。
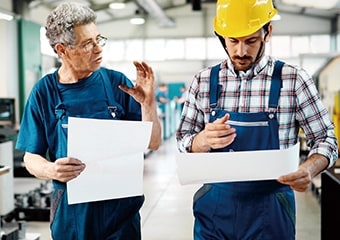
解決策 試作品を使って現状と課題を共有する

「手戻り」を防止するには、お互いが進めている作業を正確に共有し、誤解や見落としをなくすことが大切です。そのためには、まずデザインレビュー(DR)で確実に課題を抽出し、設計段階で修正することが重要です。
しかし、現実問題としてデザインレビュー(DR)で完全に不具合を見つけ出すことは困難です。3D CADのデータでは、見落としも発生しやすく、意思疎通が難しいこともあります。3D CADや解析ソフト(CAE)を活用するだけではなく、手に取って確認できる試作品があると非常に役立ちます。
まずはデザインレビュー(DR)の確実な実施が最優先ですが、それでもトラブルが発生する場合は試作頻度を増やすことも有効です。試作の頻度を増やすことで、課題はどこにあるのかを話し合いをして、誤解や見落としをなくすことができます。
現状と課題の共有は、上流工程の中だけではなく、製造部門や金型設計を行う協力会社とも積極的に行うことが大切です。試作品で組み立て方法やツメの位置などを正確に伝えることで、図面だけでは伝わらない細部の情報も共有できます。詳しくは以下のページをご覧ください。
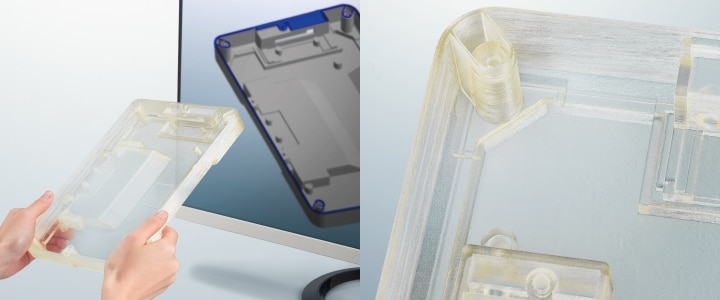
失敗しないためには上流での試作が重要
開発コストは、設計初期段階に70%が決まると言われており、商品企画や構想設計は非常に重要なプロセスです。そこで顧客・影響・開発・製造など商品開発に関わるメンバーと意思疎通を図りながら進めるコンカレント・エンジニアリングの重要性が認識されつつあります。3Dプリンタの造形モデルを利用すれば、デザイン性・操作性・形状を評価する頻度を増やし、後工程での手戻りの発生を減らすことができます。3D CADや解析ソフト(CAE)の普及で実物を使わなくても検証が可能になりましたが、試作品による検証とうまく使い分けることで手戻りを減らし、コスト削減を実現します。
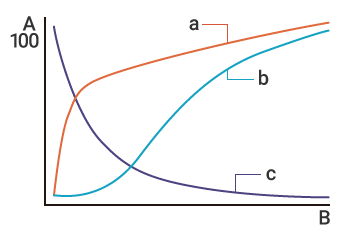
- A
- コスト(%)
- B
- 工程
- a
- コストの決定度
- b
- 発生するコスト
- c
- 変更の容易さ
また、上流での試作の頻度を増やすことで、設計初期段階に重点を置き、作業を前倒しで進める「フロントローディング」にもつながります。さらに詳しい設計初期段階のプロセスについては次のページで詳しく解説します。