試作の課題と3Dプリンタ活用術
失敗しない筐体設計の考え方として、設計書やデザインレビュー(DR)の重要性について説明しました。しかし、実際には、設計書やデザインレビュー(DR)に時間と手間をかけられないという設計者や企業も多いでしょう。設計書の決定プロセス強化やデザインレビュー(DR)の質を高めるには、設計フローや商品開発体制の変更など、企業全体で取り組む必要があり、すぐに実現が難しいというのが現実です。
その課題解決として工程内での試作が挙げられます。工程内で試作を行うことで、早期に課題抽出ができ、設計品質を高めて後工程でのトラブルを減らせます。3D CADで把握が難しい形状や厚みも試作品なら一目瞭然で、関連部署・業務委託先との意思疎通にも効果を発揮します。
従来であれば外注に依頼していた試作品も、3Dプリンタを利用することで時間とコストという問題も解決できます。試作における時間とコストという課題を解決し、スピーディに試作を実施する手段として3Dプリンタが効果的です。こちらでは、試作で重要なスピードと精度、そして3Dプリンタの活用術を紹介します。
- 試作を外注する場合の問題点
- 試作の課題を解決する3Dプリンタ
- 3Dプリンタは設計現場にあってこそ
- 試作のスピードアップ=商品開発期間の短縮
- 高精度な試作=品質の向上
- 高速かつ高精度な3Dプリンタ「アジリスタ」
試作を外注する場合の問題点
試作を外注して行う場合、時間とコストがかかるので頻繁に実施することが困難です。例えば、以下のような課題に頭を悩ませる設計者も多いのではないでしょうか?
- 上長の外注承認を得ることが難しい
- 購買に対して見積り依頼する手間がかかる
- 外注用に図面に落とし込む必要がある
- 依頼してから納期がかかる など
特に短納期化と低価格化が求められる現代の商品開発では「試作品で検証したいけど時間とコストの問題で難しい」と諦めてしまうことも少なくありません。
本当は試作を行うべきところでも、3D CADや解析ソフト(CAE)によるパソコン上での検証だけで済ませてしまい、後から問題が発覚することになってしまいます。
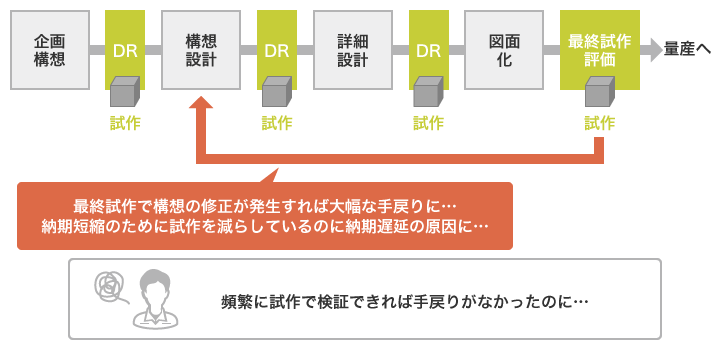
試作を最小限に抑えた結果、最終試作で修正が入り、大幅な手戻りになってしまった、というケースがあります。これでは、設計段階で3D CADや解析ソフト(CAE)を使い、試作を最小限に抑えた意味がありません。設計者としては、「デザインレビュー(DR)以外にも細かく試作品でレビューできれば、修正を抑えられたのに……」という思いがあるでしょう。かといって、前述した通り頻繁に試作を外注することはなかなか困難だというのが現状です。
試作の課題を解決する3Dプリンタ
外注に試作依頼する場合、時間とコストという制約がのしかかります。これを解決する手段が3Dプリンタです。3Dプリンタを活用すれば、3D CADデータをもとにすぐ造形モデルを作成でき、実物で検証ができます。従来の外注による試作の制約を受けず、「デザインレビュー(DR)以外にも試作品で検証できれば手戻りがなかったのに……」というジレンマが解消でき、設計品質を高めることができます。
以下は3Dプリンタを活用し、あらかじめチーム・部署内で造形モデルによる簡易レビューを行い、次工程に進んだ一例です。構想設計部分のみをピックアップしていますが、企画構想・詳細設計・図面化などでも同様に、各工程内で造形モデルを用い検証することで、手戻りや試作の作り直しを最小限に抑えることが可能です。
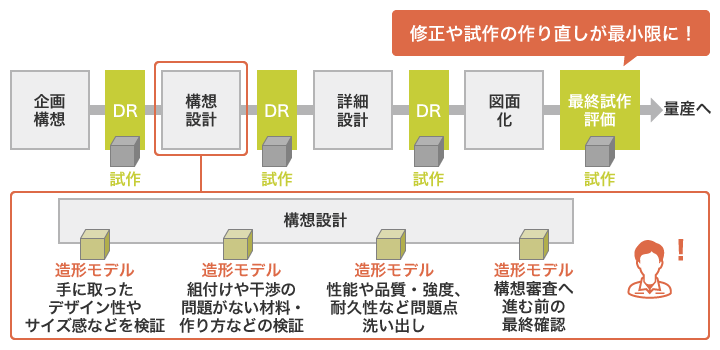
3Dプリンタは設計現場にあってこそ
3Dプリンタを導入していても、他部署や生産現場にしか設置していない場合があります。使用許可を得るのに時間がかかったり手続きが面倒だったりして、頻繁に使用できない…ということもしばしば。使いたい時に使えなければ、外注する場合とほとんど変わりません。3Dプリンタは設計現場に1台設置していればすぐに活用でき、結果として手戻りの無駄を省くことが出来るので便利です。
また、3Dプリンタがあれば、試作の課題を解決できるというわけではありません。試作はスピードと精度が重要です。3Dプリンタで念入りに検証した結果、商品開発結果が長くなってしまえば意味がありませんし、検証に耐えうる造形モデルでなければ意味がありません。3Dプリンタを試作で用いる場合は、スピードと精度を考慮した機種選択が必要です。
試作のスピードアップ=商品開発期間の短縮
近年は、高精度・低価格な3Dプリンタが登場し、手軽に試作ができるようになりました。デスクトップ3Dプリンタなら設計した3Dデータをすぐに出力することもできます。設計と試作・レビュー・評価を同時進行できることが3Dプリンタの魅力です。
外注を利用して試作品を入手する場合、発注の手間などから現物評価の頻度が減ってしまいます。3Dプリンタを導入すれば、現物評価を短いスパンで行うことができ、手戻りを低減できます。結果としてフロントローディングの実現につながり、商品開発のスピードは加速します。
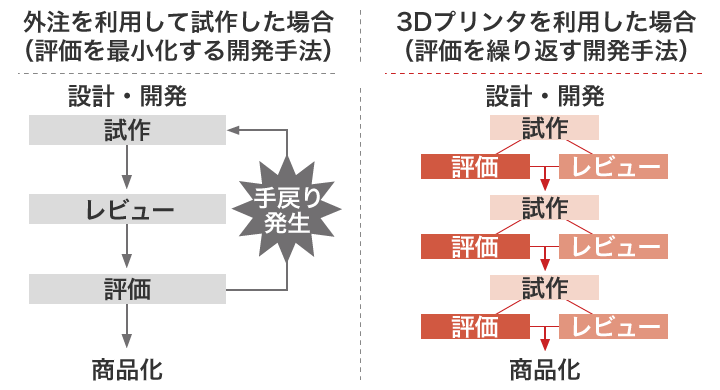
キーエンスの3Dプリンタ「アジリスタ」はインクジェット方式を採用しました。一度に256個のノズルから面になって材料を吐出し、高精度を維持しながら素早く造形モデルの出力が可能です。設計の検証に最適な3Dプリンタです。
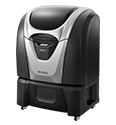
高精度な試作=品質の向上
試作のスピードアップには3Dプリンタが有効になります。広く普及しているデスクトップ3Dプリンタは、多くの場合に熱溶解方式(FDM)を採用しています。シンプルな構造で設置場所を選ばずに使えることが特長です。しかし、精度に関しては積層ピッチが0.1~0.2mm程度と粗いため、多くは大きさや形状を確認するために使われています。
また、デスクトップタイプに限らず、3Dプリンタの造形モデルはネジ締めは苦手でタップを切ると割れてしまうことがほとんどでした。3Dプリンタで組み付けまで確認するには、精度も靱性も足りていませんでした。
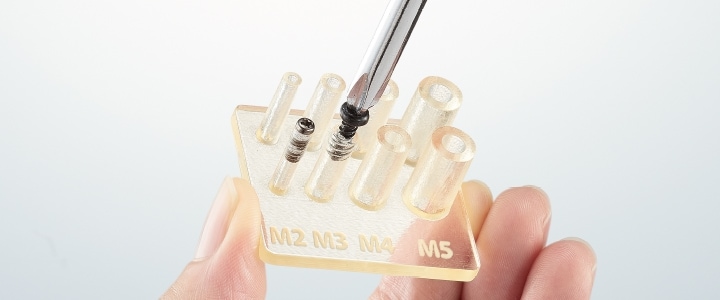
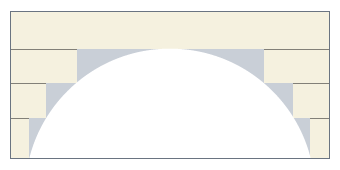
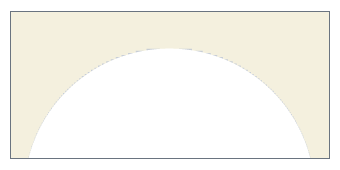
キーエンスの3Dプリンタ「アジリスタ」は、高精度なインクジェット方式を採用し、積層ピッチ15μmを実現しています。組み付けしてもカチッとはまる精度で、組立性の検証も十分可能です。靱性があるのでネジ締めもでき、半透明の樹脂を使うので内部まで見やすいことも特長です。

高速かつ高精度な3Dプリンタ「アジリスタ」
キーエンスの3Dプリンタ「アジリスタ」は、15μmという積層ピッチを誇り、商品開発における細部の検証にも使用できる精度を実現しています。水溶性サポート材を採用しているのでサポート材除去の手間も少なく、靭性と透明性を兼ね備えた材料はネジ占めやかん合、内部の流体シミュレーションなどにも対応した試作評価に最適な3Dプリンタです。
その精度を維持しながら高速に造形が可能なので、試作のスピードが飛躍的に向上。 3D CADで制作したデータからすぐに造形モデルを用意できるので、試作評価はもちろん、チーム・部内での検証などにも力を発揮。従来は手間と時間、そしてコストのかかった試作の概念が変わります。
設計者として、設計書やデザインレビュー(DR)の精度を高めることが大前提ですが、それを補うためには試作が欠かせません。設計プロセスの改善と併せて3Dプリンタの活用もご検討ください。
次のページからは、3Dプリンタを使用した筐体設計をより詳しく解説します。キーエンスの3Dプリンタ「アジリスタ」は、精度や靱性のほかにも筐体設計者の負担を少なくする機能が満載です。
詳しくはインクジェット方式3Dプリンタ「アジリスタ」のカタログをご覧ください。
まだアジリスタが誕生する前、キーエンスのデザイン部が、実際にどのようなきっかけで3Dプリンタを導入したのか、そして現在のアジリスタ開発に至ったのかがわかるページもあわせてご覧ください。