機械設計・試作
商品設計における機械設計・試作について説明します。「機械設計の外殻を担う筐体設計」のページでも説明していますが、筐体設計は機械設計に含まれます。
機械設計の基本的な流れ
機械設計の基本的な流れは、「構想設計」「詳細設計」「生産設計」と、各段階でレビューを行う「デザインレビュー(DR)」で構成されます。デザインレビュー(DR)では、筐体設計を含む構造設計と機構設計を行う「機械設計」、そのほか「電気設計」「ソフトウェア設計」を担当する設計者をはじめ、営業・企画・生産などの責任者が集まり、それぞれの立場で品質やデザイン、生産性などを評価します。機械設計は、設計とデザインレビュー(DR)による評価・承認を繰り返しながら次のステップに進みます。こちらでは、まず機械設計の基本的な流れを紹介します。
- 構想設計
-
設計の基礎になるものが「構想設計」です。全体のレイアウトや重要機能部品の構想、QCD(品質・コスト・納期)を考慮しながら構想設計を進めます。
- デザインレビュー(DR)
-
設計の各段階では、デザインレビュー(DR)を実施し、意匠や設計に問題はないか、コストや納期は予定どおりに収まるかなどを検討し、都度修正を加えます。
- 詳細設計
-
詳細設計では、構想設計をもとに図面を作成します。必要に応じて試作品を準備し、都度確認や検証も実施します。
デザインレビュー(DR)
- 生産設計
-
生産設計は、実際に生産を行う工場の意見を聞きながら設計を行います。工場視点で設計を見直すことで、部品・工程の共通化、部品点数の削減などが可能になります。
構想設計に入る事前準備について
近年は3D CADの普及により、早い段階でモデリングに入る傾向がありますが、そこには落とし穴があります。商品の仕様が詰まってない段階で、3DCADを使ってモデリングを始めてしまうと、さまざまなトラブルが発生することがあります。トラブルを防ぐために重要になるのが構想設計に入る事前準備です。すぐに3Dモデリングに入らず、設計書に落とし込んでから3D CADによるモデリングを実施すべきです。早い段階から3D CADを使うことで起こるトラブルなどは以下のページに詳しく紹介していますので併せてご確認ください。

事前準備をしっかりする理想的なフローと事前準備をおろそかにしてしまう曖昧なフローの違いは以下のページで詳しくご説明しています。失敗しないプロセスをしっかり確立させましょう。
図面作成
製品を正確に表す最も簡単な方法が図面です。図面を作る工程を「製図」といい、決められた規格や様式に沿って形状・寸法・材料・仕上げの程度・工程・質感などの情報を図面に書き起こしていきます。製図には、共通のルールがあるので、設計者はルールを熟知し、正確・明瞭・迅速に製図することが求められます。
製図後の手戻りは、大きな手間となるので、構想設計の段階でスペースや構成部品に問題はないか、見積もりを出してコストが要求に収まっているか、組み立てや加工で問題が出ないかを十分に検討します。後工程になればなるほど手戻りの負担が大きくなるので、構想設計でQCDの目処をつけてから図面作成に進むことが重要です。
評価・デザインレビュー
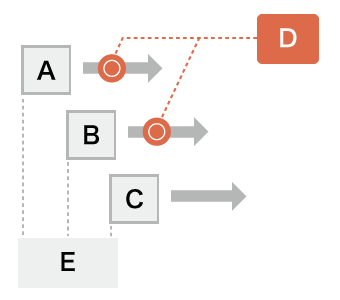
- A
- 構想設計
- B
- 詳細設計
- C
- 生産設計
- D
- デザインレビュー
- E
- 生産サイクルの短縮やフロントローディングのために設計が同時進行する
各段階で設計者と各部門の専門家や責任者が集まり、設計を評価する場を「デザインレビュー(DR:Design Review)」と言います。デザインレビュー(DR)は、日本語で「設計審査」とも呼び、集まった専門家や責任者がそれぞれの立場で品質やデザイン、生産性などを評価し、不適合があれば修正等の提案をします。
デザインレビュー(DR)の主な目的は、
①設計上のトラブルを早期発見する
②トラブル対策を実施して設計の後戻りやトラブルを防ぐ
③品質を確保して業務効率を高める
という3つです。
デザインレビュー(DR)で重要なことは、設計トラブルを後工程に流さないことです。デザインレビュー (DR)は、一般的に構想設計、基本設計、詳細設計、試作・評価などの各工程毎に行われます。デザインレビューでの承認がなければ先に進めず、指摘があれば対策や修正を施す必要があります。
また、近年は生産サイクルの短縮やフロントローディングのため、「企画設計」「詳細設計」「生産設計」を並行して行うケースが増えています。一般的には、各フェーズ毎にデザインレビューを実施しますが、企画設計のデザインレビュー時に詳細設計や生産設計を意識していく必要もあります。

- A
- コスト
- B
- プロジェクトの進行
- C
- ピークを前倒しに
- B1
- 企画
- B2
- 基本計画
- B3
- 実施設計
- B4
- 製造
- B5
- 維持管理
- a
- 変更しやすさ
- b
- 理想的設計業務量
- c
- 変更にかかるコスト
- d
- 現状の設計業務量
試作を増やすことが時間短縮に?
近年は、3D CADや解析ソフト(CAE)が一般的になり、コンピュータの画面上で確認・検証をすることが増えています。しかし、コンピュータの画面上では組付け具合や他部品との干渉など、わかりづらいことが多く、不具合が見逃されがちです。
そのままデザインレビュー(DR)へ進んでしまうとそこで初めて問題が発覚し、手戻りとなります。もちろんデザインレビュー(DR)もやり直しです。
設計フェーズ内でも試作をすることで意思疎通が図りやすくなり、不具合の早期発見につながります。

そこで3Dプリンタなどの活用が増えています。3Dプリンタがあれば、構想設計や詳細設計など各フェーズの中で簡易的に造形モデルを用意でき、設計初期段階で課題を洗い出すことにより、設計精度を高めることができます。質の高い状態でデザインレビューへ進めることで具体的な審議が可能です。結果としてデザインレビューからの手戻りも減り、時間短縮へとつながるのです。詳しくは以下のページもご覧ください。