省エネの流れ
省エネを実施する流れについて説明します。省エネと言っても照明のスイッチを消すといった今日から始められるものから、設備の入れ替えといったコストのかかるものまでさまざまです。そこで最初にどんな省エネを実施すべきか検討し、計画的に進めることが大切です。
省エネもPDCAが重要
省エネは、コストとのバランスが非常に難しく、しっかりと計画して実行しなければ思うような結果が得られないばかりか、大きな損失を生み出す可能性もあります。そこで重要なことがエネルギー使用量を管理して、省エネのPCDAサイクルを推進して無駄のない対策を行うことです。
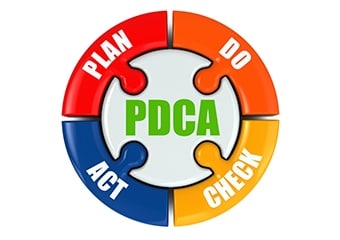
省エネのPDCAサイクル
PLAN
- エネルギー使用状況の把握
- 省エネできる項目の選定
- 省エネ施策の検討・選定
DO
- 省エネ施策の予測と体制整備
- 実施に向けた準備
- 省エネ施策の実施
ACTION
- 省エネ施策の見直し
- 管理方法の見直し
- 追加施策の考察
CHECK
- 進捗状況の確認
- 実施状況の管理
- 省エネ施策の効果検証
現在のエネルギー使用量を知る
省エネに必要な確認項目を洗い出し、資料収集(使用量・料金単価・設備運用管理データ・マニュアル・図面など)、現場調査(設備確認・エネルギー使用量の測定・運用確認など)を行い、エネルギー使用状況を把握します。その後にエネルギー使用量や運用状況を評価し、省エネできる項目を洗い出します。
- 確認項目の洗い出し
-
エネルギーが使用されている工程や場所を特定します。
- 資料収集
-
確認項目に関連する資料(使用量・料金単価・設備運用管理データ・マニュアル・図面など)を集めます。
- 現場調査
-
実際の現場で使われている設備や運用方法を確認し、エネルギー使用量を測定します。
- エネルギー使用量の見える化
-
生産設備に取り付けたモニタリング機器でデータを収集し、運転状況などと関連付けてエネルギー使用量の見える化をします。
基準値を決める
省エネ施策を実行する前に基準値を決めます。日本の場合、エネルギー消費量を「原単位」で管理するケースが多くなっています。原単位とは、一定量の生産物をつくるために使用する、または排出するものや時間などの量を指し、英語で「Intensity」と呼びます。一定量の生産物を作るのに必要なエネルギーのことを「エネルギー原単位」、一定量の生産物をつくる過程で排出する二酸化炭素排出量を「排出量原単位」と言います。原単位の対義語として、最近では「総量( Absolute Volume )」もよく使用されます。原単位や総量など詳しくは以下のページをご確認ください。
省エネできるところを突き止める
収集したデータからエネルギーの過失(漏れ)や過剰使用部位を発見し、最適な省エネ施策を検討します。運用改善や設備投資などの方法を検討し、メリットやデメリット、費用対効果などを考慮し、最終的に実施する省エネ施策を決定します。
- エネルギー使用量の評価
-
データを収集し、エネルギー使用量を把握・評価します。
- 運用方法の評価
-
設備の運転や清掃、保守など運用方法に問題はないか評価します。
- 省エネできる箇所・項目の検討
-
設備性能・設備の運転状況・設置場所・過剰設備・使用時間・運転効率・エネルギー損失・排熱利用などから省エネできる箇所・項目を洗い出します。
- 省エネ施策の検討
-
洗い出した箇所・項目ごとに省エネ施策を検討します。
- 運用改善
-
- 設備運転の最適化(作業時間や待機時間の短縮、保守点検による効率アップなど)
- 工程の合理化
- 加工方法の合理化
- 排熱の回収利用 など
- 設備投資
-
- 高効率な設備・機器の導入
- 生産ラインの改修 など
- 省エネ実施計画の策定
-
検討した省エネ施策のメリット・デメリット、運用変更によるリスク、設備投資の費用、費用対効果を検討し、実施する施策を選定します。選定した省エネ施策は、具体的な省エネ実施計画に落とし込み、実施体制の検証、資金計画の作成などを行い実行に移します。
省エネ施策を実施する
運用・測定・保守点検のルールの整備、管理ツールの整備、運用改善マニュアルの作成、設備投資などの準備を経て、省エネ施策を実施します。
効果検証でPDCAサイクルを回す
省エネ施策を実施したら、エネルギー使用量を測定・管理し、効果測定を実施します。目標との差や運用状況の確認、新規設備の運転状況などを確認し、現場の声を聞きながら効果測定します。効果測定後、省エネ施策や管理方法の見直し、新たな省エネ施策の追加などを行いながら、常に改善に取り組むことが重要です。