カーボンニュートラルを目指す製造業の取り組み
すでに、各業界の製造部門ではカーボンニュートラルの実現に向けて、さまざまな取り組みが始まっています。特に、工場などの産業部門は発電所の次に多くのCO2を排出しているといわれており、これをいかに抑えることができるかが課題となっています。
ここでは、各業界がカーボンニュートラルを実現するために導入している技術や課題を紹介。さらに、製造現場でのカーボンニュートラル実現に向けた取り組みや、具体的な事例を紹介します。
- 製造業におけるカーボンニュートラルとは
- カーボンニュートラル達成のためのPDCA
- EnpI/FEMSの導入
- 各業界のカーボンニュートラルへの取り組み
- 製造業が抱えるカーボンニュートラル実現の課題
- 産業・業務部門における省エネの課題
- 見える化・わかる化事例集
製造業におけるカーボンニュートラルとは
製造業が環境に与える負荷には、製品を製造しているとき(生産過程)と製品が顧客の手に渡った後(使用過程)があります。このうち、生産過程で発生する環境負荷には工場廃棄物や電気・ガス・石油などのエネルギーの使用で発生する温室効果ガスによる大気汚染、水質汚染や騒音などがあります。
全産業における製造業のCO2排出量の割り合いは約25%と大きく、世界が脱炭素社会を目指す中で、製造業の脱炭素への方針転換が強く求められています。
一般的な工場では電気使用量のうち多くが生産設備であり、カーボンニュートラルを達成するには、電力のカーボンニュートラル化と生産設備の省電力化が最も効果的です。たとえば、電力源を再生可能エネルギーなどに切り換え、また生産設備を省電力なものに切り換えることは、カーボンニュートラルを達成するために欠かせない取り組みです。しかし、電力のカーボンニュートラル化には電気料金高騰の恐れがあり、また生産設備を省電力化するには膨大なコストと労力が必要であり、現実的とはいえないことも事実です。
そこで、既存生産設備から発生しているロスや使用電力量の抑制、電力会社の見直しなどが、製造業にとって現実的なカーボンニュートラルへの取り組みであるといえます。
カーボンニュートラル達成のためのPDCA
カーボンニュートラル達成への取り組みは、常にコストと効果のバランスを確認しながら進めなければなりません。間違った計画のまま実行すると、大きな損失を生み出す可能性もあります。そのためには「計画⇒実行⇒評価⇒改善」のサイクルを継続的に促す技法であるPDCAが有効です。
具体的には、工場全体でカーボンニュートラル化のPDCAサイクルを推進して無駄のない対策を行うことが重要です。カーボンニュートラル化のPDCAサイクルを以下に示します。
- ①Plan:現状把握と実施計画
-
エネルギーが使用されている工程や場所、エネルギーの使用状況を把握し、省エネできる項目を洗い出して各項目への取り組みを検討します。検討した項目の中からメリットやデメリット、経営状況などを考慮し、実施する取り組みを選定します。
- ②Do:取り組み実施
-
部門代表の選定、全員参加型の体制整備など、取り組みごとに実施体制を整備し、進捗状況を管理します。同時に、達成の基準となる値(基準値)も設定します。
- ③Check:効果検証
-
実際の現場で使われている生産設備やその運用方法を確認し、エネルギー使用量を測定します。生産設備に取り付けたセンサなどのモニタリング機器でデータを収集し、運転状況などと関連付けてエネルギー使用量の見える化し効果を測定します。
- ④Action:計画見直し
-
目標との差や運用状況、新規設備の運転状況などを確認し、現場の声を聞きながら取り組みや管理方法の見直し、新たな省エネ施策の追加などを検討します。
EnpI/FEMSの導入
PDCAを実施するには、工場内のエネルギーの使用状況を定量化し、把握する必要があります。その手段としては、EnPIによる指標化とFEMS(Factory Energy Management System)導入による問題点の抽出が欠かせません。ここではこの2つの手段のメリットについて説明します。
EnpI導入のメリット
EnpIとは、エネルギー性能指標ともいわれ、「組織が定めたエネルギー性能の定量的な値」です。エネルギー性能を測る尺度であると考えることができます。エネルギー性能とは、エネルギー使用量やエネルギー効率に関連する測定可能な結果と定義されています。
具体的にはエネルギー使用量(GJやkWh)・ピーク電力(kW)・用途別エネルギー消費量・各種のエネルギー効率(エネルギー消費原単位・エネルギー変換効率)などがあります。これらは、組織における立場によって使い分けられます。
たとえば、特定の製品群の売り上げや利益、投資コストの責任者であるビジネスユニット(BU)長は、エネルギー使用量やエネルギー原単位を用います。また、製造部ではエネルギー使用量の過去比較やエネルギー原単位を用います。
このように、EnpIを導入することで、工場内のそれぞれの立場と目的に応じた値を設定することが可能になり、それぞれの立場で効果を検討することができるようになります。
FEMS導入のメリット
FEMSとは、工場の受配電設備・生産設備のエネルギー管理・使用状況の把握・機器の制御を行う工場エネルギー管理システムのことです。
FEMSを導入すると、機器の不必要な稼働やエネルギーを過大に消費している機器を特定することができます。その結果から、余計に消費されているエネルギーを抑制したり、他の機器のエネルギーに回したりといったことが可能になります。
また、FEMSはエネルギーの使用状況を数値やグラフなどで見える化でき、エネルギー原単位(単位エネルギー使用量に対するエネルギーの使用量)の算出なども可能です。
FEMSは、「本当に必要な設備なのか」、「不要時には設備を停止しているか」、「過大な負荷がかかっている設備はないか」といった既存設備の状況把握から、省エネ設備への転換の可能性の検討まで、カーボンニュートラル実現に向けた取り組みを幅広くサポートするシステムといえます。
各業界のカーボンニュートラルへの取り組み
すでに、各業界にはFEMSを導入し、カーボンニュートラル実現へと動き始めている企業が多くあります。ここでは、その中から代表的な業界・分野の省エネによるカーボンニュートラルへの取り組みを紹介します。
化学品製造プロセス
エネルギーのうち、有効に使えるエネルギーをエクセルギーまたは有効エネルギーといい、有効に使えないエネルギーを「エクセルギー損失」といいます。現在、化学品製造プロセスでは、エクセルギー損失を最小化すべく、以下の取り組みを実施しています。
- 熱分解工程の触媒分解プロセスへの転換
- 熱利用の多い蒸留工程への無機多孔体膜プロセスの導入
- バイオマス資源や高濃度CO2の原料利用
また、蒸留分離プロセス向けの無機多孔体膜技術や、熱分解触媒の開発も進められています。さらに、バイオマスやCO2を原料として化学品・工業製品などを生産することで、カーボンニュートラルを実現し、資源循環型の社会づくりに貢献することを目指しています。
鉄鋼プロセス
鉄鋼プロセスでは、高炉製鉄の工程でCO2の排出量が大きく、課題とされてきました。製鉄時、コークスを用いて酸化鉄の状態になっている鉄鉱石から鉄分子を抽出する際に、残りの酸素とコークスの炭素が結合することで大量のCO2が排出されます。また、高炉では炉内を高温にするための燃料からも、多くのCO2が排出されます。
この問題に対し、鉄鋼メーカーでは以下のような取り組みを実施しています。
- 高炉の排気口へのCCUS設備の設置
- 電炉製鋼法の導入
「CCUS」は、「Carbon dioxide Capture, Utilization and Storage」の略で、排出ガスから分離・貯留したCO2を利用する技術です。CCUS設備は、 CO2が大気に放出される前に回収する装置です。
CCUSには「水素還元方式」や「溶融酸化物電気分解法」があります。水素還元方式は、コークスのかわりに水素を用い、酸化鉄から酸素を分離し水素と結合させることで排出ガスを水に変える技術です。一方、溶融酸化物電気分解法は、酸化鉄に電子を当てて酸素イオンを分離し鉄分子を抽出する方法で、排出されるのは酸素のみです。
しかし、いずれの方法も鉄鉱石を採掘する際に発生する温室効果ガスを抑制することはできません。このため、鉄を鉄鉱石から作るのではなく、廃棄された鉄をリサイクルする電炉製鋼法といわれる方法に注目が集まっています。
電炉製鋼法では、廃棄された鉄を高温で溶融し不純物を除去することで、高品質な鉄を作り出すことができます。鉄を高温にする際に大きな電力が必要になりますが、それでも鉄鉱石の採掘から製鉄までに発生するCO2の量に比べれば、はるかに少なく抑えることができるとされています。
エネルギー転換・供給分野
工場では、電気や燃料などさまざまなエネルギーを蒸気や冷水に変換して利用しています。多くの場合、蒸気や冷水は配管を通じて生産プロセスに供給されます。このようなエネルギーの供給方式では、大量の低温排熱の放出や蒸気の供給ロスやエクセルギー損失が発生します。この問題を解決する技術が「ヒートポンプ」です。ヒートポンプは圧縮と膨張によって温度が変わる気体の性質を活用した技術で、エネルギー転換・供給において以下のようなメリットがあります。
- 低温排熱のリサイクル利用が可能
- 蒸気の供給ロスを削減
- 生産プロセスに合わせた熱供給が可能
- 温水と冷水の同時供給が可能
また、電力の使用は熱を運ぶ動力に限られるので、少ない電力で大きな熱を利用することができます。ヒートポンプは、必要なエネルギーが少なくて済むのでガスや石油による燃焼方式に比べてCO2排出量の大幅削減、省ランニングコストのシステムが構築できます。
部材加工プロセス
旋削加工やプレス加工業界ではコンプレッサや空調・照明・生産動力に多くのエネルギーを使用します。たとえば、各プロセスで使用するエアはコンプレッサ室から供給しますが、配管からのエアのモレや配管レイアウトによるエア供給圧力のロスなどをチェックし、修理・対策を行います。また、コンプレッサをインバータタイプに置き換え消費電力を抑えるなどの省エネ対策も行われています。
機械加工機などの生産動力については、段取り中など加工していない間は、油圧ポンプ・コンベアなどの補機類を停止したり、油圧ユニットのインバータ化、チップコンベアの間欠運転、流量計による各種流体の流量管理などが行われています。
たとえば、マシニングセンタでは、加工ワークと工具との摩擦を軽減し、過熱を防ぐ切削油(クーラント)を使用します。切削油の流量や濃度を管理し噴出量を最適化することで切削油のロスをなくし、切りくず回収の手間を軽減し、エネルギーロスの低減と作業効率の向上を実現することができます。
さらに、最新のマシニングセンタとしては、切削油を霧状(ミスト)にして少量のクーラントで加工をするセミドライ加工(MQL)が可能なものや、スタートとストップを繰り返す主軸にストップ時の負荷で発電する電源回生技術を用いたものがあります。
半導体プロセス
半導体プロセスのクリーンルームでは、室内清浄度や温湿度などの環境維持、生産設備に電力や超純水などを供給するための付帯設備が必要です。これらを運転し維持するためには、多くの燃料や電気が消費されます。半導体プロセスでは、全消費電力のうち約40%が生産設備であり、同じく約40%が空調設備といわれています。したがって、半導体プロセスの省エネ対策は、生産設備と付帯設備の両方で行う必要があります。
生産設備での省エネ対策は、主にプロセス条件の最適化と生産設備の排熱改善に分けられます。プロセス条件の最適化は「スタンバイブロー」といわれる洗浄待ちの間に流れる純水の排出量の削減と、水処理工程のプロセス排気の風量の削減により可能です。
付帯設備での省エネは、送風機と送水ポンプのインバータ化や圧力センサによる回転制御・高効率送風機や冷凍機の導入などにより可能です。また、プロセス排気の空調用へのリサイクルも冷熱源の電力エネルギーの削減に有効とされています。
製造業が抱えるカーボンニュートラル実現の課題
今や製造業にとって、カーボンニュートラル実現に向けた取り組みは不可欠です。しかし、中小企業への支援は不透明であり、省エネに対する財政面やモチベーションの維持など製造業が抱える問題は少なくありません。一般に中小企業が抱えるカーボンニュートラル実現への課題は、以下の2種類に大別できます。
費用対効果とモチベーションの維持
CO2排出量の削減は、費用対効果の高いものから順次選択していくことになります。このため、目標とするCO2削減量が大きくなるほど、 CO2の削減に必要な費用が増加することになります。
また、グリーン成長戦略におけるCO2排出削減目標は、2018年から2030年までの削減ペースに比べ、2030年以降の削減ペースが加速する見通しになっています。このため、特に2030年以降のカーボンニュートラル実現への投資費用の増加が企業にとって大きな負担になると予想されています。
さらに、現場では省エネの効果がわかりにくく、「モチベーションが上がらない」、「部署間での省エネ効果の責任が不明確で、取り組みが進まない」といった課題も多く見られます。
イニシャルコストの捻出
中小企業では、イニシャルコストの負担が大きい省エネ設備への投資は容易ではありません。既存設備が老朽化している場合の省エネ機器への切り換えも同様です。政府による経済的支援の時期も内容も不透明な今、既存設備の改修・補修で事業を継続したいという要望が大半を占めています。
老朽化した設備を最新の省エネ機能を備えた設備に置き換えることは、コストもさることながら、製造システム全体の調和の面でも大きなハードルがあります。また、省エネ自体が生み出す利益も不透明です。このような状況では、既存設備の省エネ化が最も合理的な取り組みであるといえます。
現場でできるカーボンニュートラルへの取り組み
前述のような状況から、中小の製造業におけるカーボンニュートラルへの取り組みは、既存設備のロスを検出して対応し、エネルギーをムダなく活用できるシステムの導入が鍵になります。
そこで、低コストで容易に取り組むことができ、成果が見込めるカーボンニュートラル実現プランを紹介します。
取り組み-1:見える化
- 取り組みのポイント:
-
- 測定による現状の把握
- 問題または課題の顕在化
CO2の削減は、装置単独の改善で成し遂げることは困難です。むしろ、コンプレッサからの配管など、工場全体に影響する設備の改善が有効です。それにはまず、装置の温度や配管の流量・圧力を各種センサで測定し、正確な値を知り現状を把握することが欠かせません。
コンプレッサは正常に動作しているか、配管にモレがないか、過剰な圧力がかかっていないか、流量・使用量は適切かといったことを測定できるセンサの導入による見える化が、カーボンニュートラル実現への第一歩となります。
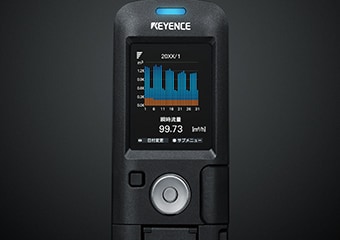
取り組み-2:わかる化
- 取り組みのポイント:
-
- 測定データと設備稼働状況の関連付け
- エネルギー原単位の算出
取り組み-2では、取り組み-1で明らかとなった問題点が、設備の稼働に与えている状況を認識しやすい形で表示します。
各種センサから収集した測定データをPLC(シーケンサ)で解析し、生産数に対するエネルギーの消費量をエネルギー原単位として表示します。これにより、設備の稼働状況を分析し問題点とエネルギー消費の関係を明らかにすることができます。
また、エネルギー原単位を知ることは、カーボンニュートラル達成に向けたPDCAサイクル活動の効果検証にとっても、重要なデータとなります。
見える化・わかる化事例集
カーボンニュートラルを実現するには、現状のエネルギーの使用状態を把握することが最も重要です。 たとえば、工場で使用する熱や圧力エネルギーは、ボイラーやポンプ、コンプレッサから配管を通じて各工程に供給されます。配管を流れる流体は、適切な温度・流量でなければならず、それには流量管理が欠かせません。
ここでは、流量管理の課題と対策を紹介します。
圧縮エア費用の見える化
- [課題]
-
圧縮エアは、コンプレッサルームから各工場建屋に供給しています。必要な圧縮エアの量は建屋によってさまざまなので、供給量を最適化しなければなりません。また、省エネに向けた改善活動を進めるには、各工場建屋の圧縮エアの費用を算出しなければなりません。しかし、従来各建屋への圧縮エアの供給量は把握できておらず、費用換算ができていませんでした。
- [対策]
-
各工場建屋への配管に流量計を設置し、圧縮エアの流量を測定して使用量を見える化します。建屋の使用量から費用を算出することができるので、建屋ごとの削減目標が設定できるほか、供給量の最適化を図る対策に役立てることができます。さらに、コンプレッサの吐出量を管理することで、コンプレッサの性能劣化を早期発見・メンテナンスすることができます。
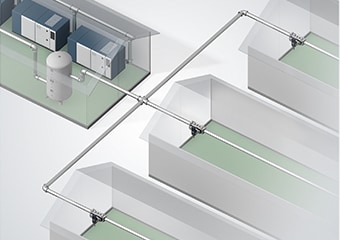
キーエンスのクランプオン式気体流量計「FD-Gシリーズ」なら、20A~200Aに対応しているので、コンプレッサやレシーバタンクにつながる大口径の配管から、装置への供給に使われる小口径の配管まで幅広い口径に取り付け・測定が可能。建屋はもちろん、ラインごとに流量管理し、費用に換算することできめ細かなコスト削減・省エネに取り組むことができます。
また、配管を共振させる超音波「ガイド波」を採用。クランプオン式でありながら、気体への高い超音波透過性を実現しています。
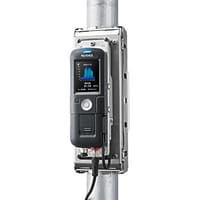
工場給水・排水配管流量の見える化
- [課題]
-
切削や冷却用に使用した工業用水の排水処理後の再循環水・下水などは循環ポンプや排水ポンプで給水・排水します。しかし、従来、詳しい循環水・下水量は把握されておらず、具体的な省エネ対策が出せずにいました。このため、水量が変化した場合にポンプ給水や排水が追い付かなかったり、不要な運転により電力のロスが発生している可能性がありました。
- [対策]
-
再循環水や下水の配管に流量計を設置して流量を見える化することで、ポンプの運転時間の調整や、稼働台数の最適化が可能になります。また、再循環水・下水の流量を管理することで、工場全体での水の使用量を把握でき、給排水の利用制限をする、運転時間を調整する、ポンプの稼働台数を制限するといった省エネ対策に役立てることができます。さらに、インバータポンプなら、流量計で測定した値を基に、動作を制御することも可能です。
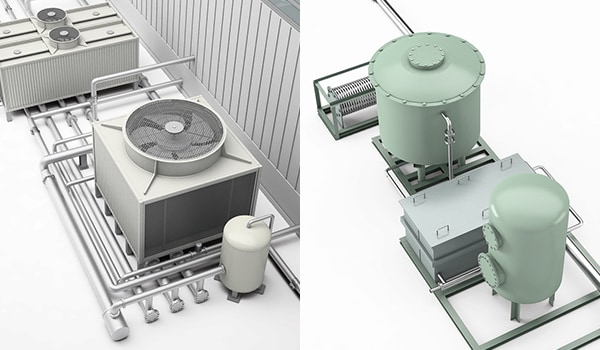
キーエンスのクランプオン式流量計「FD-Rシリーズ」なら、水はもちろん油や薬品など、さまざまな液体を検出することができます。
接液しないクランプオン式のため、液体による腐食や劣化、圧力損失の心配がなく経済的です。高圧流体も検出でき、超音波を伝達する材質であればどのような配管材質でも検出可能です。また、配線を切断せずに挟み込むだけで流量測定ができるので、設置の手間もかかりません。
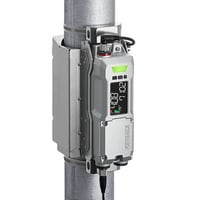
圧縮エアのモレの見える化
- [課題]
-
圧縮エアのモレ(リーク)は目に見えず、特に危険がないためこれまでは放置されるケースが多くありました。しかし、リークはコンプレッサの負担となるばかりではなく、電気や燃料などのエネルギーの大きな浪費につながります。また、圧縮エアはコンプレッサ棟で作られ、工場建屋に供給しているため、分岐配管でリークが発生している場合、従来の計測方法では確認できません。さらに、配管には大口径から小口径まであり、最適な流量計の選択に苦慮していました。
- [対策]
-
工場建屋の圧縮エアのモレを確認するには、建屋内の各配管に流量計を設置してエアの流量を測定します。各配管の流量データを比較し、異常な流量が検出された配管にはモレがあるため、対策を行います。コンプレッサの吐出量のうち、10%~20%はモレているとの報告もあるため、この対策の効果は大きいといえます。
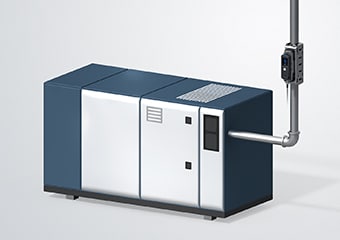
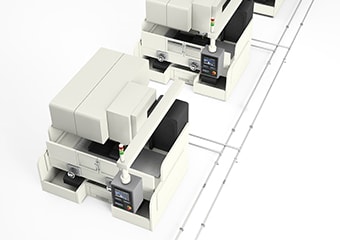
キーエンスのクランプオン式気体流量計「FD-Gシリーズ」は、20A~200Aの配管に対応しています。大口径配管の流量も小口径配管の流量も把握することができるので、工場全体での圧縮エアの使用量を把握できます。
また、分岐配管の流量を測定することで、建物・ラインごとに流量管理し、費用に換算することができます。
さらにクランプオン式でありながら測定精度2.0% of RD※を実現。最小感度流量0.03m3/hで測定でき、わずかなリークも捉えることができます。
※ キーエンス規定条件での値です。
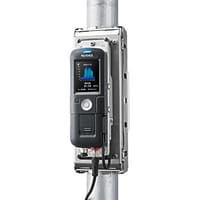
消費エネルギーのわかる化
- [課題]
-
流量計で測定した値からエネルギー消費量を分析してコストダウンを図るには、 エネルギー原単位や稼働時間当たりのエネルギー消費量の算出が必要です。
それには流量の把握だけでは不十分であり、より高度なエネルギー管理による消費エネルギーのわかる化が必要です。
- [対策]
-
稼働率を上げてエネルギー原単位や稼働時間当たりのエネルギー消費量を下げるなど省エネ化によるコストダウンは、現在の工程の稼働状態を把握し過去との差を確認、逐次対策を講じることで実現します。それには、ロス解析やエネルギー監視が可能なPLCの導入が最適です。
キーエンスのプログラマブルコントローラ「KVシリーズ」なら、フィールドネットワークを介して各種センサを接続し、さまざまな情報を集約・管理できます。たとえば、流量計と「KVシリーズ」を組み合わせることで、CO2の排出量をモニタしたり、エネルギー原単位を算出したりといった、エネルギー監視が可能になります。また、流量のOK/NG判定だけでなく、積算流量、アラーム情報まで取得できます。さらに、複数のセンサを監視できるため、最適な流量になっているかを一元監視することもできます。
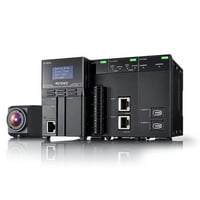